PVC Project
commissioned by Musica vzw (2015-2017)
- P: Polyphonic / Polyfoon / Projekt / Plastiek
/ Plastisch
- V: Versatile, Variable, Verplaatsbaar
- C: Contraption , Concertinstallatie/ Concertinstrument
/ Concertant
Description
The idea is to design and build a modular yet consistent instrument
using PVC material that could be played by many children in togetherness.
The instrument should be transportable in a small van and mounting
complexity should be low and take up a minimum of time. Sturdiness
is essential as well as safety. Weather resistance was also a design
issue.
- - 24 drumpipes / klopbuizen (tunable to many systems) Two modules,
each one and a half octave.
- - 2 Intonarumori (friction drums derived from noise makers as
build by Luigi Russolo)
- - 4 Kalliopes (derived from the design of 19th century steam
whistles)
- - 2 Singing Bicycles (an invention by Godfried-Willem Raes)
adapted to use on modified home trainers
- - 2 jumping rods (threaded rods mounted on a membrane, on which
rings can rotate by gravity)
- - 1 large friction drum (derived from instruments such as the
quica, rommelpot, Waldteufel, Loewengebruell etc...)
- - Whispers (Cavity resonators)
- - Log drums
- - Rommelpotten
- - Balg of pomp gestuurde schuiffluiten
Realisation / Realisatie:
1.- Twee modules met elk 12 klopbuizen voorzien van opzetstukken
waarmee de tonen kunnen worden gekozen. Bij elke module hoort een
houder voor de ping pong paletten voorzien van een speciale laag
zacht neopreen.
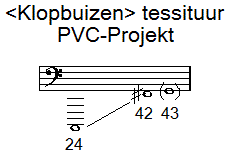
2.- Twee Intonarumori instrumenten met membraan, spanmekanisme
en door een zwengel bediend strijkwiel.
3.- Een module met vier kalliopes voorzien van vier balgen en verbonden
met witte flexibele PVC buizen. De module is in hoogte verstelbaar.
4.- Twee home-trainer zingende fietsen, elk met twee resonantiebuizen
in PVC
5.- Twee draadstang modules met membraan ringschrijven en omkeermekaniek.
(omgebouwd tot rommelpotten in 2017)
6.- Twee rommelpotten (2017)
7.- Vier schuiffluitmodules (2017)
Earlier projects and compositions by Godfried-Willem Raes using
PVC pipes:
Collaborators in the realisation and construction of this project:
- Mattias Parent (PVC research and construction)
- Laura Maes (project supervision)
- Godfried-Willem Raes (metal and welding works, structural design,
research)
Construction diary:
15.07.2014: Sketches for what mechanisms could be made using PVC
pipes:
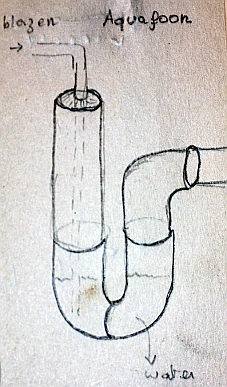
01-16.02.2015: Experiments carried out with different kinds of
PVC. The idea to make PVC logdrums came out to be unworkable. So
this design was cancelled from the list of possibilities.
17-18.02.2015: Construction of drums using large diameter PVC pipes
by Mattias Parent. Although this works very well, we did not preserve
them in the final project by lack of originality. The drums may
be modified to large lions roars later.
21.02.2015:Construction of an experimental giant whisper, using
vinyl LP records 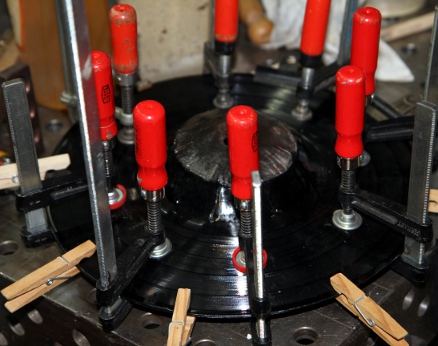
02.05.2015: Singing bicyle, with two tones mounted on a home trainer: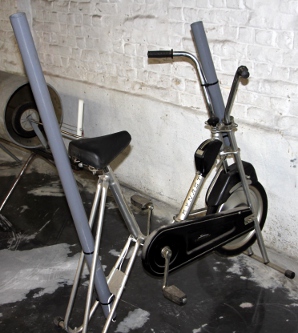
25.05.2015: Scale 1:1 technical drawing made for the construction
of the intonarumori.
26.05.2015: Welded base and mechanics for the first intonarumori
instrument, using 400 mm diameter thick PVC pipe:
Here is a detail of the crank and the friction wheel:
The legs are made from two lengths of 1 m 1/2" gaspipe, bend
under 90 degrees using the Ridgid hydraulic pump and welded to the
base 50x30x3 profile. The PVC pipe mounts on the stand with three
M12 bolts.
27-28.05.2015: Further work on the string tending mechanism in
nylon and definitive mounting of the crank. Definitive studbolt
mounted for limitation of the range for the tending mechanism.
30.05.2015: A new load of PVC pipe cames flowing in... 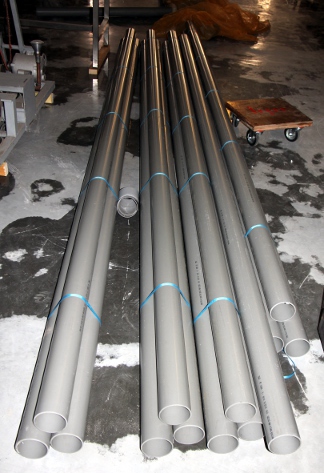
02-04.05.2015: Construction of the bellows for the kalliopes
06-07.05.2015: Construction of the second intonarumori instrument.
10-15.06.2015: Cutting, drilling and TIG-welding works on the hexagonal
holding structures for the tube resonators. Each module will hold
12 tubes, 90 mm in diameter. The diameter of the complete module
will become 1100 mm. There are two such modules, so in total 24
tubes.

16.06.2014: Mounting of the PVC tubes in the structure.
The first of these modules is ready and playable... Welding of the
T-stands for the two jumping rods. (50x30x3 steel and 25x25x1.5)
The distance
holder rods between the stands still has to be welded in. We first
have to know how to rotate the mechanism.
17.06.2015: Different kinds of neoprene and rubbers tested for
the construction of the playing pallets.
18.06.2015: Two modules ready. All exchangeable pipe lengths sawn
off and tuned. Design alternatives for the kalliopes drawn out and
studied.
19.06.2015: Welding and final construction works on the second
intonarumori instrument. This will be made from orange sewer pipe
PVC,
20.06.2015: Sawing, precision drilling and welding of the steel
holder for the four kalliopes.
These will be mounted on a sturdy tripod such that the height can
be adjusted. The kalliopes are mounted on the structure in a vertical
position.
21.06.2015: Painting of the welded construction. Mounting of the
kalliopes.
Construction and adjustment of the mounting brackets. First tests
with the bellows.
22.06.2015: Finalising the construction of the threaded rod instruments:
clamping mechanism and welding of the studs connecting both T's
pieces. The painting still has to be done.
And here
is a picture of both beat-tube/ drum-pipemodules together: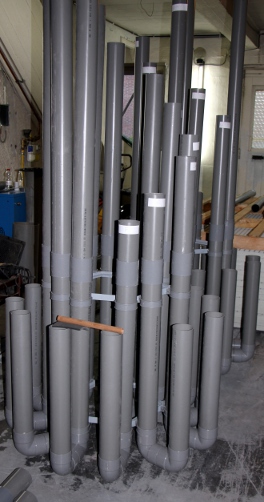
23.06.2015: Finishing of the second intonarumori instrument.
24.06.2015: Final painting of all modules. Construction of the
beaters for the drum-tubes. Instrumental setup demonstration for
Musica.
25.06.2015: Printing of the labels with the pitches for the pipes.
Further construction of playing pallets. Design and construction
of two holders for the ping-pong pallets.
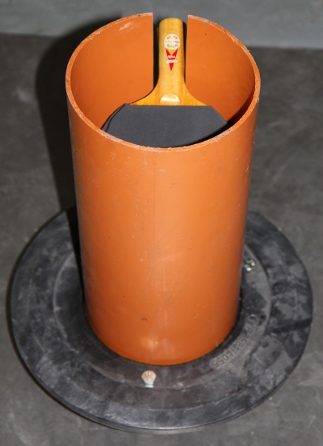
26.06.2015: Transport of the project to Musica in Limburg. Setup
and installation Laura Maes and Mattias Parent at Alden Biesen.
Some issues to be remedied are: the bikes are too loud in comparisson
to the other modules. The threaded rods are too gentle. The first
issue can be solved by placing a series resistor in the wires to
the speakers. The second one, to replace the ring with heavier ones
and to exchange the membrane with styrofoam.
28.06.2015: Premiere of the project at AlbaNova organized by Musica
at Alden Biesen.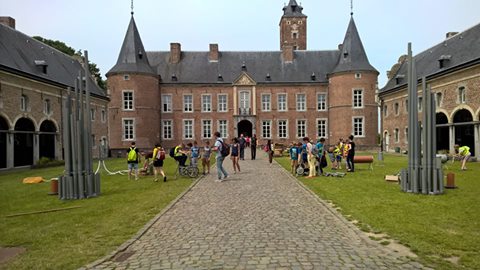
2016: Parkbos installatie: 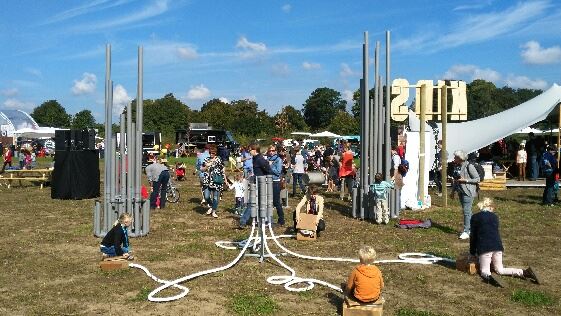
}10-13.08.2017: Construction of two easy to play lions roar modules:
[Konstruktie van twee rommelpotten:|
These use a wooden wheel with bow rosin (collophonium)
14.08-18.08.2017: {Konstruktie van de eerste twee schuiffluit modules:}
Construction of the two
highest bellow-blown slide whistle modules. Although it would have
been a lot easier to just make mouth blown slide whistles, we rejected
the idea for hygienic reasons. The bellows use Jobe double action
hand pumps. Due to the fact that their wind outlet is in de handgrip,
we had to mount them upside down. These bellows have 2 x 2 liter
air content, this allowing pretty long sustained notes. Maximum
air pressure is 1.9 Bar. The PVC pipes for the flutes are 25 mm
in diameter. The sliding end-stop plunger is made of Epramid staff
material, turned to size on the lathe. Here are some details:
19.08.2017: Design of the lower slide whistles. Here we are using
much larger pumps. So we selected Quechua pumps with an air content
of 5.2 liters. The flue pipes in this case were a lot more difficult
to make, as we had to make the slide-piece and the flute block completely
from scratch. In fact we used a piece of aluminum tube turned on
the lathe and filled with epoxy rosin (Seno 4046, produced for the
encapsulation of electronic circuits). The epoxy compound needs
24 hours to cure, so we had to interrupt the works and just wait...
20.08.2017: Further construction of the slide whistles.The bass
whistle uses a PVC tube, 40 mm x 1.8. The sliding plunger thus has
to be just a bit (ca. 0.2 mm) smaller than 36.4 mm. This plunger
was fabricated using aluminum tube filled with epoxy rosin. The
result is not too great, as gently sliding remains problematic,
even when greased with vaselin. Apparently the PVC tube itself is
not pure cilindric... The larger pumps used to drive this whistle
give some problems as well, as their movement is not very fluent
neither. They do not seem to work as well on low pressures as the
Jobe pumps used for the smaller pipes.
21.08.2017: Construction of handgrips for the large red pumps, as
their diameter is too large to be easily taken by childrens hands.
The grips made of Teflon (PTFE), giving a very smooth and nice feel.
Here are two pictures:
22.08.2017: Construction of the tenor slide whistle. Here we will
use 30 mm diameter PVC pipe. The slider can be made from massive
brass rod, 28 mm diameter. The block for the flue is made from massive
PVC and turned to size on the lathe. The grid used for this module
will be green glassfibre fabric. The blocks preventing sideways
movement of the pump are made from massive 30 mm thick PVC material.
This is certainly an improvement over earlier designs, although
more expensive to fabricate.
23.08.2017: Finishing the tenor slide whistle. Construction of the
pumps handle. Construction of the slide mechanism with aluminum
handle. Construction of the end-stop with venting holes. Construction
and mounting of the fingerboard.
All four
slide whistles are now ready to be presented by Musica...
24.08.2017: All four whistles delivered to Musica.
15.10.2017: slide mechanisms improved on the slide whistles.
Todo: add musical scales to the fingerboards on the slide whistle
modules
|