Pitched
Percussion Robot
|
<Tubo>
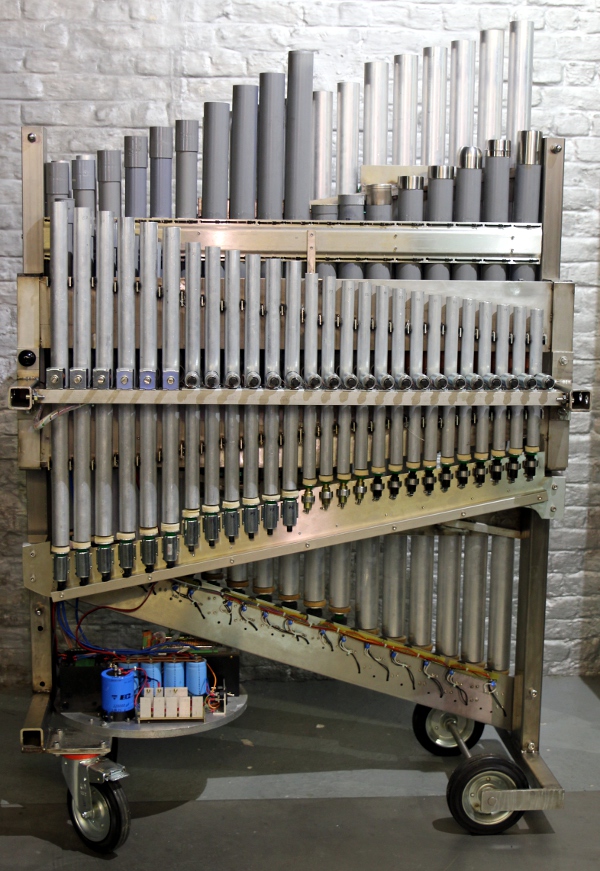
Godfried-Willem
RAES
2019 /
2020
|
<Tubo>
Aluminum tubes were used in earlier robots such as our <Tubi>,
a quartertone instrument. In 2019, we did build the
Plus-Minus project, using aluminum tube of greater thickness. Extending
the register on the low side, appeared impossible using the same type of tube.
When the tubes are made longer, the second overtone becomes dominant. Hence
the idea to apply mensuring on the proportions. Thus this instrument uses aluminum
pipes of different diameters. The tube lenghts can be calculated using following
formula, valid as long as the tube length is at least 10 times larger than the
diameter.
The frequency
for the first overtone, given by Olson as 2.758 times the fundamental frequency,
after our measurements, it ought to be 2.705 times the fundamental. This is
the pitch perceived on the attack of the tube. It can be measured exactly by
suspending the tube exactly in the centre, the first overtone having a node
there.
Note that the modulus of elasticity (Youngs modulus) is temperature dependent.
This curve illustrates this dependency for aluminum:
The variation is quite small, but when tuning, one has to be carefull to cool
the tubes to ambient temperature before checking the pitch. Grinding and sanding
makes the tubes very hot... A bucket of cold water next to the sander is of
great help here.
The alloy used for the tubes is AlMgSi 0.5 F22 (Werkstof nummer: 3.3206, International
6063)
The composition is: 0.3-0.6% Si , 0.1-0.3% Fe, 0.1% Cu, 0.1% Mn, 0.35-0.6%
Mg, 0.05% Cr, 0.15% Zn, 0.15% Ti, 0.15% other elements, saldo to make 100% is
Al
An alternative alloy is AlMgSi 1 (Werkstof nummer: 3.2315, international 6082)
Composition: 0.7-1.3% Si , 0.5% Fe, 0.1% Cu, 0.4-1% Mn, 0.6-1.2% Mg, 0.05%
Cr, 0.25% Zn, 0.1% Ti, 0.15% other elements, saldo to make 100% is Al. However
this alloy is only available in tubes 57/47. Moreover, we couldn't obtain this
alloy as it appears not to be a stock item.
Tube sizing:
60mm / 50mm tube: (2.331 kg/m)
midi note |
frequency (Hz) |
length (mm) |
suspension |
m constant |
weigth kg |
48 |
130.8 |
1627.5 |
365 |
1.1172 |
3.793 |
49 |
138.6 |
1581 |
354.5 |
1.1169 |
3.685 |
50 |
146.8 |
1536 |
344 |
1.1169 |
3.580 |
51 |
155.6 |
1491 |
334 |
1.115 |
3.476 |
52 |
164.8 |
1449 |
325 |
1.1157 |
3.378 |
53 |
174.6 |
1407 |
315.5 |
1.1145 |
3.280 |
55mm / 45mm tube: (2.200 kg/m)
midi note |
frequency (Hz) |
length (mm) |
suspension |
m constant |
weigth kg |
54 |
184 |
1298 |
291 |
1.1045 |
2.856 |
55 |
195 |
1261 |
283 |
1.1044 |
2.774 |
56 |
207.6 |
1225 |
274.5 |
1.1033 |
2.695 |
57 |
220 |
1190 |
267 |
1.104 |
2.618 |
58 |
233.1 |
1156 |
259 |
1.1037 |
2.543 |
59 |
246.9 |
1123 |
252 |
1.1036 |
2.471 |
50mm / 40mm tube: (1.908 kg/m)
midi note |
frequency (Hz) |
length (mm) |
suspension |
m constant |
weigth kg |
60 |
261.6 |
1040 |
233 |
1.1129 |
1.955 |
61 |
277 |
1010 |
226.5 |
1.112 |
1.906 |
62 |
293 |
980 |
220 |
1.1092 |
1.848 |
63 |
311 |
952 |
213.5 |
1.1089 |
1.801 |
64 |
329 |
925 |
207 |
1.1092 |
1.746 |
65 |
349 |
898 |
201 |
1.1075 |
1.698 |
40mm / 30mm tube: (1.484 kg/m)
midi note |
frequency (Hz) |
length (mm) |
suspension |
m constant |
weigth kg |
66 |
369 |
773 |
173 |
1.1135 |
1.136 |
67 |
391 |
751.5 |
168.5 |
1.115 |
1.108 |
68 |
415 |
730 |
163.7 |
1.1146 |
1.076 |
69 |
440 |
709 |
159 |
1.1139 |
1.048 |
70 |
466 |
689 |
154.5 |
1.1145 |
1.018 |
71 |
493 |
668.5 |
150 |
1.1116 |
0.988 |
35mm / 25mm tube: (1.272 kg/m)
midi note |
frequency (Hz) |
length (mm) |
suspension |
m constant |
weigth kg |
72 |
523 |
602.5 |
135 |
1.1121 |
0.765 |
73 |
554 |
585 |
131 |
1.1107 |
0.743 |
74 |
587 |
567 |
127 |
1.1055 |
0.721 |
75 |
622 |
551 |
123.5 |
1.106 |
0.701 |
76 |
659 |
535 |
120 |
1.1047 |
0.680 |
77 |
698 |
519 |
116 |
1.1015 |
0.660 |
30mm / 20mm tube: (1.060 kg/m)
midi note |
frequency (Hz) |
length (mm) |
suspension |
m constant |
weigth kg |
78 |
739.99 |
466.5 |
104.6 |
1.1247 |
0.494 |
79 |
783.99 |
453.6 |
101.7 |
1.1266 |
0.481 |
80 |
830.61 |
440 |
98.65 |
1.1231 |
0.466 |
81 |
880 |
426.5 |
95.6 |
1.118 |
0.441 |
82 |
932.33 |
414.5 |
92.93 |
1.1187 |
0.439 |
83 |
987.77 |
402 |
90.13 |
1.1149 |
0.426 |
84 |
1046.5 |
391.5 |
87.77 |
1.1203 |
0.415 |
85 |
1108.7 |
380 |
85.2 |
1.1182 |
0.403 |
86 |
1174.66 |
369 |
82.7 |
1.1171 |
0.391 |
87 |
1244.51 |
357 |
80 |
1.1078 |
0.378 |
88 |
1318.5 |
347.5 |
77.9 |
1.112 |
0.368 |
89 |
1396.9 |
336 |
75.3 |
1.1014 |
0.356 |
90 |
1479 |
326.5 |
73.2 |
|
0.346 |
91 |
1567 |
316.8 |
71.03 |
|
0.336 |
The tubes are suspended on their nodal point at both ends. Thus we could avoid
the swinging of the tubes and as a consequence, unreliable operation on repeated
notes. This is a problem we had on the <Tubi> robot.
This robot uses seven fast PIC microprocessors; five 8-bit controllers and
two 16-bit controllers, handling following tasks:
- Midi parsing, hub and light control (18F2620)
- Beaters for notes 48 to 65 (18F4620)
- Dampers for notes 48 to 65(18F4620)
- Beaters for notes 66 to 91 (18F4620)
- Dampers for notes 66 to 91 (18F4620)
- Vibrato motor control 48 to 65 (24EP128MC202)
- Vibrato motor control 66 to 91 (24EP128MC202)
Beaters:
The beaters for the tubes were selected such that the mass of the moving anchor
is in the order of one fifth of mass of the tube to be struck. This condition
made the use of pretty hefty solenoids for the low notes mandatory. Hence our
selection of Kuhnke solenoids, type HD8286-RF for the notes 48 to 65 and type
HD6286-RF for 66 to 71. For the higher notes, Tremba 24V solenoids were used.
The beaters have adjustable bakelite knobs (threaded) covered with a layer of
felt. These solenoids are specified to operate at 24V (100% duty cycle). As
we wanted to implement a wide range of dynamic, we operate them on a 100V voltage.
At that voltage, the pulse durations required to activate the coils range from
3.5ms to 30ms. Microcontrollers (PIC 18F4620) are used to generate these pulses
proportional to the required velocity. As this robot uses many and heavy solenoids,
it became a pretty expensive robot to construct.
It appeared of utmost importance to build the instrument such that the beaters
strike the tubes exactly at the point halfway their length, thus eliminating
as much as possible the sounding of the first (inharmonic) overtone, having
a nodal point at that place. The circuit controlling the operation of the beaters
is:
Two of these
boards are used for the beaters. The MOSFET's used here are IRL640 types and
the clamping diodes MUR620C.
Dampers:
The dampers make this robot very different than the earlier <Tubi> robot,
where we did not use any kind of damping. With the dampers -the damping can
be controlled by the users- the robot becomes a valid alternative for our <Vibi>
robot, an automated vibraphone.
To reduce costs a bit, we used cheap Chinese long-stroke magnets for the dampers
on the lowest 18 notes. At Banggood they go for ca. 17$ a piece. They are rated
for 12 V at a duty cycle of 5%. The DC resistance of the winding is 1.5 Ohm.
Applying the handy formula given in the Kuhnke catalog:
we
can derive that the nominal voltage for the coils is 5.8 V. However, if we leave
them activated for a long time (> 5 minutes) they become very hot and their
resistance goes up to 2.2 Ohm. Thus, to keep things safe, the continuous voltage
should be kept below 5 V. At that voltage, the coils still draw 3.33 A of current
and consume 16.6 W. With such figures in mind, it's easy to understand why we
limited the polyphony of this robot to four notes in the low register...
To protect the damper solenoids used for the note range 48 to 65, we applied
an old trick: wiring a 35 W - 12 V Halogen bulb in series with the coils, automatically
generates a high striking force, going down quickly as the bulb starts glowing,
thus increasing its resistance by a factor 10. The time the dampers are active
can be controlled by the user, as we mapped it on the release byte accompanying
the note-off commands. If note-off with release can not be used (most commercial
sequencer software seems to ommit its implementation), we provided a midi controller
(#25) to set the amount of damping.
These solenoids drive circular felt covered plates mounted at the underside
of the tubes. The felt here is 10 mm thick, a requirement for silent operation.
Fall back of the anchors is also dampened with thick felt.
For the notes 66 up to 77, we used Tremba solenoids. For the notes 78 to 81,
we used Lucas Ledex solenoids and for the notes 82 up to 91 Black Knight types,
all rated for 12V at 100% duty cycle. As a consequence, here we could go without
the halogen bulbs. Of course, response speed is slower here.
A sustain controller (#64) is implemented in the firmware to disable the damper
mechanism alltogether.
The circuit to control the dampers (two boards are used) is identical to the
one described above for the beaters. However components are different. The MOSFET's
here are IRLZ34NPBF and here we did not mount clamping diodes, but MOV's. (Epcos
B72210S0140K101)
Resonators:
In <Tubo> pipe resonators are coupled to all tubes up to note 91. This
highly reinforces the fundamental pitch of the tubes. Due to the high mass of
the tubes, the sustain of the tones is very long. In order to limit building
height of the instrument, we used closed pipe resonators for the lowest nine
notes and open pipes for the higher notes. All resonators were made from PVC
tube material, except for the highest octave, where we used brass and copper.
In orchestrations for the logos robotorchestra of orchestral music, <Tubo>
makes a better alternative for the celesta. It can also be used as a replacement
for vibraphone parts.
Vibrato:
The resonators were mounted on an assembly that can move over a limited trajectory.
By automating this movement using two DC-motors with an excentric shaft, we
succeeded in building a quite novel vibrato mechanism. Modulating the distance
between the open ends of the resonators and the aluminum pipes leads to a vibrato
quite simular to that implemented on the vibraphone. The speed of the vibrato
can be controlled. Due to the high mass of the resonator assemblies, we had
to limit the maximum vibrato speed to slightly over 2.5 Hz. Extreme slow vibrato
is perfectly possible. When the vibrato mechanism is switched off, the motors
will slow down and return the resonators to their optimum coupled position automatically.
One motor steers the vibrato for the notes 48 to 65 and another one the notes
66 to 91. Hence we implemented two separate controllers (#20 and #21) for the
vibrato speed. Controller #22 is implemented as well, and will set the vibrato
speed for both motors together.
The circuit used to drive the vibrato mechanism is:
Here
a 16-bit PIC microcontroller is used.
MIDI-hub board:
All circuits shown above get their 5V power from a MIDI-hub board, controlling
the lights and taking care of MIDI parsing. This board also houses a high current
relay used to switch the high power supplies on. Here is the circuit: 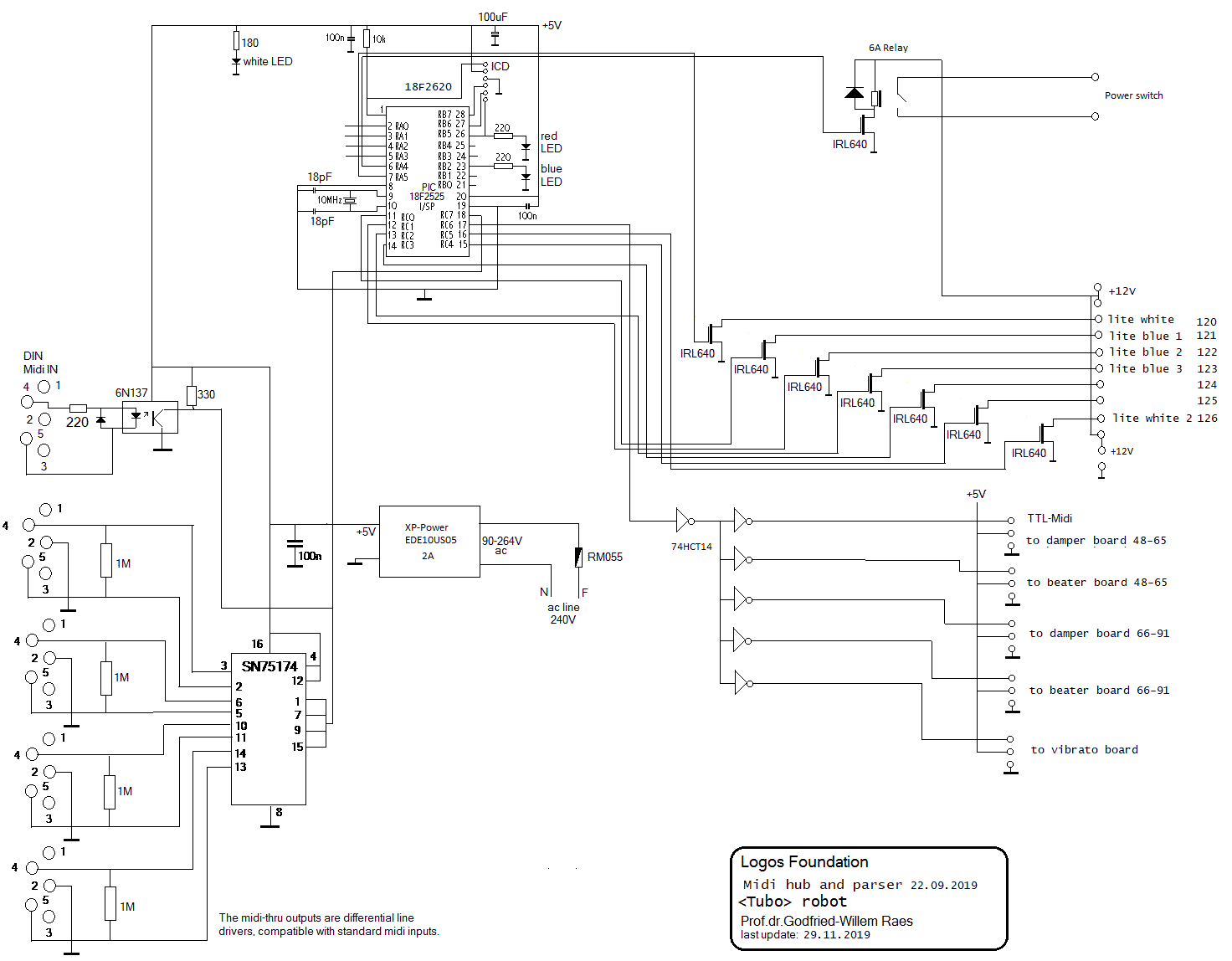
Power Supply:
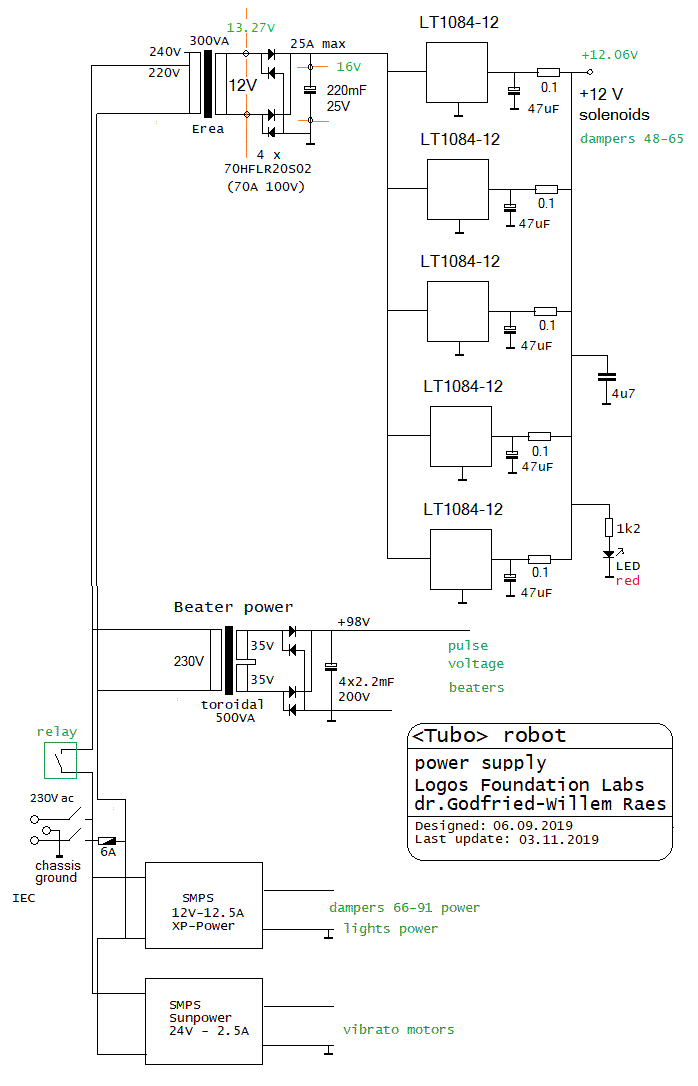
This robot was finished and completely ready for playing in february 2020.
In 2021 we added a radar board such that the <Tubo> robot can now be
setup as an autonomous interactive sound sculpture. Details on the
radar board can be found here.
Here is the circuit: 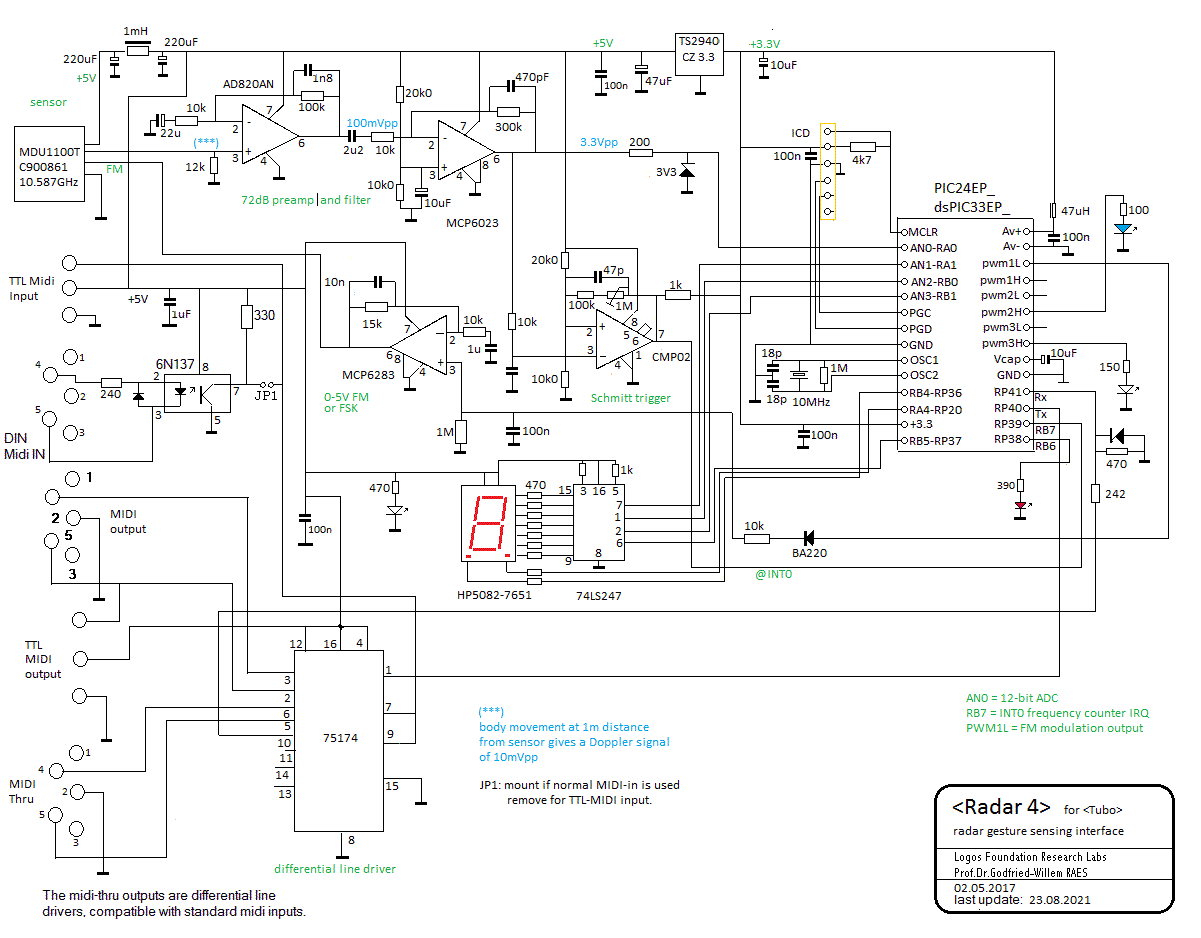
Mapping:
Midi note range: 48-91
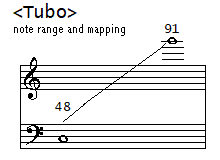
Note Off commands with release are required to activate the dampers. If noteoff
with release cannot be used (many sequencers do not implement it), the release
values used can be set with controller 25. This value will also be used when
noteon commands with velo=0 are used to switch notes off. It is permissible
to only send note-on commands, if dampers are not used. It is also permissible
to only send noteoff+release commands, causing the tubes to be played with the
dampers only. This gives a rather soft tone and sounds the pitch of the air
column in the tubes together with their fundamental note.
Note On commands: Velocity is implemented and has a wide controll range. Value
32 corresponds to a musical 'p' (76dBA), a 'f' (90dBA) is reached with value
64 and a 'ff' (102dBA) with value 96. Note that repetition rate is a function
of velocity! The lower the velocity values used, the faster the repetition rates
can be. Repetition rates also depend on pitch, as they are a function of the
anchor mass. So low notes have inherently slower repetition rates than high
notes.
Lights are mapped on midi-notes as follows:
- note 120: White LED strip under the low side beater assembly
- note 121: Blue LED spot upwards from bottom power supply
- note 122: Blue LED spot downwards from bottom power supply
- note 123: Blue LED strip under the high side damper assembly
- note 124: Blue LED multi-LED spotlight, inside on high damper assembly
- note 125: Blue LED multi-LED spotlight, outside on high damper assembly.
- note 126: White LED strip under the high side beater assembly
The velocity byte, in this case, steers the flashing speed. With velocity =
127, the lights are full on, without flashing.
The key pressure command controls the repetition rate for the lights, if switched
on. This feature is not implemented for the beaters.
Controllers:
- Controller 20: Steers the vibrato speed for the note range 48 to 65
- Controller 21: Steers the vibrato speed for the note range 66 to 91
- Controller 22: Steers the vibrato speed for both motors together. However,
sync is not guaranteed.
- Controller 25: Steers the damping time for all notes 48 to 91. Default value
= 64
- Controller 64: sustain on/off switch. When 0 (off), the damper mechanism
will be active. When >0 (on), the damper mechanism is disabled. The default
value is OFF.
- Controller 66: is used to switch the solenoid power on or off. It will also
release all dampers and reset controllers to default values. On cold boot,
this controller is OFF.
- Controller 123: all notes off command. Damps all sounding notes (unless
sustain is on) and switches off lights. It stops both vibrato motors. It does
not reset any controllers.
The midi listen channel is 4 (counting 0-15)..
Techical specifications:
- size: h = 1600 mm, w = 1272 mm, d = 620 mm
- weigth: 228 kg
- power: 240V ac
- tuning: equal temperament based on A=440 Hz
- Ambitus: 3 1/2 octaves 48-91
- Maximum sound pressure level: >106dbA
- control: MIDI input , channel 4
- Insurance value: (construction cost) 56.000 Euro
Design and construction: dr.Godfried-Willem
Raes
Collaborators on the construction of this robot:
- Bert Vandekerkhove (mounting)
- Kristof Lauwers (coding)
- Lara Van Wynsberghe (tuning)
- Mattias Parent (workshop)
- Moniek Darge
- Peter Van Lancker
- Laura Maes
Music composed for <Tubo>:
- Godfried-Willem Raes 'Eindjes' (2019)
- Godfried-Willem Raes 'Rad4Tub' (2021, interactive and embedded composition
for Radar4)
Nederlands:
<Tubo>
Bouwdagboek:
Omdat ons vaak wordt gevraagd hoeveel werk en tijd kruipt in,
en nodig is voor, het bouwen van een muzikale robot, hebben we ook voor <Tubo>
een uitgebreid en gedetailleerd bouw- en onderhoudsdagboek bijgehouden: Dit
bouwdagboek is uitgebreider dan dat voor vele vroegere robots omdat we -wetend
dat ons einde stilaan naderbij komt- jongeren die in ons voetspoor zouden willen
treden zoveel mogelijk tegemoet wilden komen.
- 01.06.2019: eerste ideen en konkrete tekeningen aansluitend bij de bouw
van het Plus-Minus projekt.. Onderzoek naar de toepassingsmogelijkheden van
bidirektionele sleeplade magneten voor de kloppers. Zo stond het beschreven
in de eerste beschrijving van het <Tubo> bouwprojekt: "The tubes
have individual felt covered rubber beaters driven by solenoids as well as
individual dampers. Musical dynamics are implemented by applying pulse width
modulation techniques in the driver circuits both for the beaters and for
the dampers. For the lowest octave the weight of the beaters has to be ca.
1/5th of the weight of the tube to be struck. The beaters have to be covered
with a layer of felt. This condition necessitated the use of strong bidirectional
solenoids for the beaters. In organ windchests these solenoids are always
wired as:
If
the left winding gets current, the anchor moves to the left, with the right
coil powered, the anchor moves to the right side. If both coils are activated,
the magnetic fields cancel each other and no force is available from the anchor.
If we use this type of solenoid in the following configuration, however:
operation is quite different. When only one coil is activated, it will behave
as before, but when both coils are activated, the anchor will move to he center
and force will be available to keep it there, as both magnetic fields will
reinforce each other. By controlling the current over both coils independently,
we can make the coil operate as a linear motor."
- 02.06.2019: Ontwikkeling veralgemeende software voor de berekening van de
stemming en dimensionering van de aluminium buizen. Hiervoor gebruiken we
de Power Basic Console Compiler.
- 03.06.2019: Aanmaak set proefbuizen ter bepaling van de materiaalkonstanten.
- 04.06.2019: Buizen voor de noten 60 tot 65 uit 50/40 buis precies gezaagd
en gestemd.
- 05.06.2019: Noten 66 tot 71 uit 40/30 buis gestemd.
- .
Hier zijn de
maten van de af te zagen lengtes:
midi noot |
frekwentie (Hz) |
lengte (mm) |
ophangpunt |
gewicht kg |
60 |
261 |
1040 |
233 |
1.955 |
61 |
277 |
1010 |
226.5 |
1.906 |
62 |
293 |
980 |
220 |
1.848 |
63 |
311 |
952 |
213.5 |
1.801 |
64 |
329 |
925 |
207 |
1.746 |
65 |
349 |
898 |
201 |
1.698 |
Om een goede grondtoon te verkrijgen moet het gewicht van de (zachte) hamers
minstens een vijfde zijn van het gewicht van de buis.
- 06.06.2019: Zes testbuizen, maat 40/30 nauwkeurig gestemd. Midi noten 66
tot 71. Hier zijn de maten van de af te zagen lengtes:
midi noot |
frekwentie (Hz) |
lengte (mm) |
ophangpunt |
gewicht kg |
66 |
369 |
773 |
173 |
1.136 |
67 |
391 |
751.5 |
168.5 |
|
68 |
415 |
730 |
163.7 |
|
69 |
440 |
709 |
159 |
|
70 |
466 |
689 |
154.5 |
|
71 |
493 |
668.5 |
150 |
|
- 07.06.2019: Berekeningssoftware aangepast en geperfectioneerd. Zes testbuizen,
maat 35/25 gestemd. Midi noten 72 tot 77. Deze buizen kunnen ook in de bestaande
struktuur van Plus Minus opgehangen worden.
midi noot |
frekwentie (Hz) |
lengte (mm) |
ophangpunt |
gewicht kg |
72 |
523 |
602.5 |
135 |
|
73 |
554 |
585 |
131 |
|
74 |
587 |
567 |
127 |
|
75 |
622 |
551 |
123.5 |
|
76 |
659 |
535 |
120 |
|
77 |
698 |
519 |
116 |
|
- 08.06.2019: Meting van het minimaal noodzakelijk gewicht van de hamers.
Blijkt dat dit minimaal 1/10, maximaal 1/5 van de massa van de aan te slane
buizen moet zijn voor een optimaal grondtonige klank. De 'wet van de klok'
blijkt ook hier van kracht. De hamers moeten ook voorzien worden van een dikke
laag leder of vilt.
- 09.06.2019: Ontwerp en berekening van een terugslagmechanisme voor de hamers
in het laagste oktaaf, gebruik makend van bidirektionele registertrekmagneten
zoals gebruikt in de orgelbouw.
- 10.06.2019: Eerste tentatieve maatvoering uitgewerkt (voor ambitus 60 -
96):
eerste rij buizen |
tweede rij buizen |
6 x 50 = 300 |
2 x 35 = 70 |
6 x 40 = 240 |
19 x 30 = 570 |
4 x 35 = 120 |
22 x 10 = 220 |
17 x 10 = 170 |
|
breedte = 850 |
breedte = 860 |
Op deze wijze opgebouwd
kan de breedte van de robot wellicht beperkt blijven tot 1 meter.
- 11.06.2019: Proefopstelling gemaakt met haakjes. We hebben hier wel wat
problemen met zinderingen op de ophangstaafjes.
Viltjes helpen wel wat, maar lossen het probleem niet helemaal op.
- 12.06.2019: Experimenten met buisresonatoren teneinde de grondtonigheid
te versterken. De klank gaat dan wel meer naar een vibrafoon klinken. Open
buis resonatoren geven iets meer resonantie (volume) dan gesloten buizen,
zoals blijkt uit onze experimenten met de buis voor midi noot 60. Buisresonatoren
zijn heel zeker een muzikale verbetering. In principe zouden we ook draaiende
kleppen kunnen voorzien, zoals op een vibrafoon. Softshift magneten op elke
resonator buis zouden de ideale oplossing zijn, maar daarvoor hebben we de
middelen niet meer... ( Met dank aan Sven Gatz die de samenstelling van de
ministeriele advieskommissies niet van korruptie dierf te saneren).
- 13.06.2019: Overweging tot uitbreiding van het instrument naar de laagte
toe. Ambitus 48 - 96 of, 48-84. Zodoende kan het instrument ook als celesta
dienst doen. Ontwerp T-vormige resonatoren in PVC. Elektromagneten voor de
hamers besteld bij Laukhuff.
Enkele
bugs gedood in de berekeningssoftware. De nieuwe tessituur zou dan kunnen
worden: 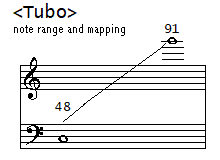
- 14.06.2019: Nieuwe en betere test- en meetopstelling gemaakt. De resonatorbuizen
moeten zeker dezelfde diameter hebben dan de klankbuizen. De testopstelling
voor midi noot 60 werkt prima nu. Software aangepast voor de berekening van
de resonators. Resonatoren hebben vanaf noot 87 weinig zin meer. De lengte
van de resonator wordt kleiner dan vijfmaal de doorsnede ervan wat een geringe
resonantie voor gevolg heeft. Foto van de betere testmontage:
En ook vier resonatoren voor de noten 60, 61,62, en 63 gemaakt, gestemd en
getest:
De diameter van de resonatoren moet overeenstemmen met die van de aluminium
klankbuis.
- 15.06.2019: Vijf duwmagneten besteld bij Conrad.
- 16.06.2019: Eerste schets van de mogelijke opbouw...
Gestemde buizen afgewerkt tot en met noot 84. Alle nodale gaten voor noten
60 tot 84 geboord en afgewerkt. Voor de uitbreiding naar de laagte is het
wachten op informatie over de leverbaarheid van de aluminium buizen. Zo stilaan
hebben we een zicht op de werklast voor de konstruktie van deze robot. Hij
zal pas in 2020 beschikbaar kunnen komen...
- 17.06.2019: Buizen voor noten 85 en 86 gezaagd en gestemd. Experimentele
opstelling met buismontage in de slagrichting. Dit zou de konstruktie aanzienlijk
vereenvoudigen. Er zijn wel 10 mm dikke viltringen nodig voor de montage.
Akoestisch gezien
is en blijft dit evenwel een minderwaardige oplossing. Wel kunnen we nog overwegen
om de ophanggaten (nu 3mm) te vergroten, zodat we de schroefdraad kunnen overtrekken
met kunststof of rubber. Na te meten valt in welke mate dit een invloed heeft
op de stemming. Vijf Tremba solenoids type ZMF-3865d-15.002 24V DC geleverd
door Conrad. Deze zouden geschikt moeten zijn voor de dempers. Resonatoren
prototypes gemaakt voor noot 66 (40 mm PVC buis) en noot 72 (32 mm PVC buis).
Overwogen kan ook worden om het mechanisme van een doppler-reflektie tremulant
zoals we die aantreffen in harmoniums, te gebruiken voor de noten vanaf 78.
Zo'n geautomatiseerde tremulant bouwden we al eens voor onze <Harmo>
robot.
- 18.06.2019: Resonatoren voor de noten 72 tot 77 gemaakt en gestemd. Materiaal:
grijs PVC , 32 mm diameter.
Bestelling geplaatst bij Demar-Lux voor aluminium buizen tot diameter 60 mm.
Buisdiameter 57 blijkt niet leverbaar, maar 55 mm klaarblijkelijk wel. Noten
54 tot 59 moeten dus opnieuw berekend worden.
- 19.06.2019: Proefopstelling gemaakt met een buis waarvan we de ophanggaten
uitboorden tot 6 mm, zodat we er met zacht PVC beklede M3 draadstang kunnen
doorsteken. Het vergroten van de ophanggaten heeft geen door ons meetbare
invloed op de stemming. We hebben de indruk dat de toonhoogte minder dan een
cent daalt. Deze wijze van ophanging geeft evenwel, bij gelijke aanslagsterkte,
slechts ongeveer de helft van de geluidsterkte op.
- 20.06.2019: Aluminium buis 55/5 blijkt nu toch niet leverbaar te zijn...
Dan maar 60/5 voor het laagste oktaaf?
- 22.06.2019: Verdere proeven en berekeningen voor de konstruktie van de ophanging
van de buizen.
- 24.06.2019: De bij Laukhuff bestelde bidirektionele sleeplademagneten kunnen
bij dit bedrijf alleen nog besteld worden met een aangebouwde microprocessor
bestuurde regeling. Dit is voor onze toepassing evenwel volkomen onbruikbaar.
Bovendien staan die magneten met die schakeling nu ca. 250 euro per stuk geprijsd,wat
de kost met 6250 euro zou verhogen... Op zoek naar alternatieven. In de Kendrion
Kuhnke katalogus staan enkele types die in aanmerking kunnen komen: HD82-86R
F24. Het bidirektionele type UV40F heeft evenwel een trajekt van maximaal
8 mm, wat zeker met de M5 schroefdraad op het anker, aan de kleine kant is
voor onze toepassing. Het type V45 heeft een trajekt van 15 mm en is voorzien
van M6 schroefdraad op het anker. Hier is een link
naar de katalogus.
- 03.07.2019: Twaalf Kuhnke magneten (HD8286RF24) besteld bij Distrelek. Te
testen voor het onderste oktaaf. Hier is een foto van zo'n elektromagneet:
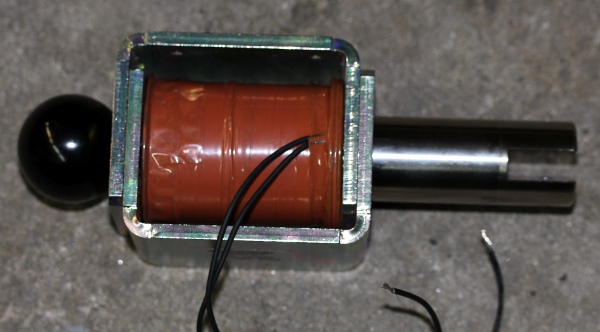
- 04.07.2019: Banggood: magneten besteld in China (12V, 1.5 Ohm). Elf Kuhnke
magneten werden geleverd, een magneet is in nabestelling.
- 05.07.2019: Levering Demar-Lux: Alu-buis diameters 55 en 60 mm. Buizen voor
de noten 54 tot 59 berekend, gezaagd en gestemd.
55mm / 45mm tube: (2.200 kg/m)
midi note |
frequency (Hz) |
length (mm) |
suspension |
m constant |
weigth kg |
54 |
184 |
1298 |
291 |
1.1045 |
|
55 |
195 |
1261 |
283 |
1.1044 |
|
56 |
207.6 |
1225 |
274.5 |
1.1033 |
|
57 |
220 |
1190 |
267 |
1.104 |
|
58 |
233.1 |
1156 |
259 |
1.1037 |
|
59 |
246.9 |
1123 |
252 |
1.1036 |
|
- 06.07.2019: Berekenen, zagen en stemmen van de 60 mm aluminium buizen voor
de noten 48 tot 53.
60mm / 50mm tube: (2.331 kg/m)
midi note |
frequency (Hz) |
length (mm) |
suspension |
m constant |
weigth kg |
48 |
130.8 |
1627.5 |
365 |
1.1172 |
|
49 |
138.6 |
1581 |
354.5 |
1.1169 |
|
50 |
146.8 |
1536 |
344 |
1.1169 |
|
51 |
155.6 |
1491 |
334 |
1.115 |
|
52 |
164.8 |
1449 |
325 |
1.1157 |
|
53 |
174.6 |
1407 |
315.5 |
1.1145 |
|
Absolute measurement error on lengths: +/- 0.5 mm.
Voor de laagste 12 noten (48 to 59) gebruiken we beter 1/4 lambda resonatoren
omdat anders het instrument hoger zou worden dan twee meter, wat niet alleem
problemen geeft bij transporten, maar ook de konstruktie van het vibrato mechanisme
ernstig bemoeilijkt. De organisatie van de buizen in de robot zou ideaal zijn
met 18 klankbuizen vooraan (breedte 1200 mm, wanneer we 10 mm tussenruimte
kunnen aanhouden) en 27 klankbuizen achteraan (wat met dezelfde tussenruimte
ook 1200 mm oplevert). De tessituur kan dan lopen van 48 tot en met 94. Dit
zou een goede dimensionering kunnen zijn voor de voorste rij:
Hier
zijn we met de 12 gestemde buizen voor het laagste oktaaf: 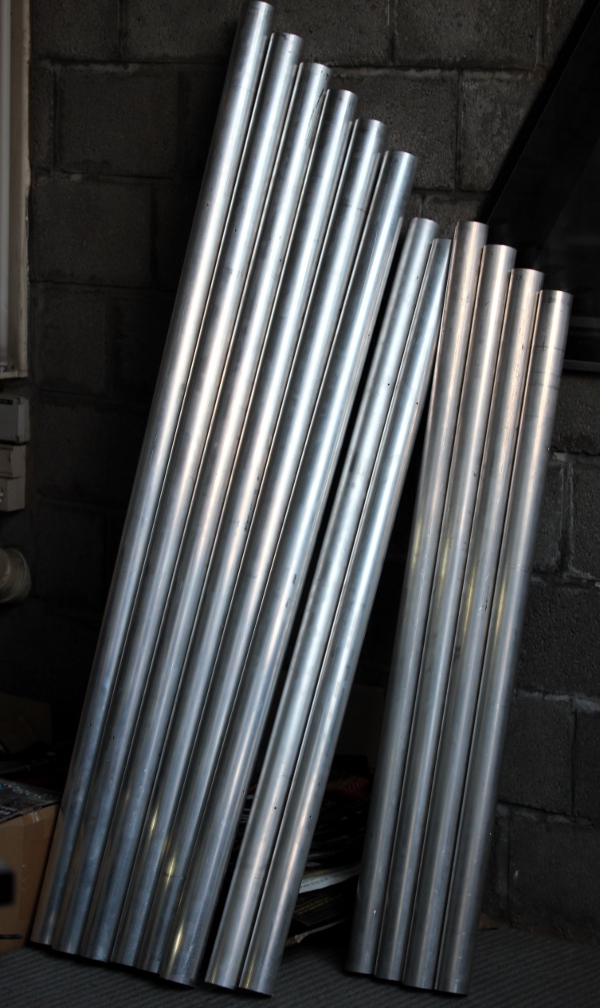
- 07.07.2019: Redaktie van een software programma voor de berekening van de
maatvoering voor de bouw van <Tubo>. Dit is het resultaat voor de eerste
module:
De breedte
van deze module komt dan uit op 430 mm. Ook de precieze maatvoering voor de
vertikale plaatjes, kunnen we heel exakt bepalen nu:
De vertikale plaatjes moeten in tweevoud gemaakt worden (het tweede exemplaar,
gespiegeld), want we hangen de buizen op twee nodale punten op. Alle maten
zijn opgegeven in mm.
- 08.07.2019: Gespiegelde ophangplaatjes toegevoegd aan de werktekening. Belangrijk:
eerst alle gaatjes in de plaatjes boren alvorens ze vast te lassen op de achterplaat.
Eens gelast is boren en uitboren immers onmogelijk geworden vanwege de kleine
tussenruimte.
- 09.07.2019: Uitzagen en boren van de ophangbeugels uit 3 mm dik plat inox,
30 mm breed. Werktekening aangepast:
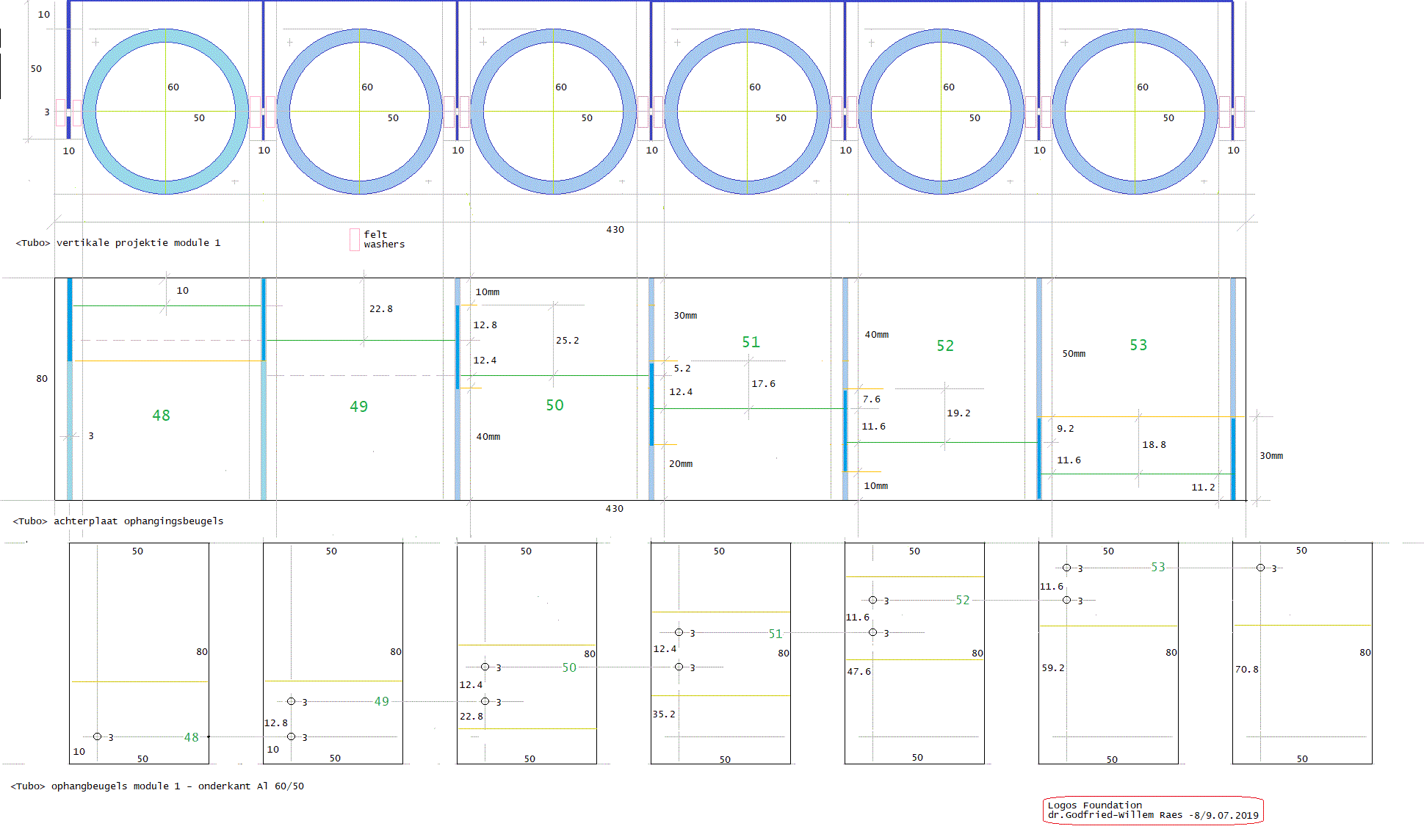
- 10.07.2019: Testresonator gemaakt in T vorm. Dit zou een groter geluidsvolume
moeten opleveren, maar het bemoeilijkt wel de konstruktie van het vibrato
mechanisme. Uitsnijden twee achterplaten voor de beugels (430 x 80 x 2). TIG-laswerk
bovenste en onderste houder voor noten 48 tot 53.
Volledig
rondlassen van de uitstekende ophangstukken blijkt onmogelijk vanwege de ruimte
die we voor de TIG toorts en haar beweging zelf nodig hebben. Hier is een
foto van de beide afgelaste beugels:
Het ziet ernaar uit dat we met veel moeite de hoogte van dit instrument kunnen
beperken tot twee meter.
- 11.07.2019: Werkplan voor de tweede module:
Ophangplaatjes,
inox plat 30 mm x 3 mm x 45 mm gezaagd en geboord. Alle plaatjes gelast. Hele
dag werk...
- 12.07.2019: Werktekening voor module 3:
Voor de ophangplaatjes kunnen we inox plat 30 x 3 aanhouden. We kunnen hier
alle plaatjes afzagen op 40 mm. Uitzagen en boren van de gaatjes.
- 13.07.2019: TIG-laswerk voor de ophangbeugels van module 3, noten 60 tot
65. Mogelijke samenvoeging van de eerste drie modules:
Om de vertikale verbindingen te maken, zou dit een mogelijkheid zijn, gebruik
makend van inox plat 10 x 20:
De
aanslagsolenoids zijn in de lengte niet helemaal op schaal getekend. De opgegeven
lengte maat, 180 mm, is de volledige ruimte die de solenoiden in beslag nemen.
De horizontale drager waarop ze gemonteerd moeten worden, moet losneembaar
zijn. (Vier lange M10 bouten gebruiken). Anders is het onmogelijk de klankstaven
in de struktuur op te hangen. Een maatschets voor de frontale kant zou er
zo kunnen uitzien:
Aan de rechterkant komt plaats vrij voor de inbouw van de elektronika en de
aansluitingen voor voeding en data.
- 14.07.2019: Ontwerp van een geschikte wielbasis, met zo mogelijk beperking
van de diepte van de robot tot 450 mm. Berekening van de lengtes van de vertikale
opstanden, wanneer we die zouden vervaardigen uit 100 x 50 x 3 inox kokerprofiel.
Hier is een eerste tentatief ontwerp:
De wielen aan de rechterkant zijn zwenkwielen, bouwhoogte 125 mm, wieldiameter
100 mm. Grotere wieldiameters zijn ook mogelijk, aangezien de wielen de dempers
niet in de weg zitten. De maximale diameter, zonder de totale bouwhoogte te
vergroten zou 250 mm zijn. Die wielen hebben we echter niet op voorraad.
- 15.07.2019: Plan opnieuw getekend indien we 200 mm wielen zouden gebruiken.
Wicke wielen 200x50, bouwhoogte 235, as 20mm, naaf 60mm. Deze wielen kosten
echter wel ca. 400 euro.
Vier
zwenkwielen met rem zouden natuurljk de handigste oplossing zijn. Om de kostprijs
te beperken kunnen we natuurlijk ook standaardzwenkwielen met zwarte rubberbanden
voorzien, ze kosten minder dan half zoveel als de mooiere Wicke wielen. Deze
standaard-wielen hebben een bouwhoogte van 243 mm. Het bouwplan zou er dan
komen uit te zien alsvolgt:
Voor
de lage kant, kunnen bij deze bouwhoogte echter geen zwenkwielen worden gebruikt:
ze komen in botsing met de onderste drie demper-magneten! Voor de noten 66
tot 71 kunnen we Kuhnke magneten, type HD6286-RF gebruiken. Die kosten 96
Euro per stuk bij Distrelec. De klankbuizen hebben hier een diameter van 40
mm.
- 16.07.2019: Inkoop bokwielen, 200 mm diameter. Zes extra Kuhnke magneten
besteld bij Distrelec.
- 17.07.2019: Bokwiel sektie ontwerp gewijzigd (plan 13):
Gedetailleerd bouwplan voor de bokwielkonstruktie op een doorlopende as van
20 mm uitgetekend( plan 14):
De
stelringen worden vastgezet met M6 stelbouten (inbus hex). Op die wijze zijn
de wielen eenvoudig af te nemen en indien nodig te vervangen. Uitzagen van
de 10 mm dikke wielhouders: 200 x 50 x 10 en precies boren van de 20 mm asgaten.
Bij nader toezicht, blijken de buitenste stelringen eigenlijk overbodig te
zijn.
- 31.07.2019: Inkoop 60 mm PVC buis (regenafvoer) bij Deschacht. Ook 12 bochten
aangekocht. Stoppen voor deze buizen blijken niet te bestaan. In de katalogus
van Eriks zijn ze wel opgenomen, maar dan voor buisdiameter 63 mm.
- 17.08.2019: Atelier werk aan Tubo opnieuw gestart. Uitzagen en aftekenen
op werkstuk van de linker vertikale opstand. Materiaal: inox kokerprofiel
100 x 50 x 5. Hoogte 1524 mm. Positionering van de beaters:
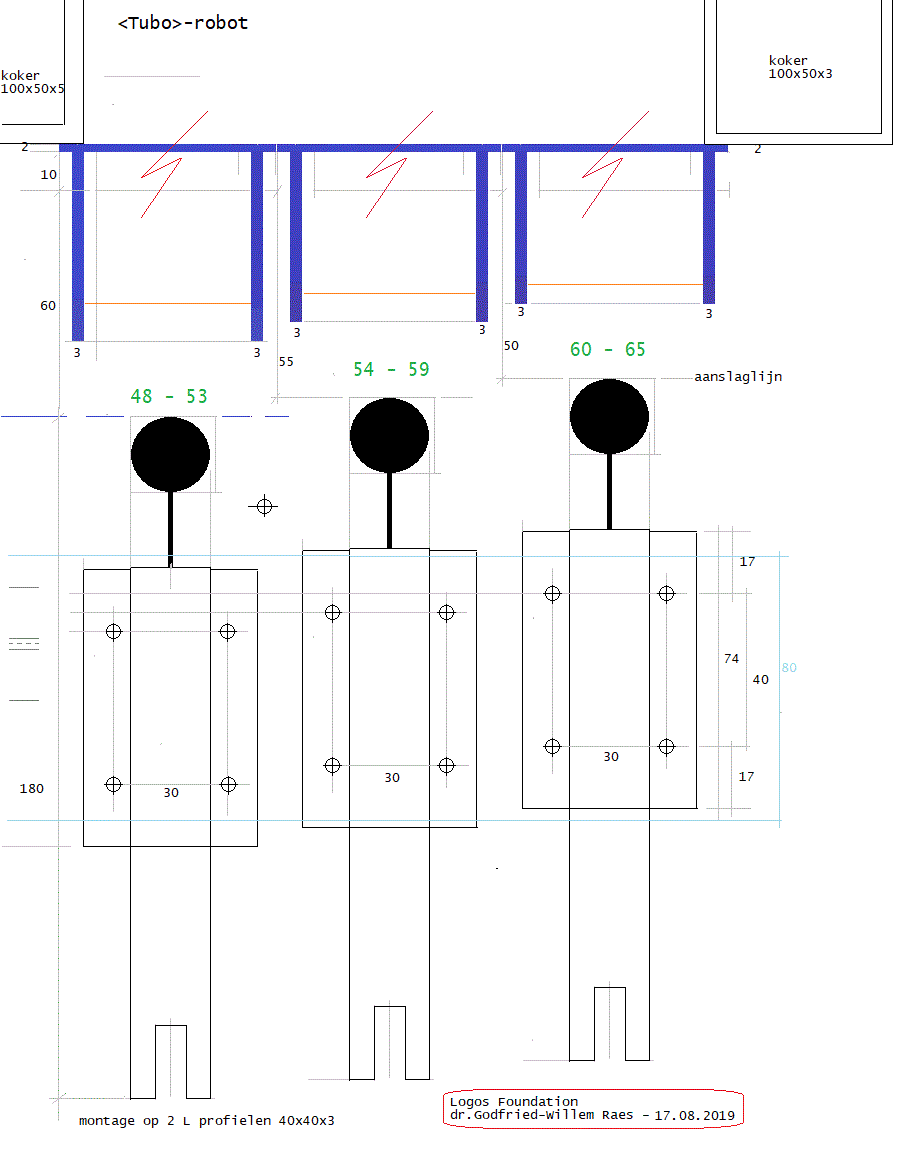
- 18.08.2019: Uittekenen gedetailleerd bouwplan en te lassen onderdelen. Hier
is de konstruktietekening voor de kloppers met de Kuhnke elektromagneten:
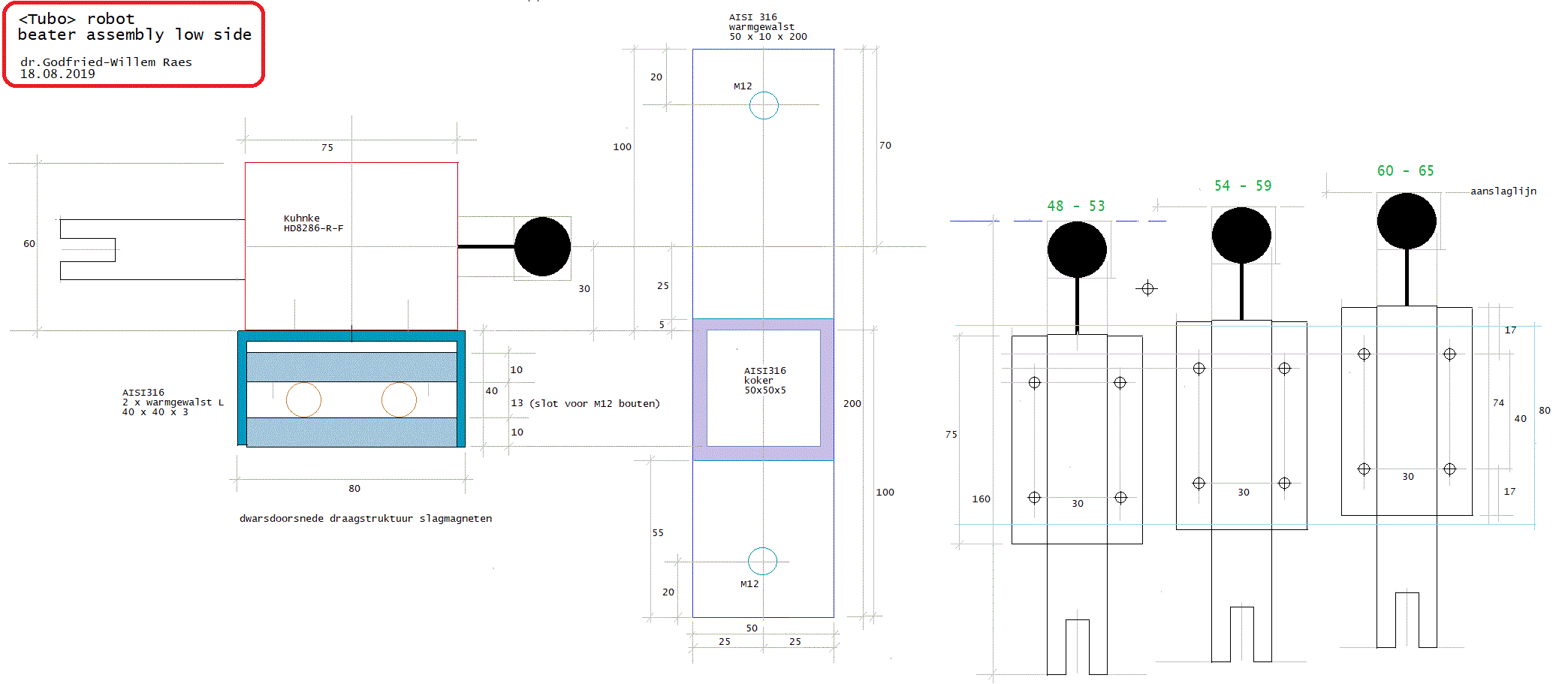
- Alle onderdelen worden vervaardigd uit roestvast staal.
- 19.08.2019: Berekening en uitzagen van de rechterkolom: 100x50x3x1348. De
bouwhoogte van de zwenkwielen met rem is 242 mm. Montageplaten voor de zwenkwielen
uitgezaagd in 10 mm dik inox plaat, geboord en gelast op 600 mm kokerprofiel
50 x 50 x 5. Tegenlas uitgevoerd in TIG, om de krimp en de doorbuiging tegen
te gaan. De wielen worden bevestigd met M10 inox bouten. Om een indruk te
krijgen van de omvang en de verhoudingen van de robot in opbouw, legden we
de al gezaagde vrije onderdelen eens losjes uit:
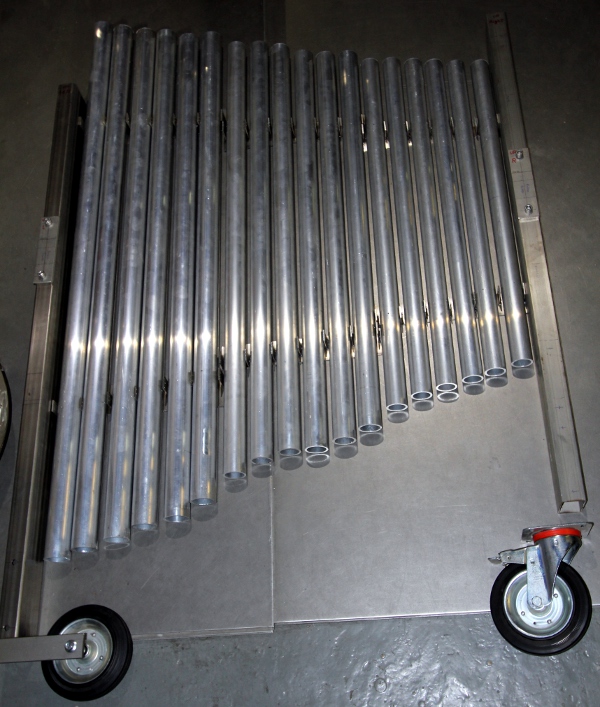
- 20.08.2019: Uitsnijden en lassen van de linkerwieldrager. Kokerprofiel 50x50x5x552.
De as is massief inox, 20 mm diameter. Asgaten gehoond. Gaten geboord in de
vertikale opstanden: montage van de resonatoren en van de achterrij buizen
moet zo mogelijk worden. Deze delen moeten demonteerbaar zijn. Hadden we maar
een lastafel van 2 meter... In te kopen: inox cilinderbouten M10 x 20 voor
de montage van de zwenkwielen. Hier zijn de wielmontages, in opbouw:
En nu, het precies
uitmeten en aanlassen van de dragers voor de klankbuizen aan de voorkant van
de robot: 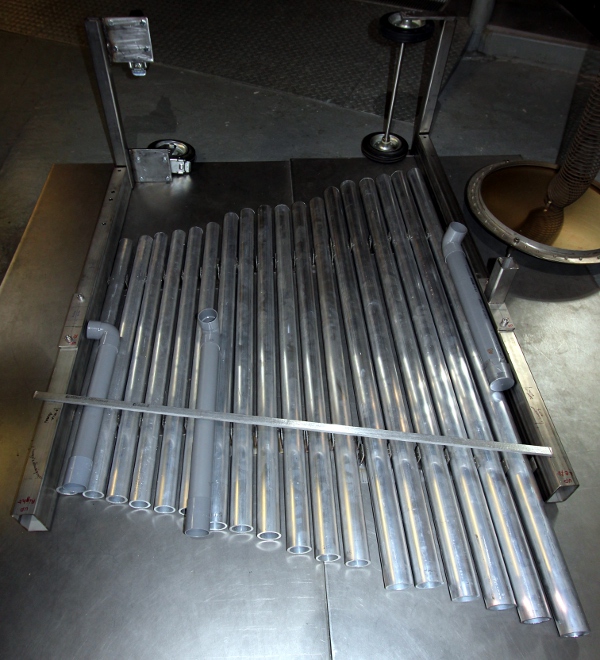
- 21.08.2019: Lassen op de lastafel van de beide buisdragers op 20 x 10 warmgewalst
inox staafmateriaal. Passen van de klankbuizen op de dragers: met de buis
voor noot 55 is er een probleem, de geboorde gaten kloppen niet... Rekenfout
of meetfout. De gaatjes voor noot 65 moeten een beetje bijgevijld worden.
Lassen van de rechter
vertikale kolom op de zwenkwielhouder.
- 22.08.2019: Rechten van de kromgetrokken buishouders: tegenlas en plooipomp.
Elektrodelassen van de linkervertikale kolom op de wielbasis. Terugplaatsen
van de takels in het atelier, het werkstuk is inmiddels immers veel te zwaar
geworden om nog volledig manueel gemanipuleerd te worden...
- 23.08.2019: Pijpdrager aangelast aan de vertikale opnstanden. Dwarsversterking
zal nodig zijn. Hier en daar moeten boorgaatjes in de klankbuizen toch wat
worden bijgevijld. Meetfouten en kromtrekken van laswerk spelen ons duidelijk
parten.
- 24.08.2019: Dwarsversterkingsprofiel afgetekend: 100 x 50 x 3 x 1271. Kan
dienstig zijn voor de montage van de elektronika. Begin berekening van de
achterzijde...een tessituur tot en met midi noot 91 moet haalbaar zijn.
- 26.08.2019: Te warm in het atelier voor laswerk... tekenen dan maar.
- 27.08.2019: Ontwerpen en uittekenen van de dempermechanieken. De chinese
elektromagneten zijn voorzien van een (slordig gemaakte...) M5 schroefdraad.
Uitzagen van de demperplaatjes. Testmontage met vilten dempers. De elektromagneten
moeten met M4 trillingsdempers gemonteerd worden. Fivistop 60IRHD M4x10 MF
besteld bij Farnell: bouwhoogte 8 mm, diameter 10 mm. Plaatjes, diameter 60
mm uitgezaagd uit aluminiumplaat:
Hoe we de nodige viltringen netjes kunnen maken is nog niet geheel duidelijk.
Met een schaar ziet het er echt niet uit. Een holpijp voor de nodige maten
kost meer dan 150 euro... Morgen, een experiment met een laser-snijmachine...
Plaatjes diameter 55 mm (aluminium) en 50 mm (inox) uitgezaagd.
- 28.08.2019: Zuiver centeren van de plaatjes op de draaibank. Afslijpen van
de zaagbramen. Het experiment met een laser-cutter werkt bevredigend met vilt,
maar het snijden laat wel een bruine rand na op het vilt. Uitzagen van de
houder voor de dempermagneten uit geplooid inox (dikte 2 mm). Voor het boren
van de gaten voor de magneten moeten we eerst een precieze boormal maken.
Het uitlijnen ervan belooft bijzonder moeilijk te worden, Hier is een afgewerkt
exemplaar van een demper-eenheid:
Alleen de trajektbegrenzingsviltring, tevens terugslagdemper, ontbreekt nog.
- 29.08.2019: Alle dempermagneten voorzien van trillingdempers. Test-presentatie
van de gemonteerde dempers op het chassis. Vastmaken chassis op de draagstruktuur.
Trajektbegrenzingsviltschijven besteld. Deze worden in de handel gebracht
voor de montage van hihat cymbalen. De dikte is 15 mm, diameter 40 mm.
- 30.08.2019: Om de magneten goed te kunnen afstellen, hebben we eigenlijk
een metaalfrees nodig die ons zou toelaten sleuven te maken in de inox draagplaten...
Viltschijven voor de dempers gelaserd en afgeleverd. Vastkleven van deze viltschijven
op de ronde metalen plaatjes. Hiervoor gebruikten we transparante siliconenrubber.
Uithardingstijd: 24u. De demperspoelen trekken bij 12V een stroom van 8 ampere.
De duty cycle moet volgens opgave van de fabrikant beperkt blijven tot 5%.
De voeding moet dit in pulsbedrijf kunnen leveren voor minstens 4 spoelen
tegelijkertijd. De piekstroom wordt dan 32 A... Wanneer we het gewicht van
de transformator binnen de perken willen houden, zijn we aangewezen op het
toepassen van heel erg grote elko's. Dat recept pasten we eerder al toe in
onze <Puff> robot.
- 31.08.2019: Testmontage van vier demperspoelen of het hoofdchassis. Het
precies boren van de gaatjes belooft een werk van lange adem te worden. De
eerste zes magneten worden met telkens vier rondellen (dikte 2 mm, Ettinger,
Farnell order nr. 1466917) ) gemonteerd met M4x10 cilinderboutjes.
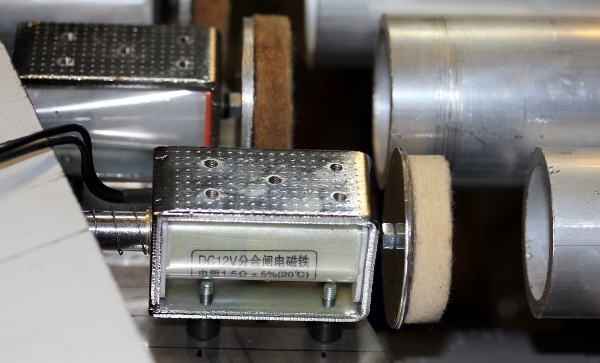
- 01.08.2019: Verder aftekenen van de boorgaten voor de dempers en boren van
de gaten. Uitzagen van de twee kokerprofielen 50x50x5x220 waaraan de kloppers
zullen worden bevestigd. Het lassen op de 10 mm dikke montageplaten moet even
wachten wegens gebrek aan ruimte op de lasttafel. Na een hele dag werken,
hebben we nu al 13 dempers uitgelijnd en gemonteerd. De voorraad M4x10 boutjes
is nu uitgeput.
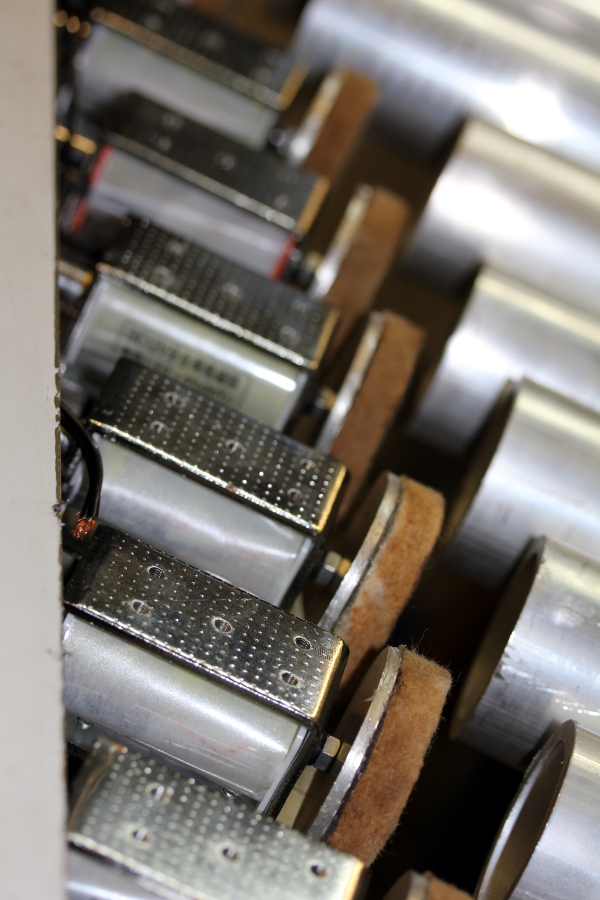
- 02.09.2019: Boren van de gaatjes voor de laatste vijf dempers aan de voorkant.
Bestelling bouten en montagemateriaal bij Fabory. Uittekenen mogelijke bedrading
en gebruik van een konnektor zodat de demperlat eenvoudig losneembaar zou
zijn. We kunnen eventueel hetzelfde type 30-polige konnector gebruiken als
eerder toegepast in <Hybr>. Alvast 6 dikke aluminium schijfjes uitgezaagd
voor de 40 mm diameter klankbuizen aan de achterzijde.
- 03.09.2019: Demperdrager terug helemaal losgenomen om de gaten voor de doorvoer
van de aansluitdraden te kunnen boren. Meteen ook alle boorgaten voor de spoelmontage
ontbraamd. Begin werktekeningen voor de achterzijde, buisophanging. Inox L-profiel
40x40x4 besteld bij Demar-Lux. Aluminium plaatjes voor de dempers aan de 35
mm klankbuizen uitgezaagd.
- 04.09.2019: Maatplan achterzijde uitgewerkt in 1 dimensie:
Te
zagen onderdelen: 4 plaatjes 30x40x3, 50 plaatjes 20x40x3. Montageplaten:
1272 x140 x 4.
- 05.09.2019: Aftekenen van het volledige bouw- en lasplan op de grote 3 mm
dikke achterplaat. De afstanden van nodaal punt tot aanslaglijn werden berekend
en in vertikale getallen op het werkplan aangebracht. Holpijpen besteld bij
Decoene voor de aanmaak van de dempervilten.
- 06.09.2019: De cymbaalviltringen werden geleverd. We kunnen ze, met een
dun laagje siliconenrubber op de dempermagneten bevestigen. De twee 50x50x520
kokerprofielen vastgelast op de 10 mm dikke onderplaten voor de slagmagneten.
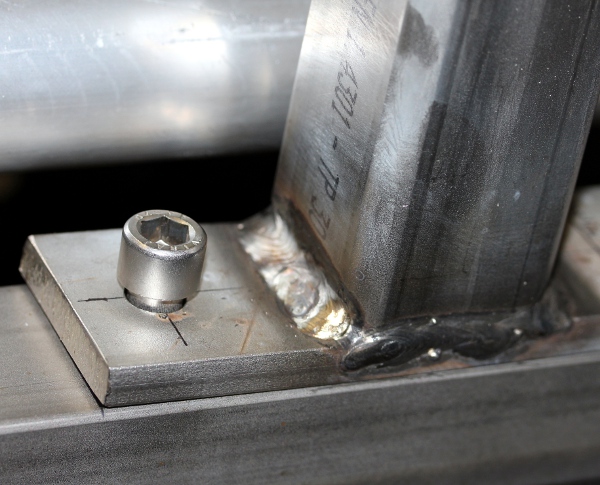
- 07.09.2019: Konstruktie van de drager voor de slagmagneten volgens bouwtekening
17. Aftekenen en boren van alle 72 bevestigingsgaten. Om wat speling te
hebben zijn al deze gaten op 5 mm geboord. Doorvoergaten eveneens geboord
en aan beide kanten gefreesd om beschadiging van de elektrische bedrading
te vermijden. De sleuven voor de afregeling van de slagmagneten werd uitgevoerd
met stukjes 10x3x72, ingelast op de zijkanten:
Testmontage van enkele van de Kuhnke magneten, voorzien van een terugslagdempingsviltring
en bakeliet klopper:
Op de bakeliet kogelknop is hier een viltje aangebracht, maar dat moeten uiteindelijk
dikke stukjes zacht leder worden. Alvast montagegaten geboord voor de plaatsing
van een 30-polige konnektor met meskontakten. Een LED-strip kan eventueel
aan de onderkant over de gehele lengte worden aangebracht.
- 08.09.2019: Soldeerlippen strips gemonteerd aan de binnenzijde van de drager
voor de klopmagneten. Bevestiging op isolatieplaatje met M10 x 3 boutjes.
De slageenheid kan nu gemonteerd worden en vormt een zelfstandig en demonteerbaar
geheel. Hier een zicht op het eerste begin van de opbouw:
De
aanslagkogels in bakeliet en voorzien van een M8 schroefdraad hebben per zes
klankbuizen een verschillende aflopende maat: 40mm, 36mm, 32mm, 25mm.
- 09.09.2019: Boren van de zijdelingse bevestigingsbouten voor de sleuven
van de klopmagneten eenheid: Verzonken M12 x 80 bouten, vier stuks. De gaten
werden geboord en nagehoond op exakt 12 mm. Bij de eindmontage van deze unit
bleken 3 van de 18 schroefdraden (M8) op de Kuhnke magneten beschadigd of
toch minstens onnauwkeurig gedraaid. Deze hebben we opnieuw getapt. Alle kogels
voorzien van 2.5 mm dikke zelfklevende viltjes. Demper terugslagvilten vastgekleefd
op de Banggood magneten met siliconenrubber.
De stalen trappen in het Logos atelier zijn wel erg handig hiervoor... Alle
magneten terug losgenomen om de nog niet geboorde montagegaten te kunnen boren
evenals de 6mm doorvoergaten voor de aansluitdraden.
- 10.09.2019: De klopper eenheid is nu ook voorzien van de witte LED-strip:
Ontwerp van mogelijke
besturingsschakelingen voor de dempermagneten. Puls en hold schakelingen zoals
toegepast in talloze vroegere robots zoals de player-piano zijn mogelijk maar
vergen een groot aantal onderdelen en stellen ook nogal wat eisen aan de firmware
vanwege het oplopend aantal nodige timers. Daarom experimenteerden we wat
met een oeroud recept: het gebruik van gloeilampen als spanningsafhankelijke
weerstanden. Dit pasten we al in 1989 toe in onze <Autosax> robot. Gezien
de grote stroom nodig voor de bekrachtiging van de Banggood spoelen (1.5 Ohm
weerstand bij 12V levert 8A op...), gebruikten we voor onze metingen een zware
12V loodakku als spanningsbron. Hierbij schema en resultaat van de berekening
en de metingen:
Om
de responssnelheid niet nog meer te vertragen dan nodig, gebruikten we hier
geen terugslagdiodes maar wel een stevige MOV van Epcos. Voor de MOSFET kan
ook een IRL640 worden toegepast, maar die dissipeert dan wel 1.5W (Rds_on
= 0.18 Ohm). Voor de IRF3710, met een Rds_on van 18 milliohm, zakt de dissipatie
in de MOSFET tot 154mW. Dit type heeft echter een wat hogere gate spanning
nodig. IRLZ44 of IRLZ34 zijn wat dat betreft betere keuzes. Voor de aansturing
van alle 18 dempermagneten kunnen we nu met een enkele PIC-controller volstaan,
wanneer we een 18F4620 type nemen. Een mogelijk toepasbaar PCB is dit ontwerp
voor een 26-output board, V1.0 23.01.2017:
Een eerste schets van de firmware meteen uitgewerkt. De voeding zou er kunnen
uitzien als:
Met
zo'n ontwerp kunnen maximaal vijf dempers tegelijkertijd geaktiveerd worden.
In de houd-faze is de polifonie beperkt tot tien dempers. Deze beperking heeft
alleen betrekking op het laagste anderhalf oktaaf. De LT1084-12 regulators
zijn niet langer verkrijgbaar bij Farnell, wel nog bij RS-Components. Voor
het PCB kunnen we nagenoeg hetzelfde ontwerp gebruiken als voor <Zi>,
uit 2015. De 12V / 300W transformator (Erea) kunnen we recycleren uit een
vroegere versie van de voeding gebouwd voor <Flex>. Het afgewerkte dempermechanisme,
voorzien van alle dempingsvilten ziet er nu uit als:
Voor de montage van de lampjes is het wachten op de levering van de gepaste
lampvoetjes door Conrad.
- 11.09.2019: Wachten op levering van lampvoeten (Conrad) , MOV's (Farnell)
, LT1084 regulatoren (RS components) .... Een leverancier voor op epoxy gemonteerde
soldeersteuntjes konden we nog niet vinden. Verbeteringen aangebracht aan
het PCB ontwerp voor de 12V-25A voeding, uitgaand van het <Zi> ontwerp.
Voor de bruggelijkrichter kunnen we vier 70HFLR20S02 diodes (70A/100V) gebruiken,
een klassieke 25A brug lijkt immers maar marginaal te volstaan hier.
De
bufferelko kon geen plaats vinden op de printplaat en moet dus extern worden
aangesloten. Hier is het printontwerp:
Film aangemaakt, belicht ontwikkeld, geetst en geboord, En, hier is een foto
van de bestukte print voor deze voeding:
Alleen vijf 47uF kondensatoren onbreken nog op de print. Die zijn in bestelling...
- 12.09.2019: Tests op de voeding voor de 12V dempers. Bedradingsfout in de
gelijkrichtdiodes gekorrigeerd. Voor de besturing van de kloppers zouden we
kunnen uitgaan van het ontwerp gemaakt voor de <Bello> robot. Die PCB's
besturen 1 oktaaf per board en note-repetition met keypressure is goed geimplementeerd
in de firmware. Levering van de Osram 12V/35W halogeenlampjes en de porceleinen
lampvoetjes. Montage- en draaddoorvoergaten geboord op de lage demperunit.
Alle lampjes gemonteerd (elk met twee M3x16 boutjes). Meteen ook gaatjes geboord
voor de draadsteunen van de bedrading. Voor de bedrading moeten we nog wachten
op een levering van Farnell.
- 13.09.2019: 300W - 12V Erea transformator losgemaakt uit de oude <Flex>
voeding. De nog ontbrekende 47uF elkos werden geleverd en meteen ingesoldeerd.
De 12V voeding blijkt perfekt te werken. Volledige montage van dempers en
lampjes afgewerkt. Begin montage van de klankbuizen op dik nylondraad met
tussenviltjes. Hiermee zijn we halfweg geraakt, mede dankzij de hulp van Bert
Vandekerckhove. Toroidale transformator 2 x 35V, 500VA opgedolven uit voorraad.
Ideaal geschikt voor de voeding van de kloppers.
- 14.09.2019: Ontwerp van het draagchassis voor de voedingen, de netspanningsingang,
de hoofdschakelaar en het midi-hub board. Hiervoor gebruiken we een ronde
plaat in aluminium, 20 mm dik. Bevestiging aan het chassis met twee M10 cilinder
bouten en twee M6 bouten, verzonken in het aluminium.
- 15.09.2019: Uittekenen en boren van de montagegaten voor de voedingskomponenten.
IEC netspanningsingangen (chassisdelen) besteld bij Farnell. Alle gaten geboord
en getapt met M3,M4, M5 en M6 schroefdraad, naar gelang de maten van de te
monteren onderdelen. Er is nu plaats voor de 12V-25A voeding, de 100V-6A voeding,
een extra 12V-12.5A SMPS voeding, het hub board met de 5V-2A voeding, de schakelaar
en de IEC ingang en twee MOSFET besturingsprinten voor de lage kant van de
robot. Hier een foto van de voorlopige plaatsing:
Aan
de onderzijde kunnen we nog een blauwe 12V LED spot voorzien.
- 16.09.2019: Opruim atelier. Was stilaan dichtgeslibt geraakt. Verder werk
aan de firmware voor dempers en kloppers.
- 17.09.2019: IEC chassisdelen geleverd en gemonteerd. Zekering van 6A (traag)
geplaatst. Begin PCB ontwerp voor de 18 kloppers.
- 18.09.2019: Verdere afwerking van de ophanging van de klankbuizen voor de
noten 48 tot 65. Bedrading 30-polige konnektor op de kloppers.
De
meskontakten komen op het chassis te zitten, het vrouwelijk deel aan de samen
te stellen multikabel. Alle bedrading gesoldeerd, behalve de zwarte en rode
draden, wegens doorheen de voorraad. Enkele nieuwe haspels 0.5 mm2 draad besteld
bij Farnell. Hierbij het bedradingsplan: 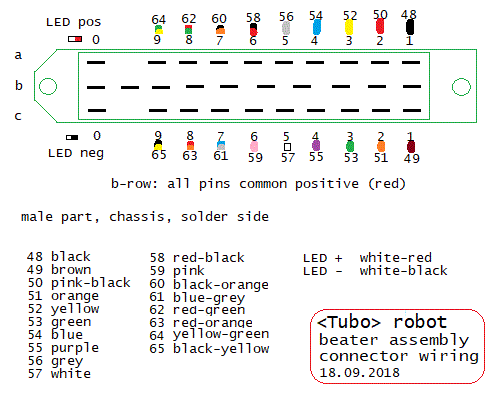
- 19.09.2019: Wachten op levering draad door Farnell... Aangekomen, en meteen
bedrading volledig afgewerkt. VDR's (150V) gemonteerd parallel over de spoelen.
LED-strip vastgekleefd met dubbelzijdig plakband. Rechtstreeks kleven van
de LED strip was onmogelijk, vanwege niet geisoleerd aan de kleefzijde.
Demper unit terug
losgenomen en begin bedrading ervan. De VDR wordt vlakbij de spoelen gesoldeerd.
Hier is de tabel met de voor de dempers gebruikte draadkleuren:
48 |
zwart |
49 |
bruin |
50 |
rood |
51 |
oranje |
52 |
geel |
53 |
groen |
54 |
blauw |
55 |
violet |
56 |
grijs |
57 |
wit |
58 |
zwart-wit |
59 |
zwart-roze |
60 |
zwart-rood |
61
|
zwart-oranje |
62 |
zwart-geel |
63 |
groen-blauw |
64 |
grijs-blauw |
65 |
rood-geel |
Alle bedrading uitgevoerd met 0.5 mm2 draad, behalve de gemeenschappelijke
positieve voedingsdraad, die op 1.5 mm2 werd genomen.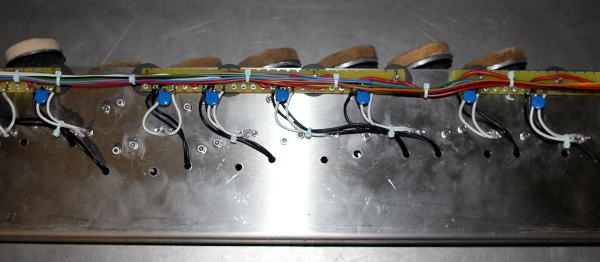
- 20.09.2019: Aanbrengen spirawrap rond de beide kabelbundels. Begin implementatie
van <Tubo> in GMT. Daarzonder kunnen we immers geen testkode maken.
Ikoontje aangemaakt en opgenomen in de resource files. Uitzagen van de dwarsverbindingsbalk
in inox 100x50x3 kokerprofiel. Begin bedrading van de voedingseenheid.
- 21.09.2019: De bestelde holpijpen nodig voor het maken van de vilten voor
de dempers voor de noten 66 tot 91 zijn aangekomen bij De Coene. Verder werk
aan de bedrading van de voedingseenheid voor de noten 48-65.
Hub
en 12V-SMPS doen het al. Ook de andere voedingen werken wanneer we het relais
overbruggen. Begin redaktie van de kode voor het midi-hub board in de Proton+
kompiler. Dit implementeert in eerste plaats een midi-filter en parser en
in tweede orde de besturing van de lampjes in het notenbereik 120-127. De
lampjes voor de noten 120,121 en 122 zijn al toegewezen en bedraad. De parser
introduceert wel een latency van 1 ms in de midi-flow. Hier is het dubbelzijdig
printontwerp:
Hier is het schema van hub-schakeling: 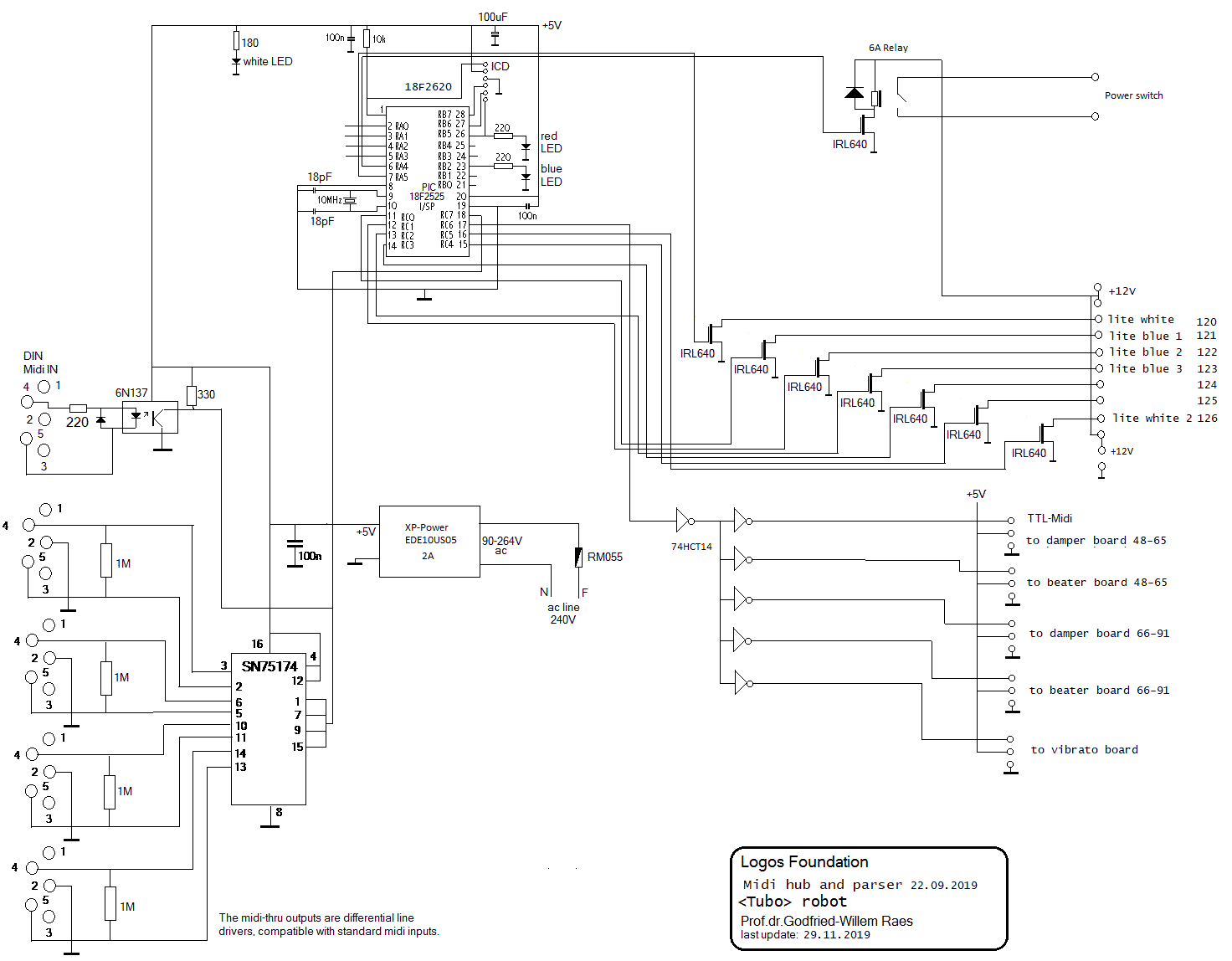
- 22.09.2019: Bestukking van het PCB voor de besturing van de dempers. Hier
gebruiken we slechts 18 van de 26 uitgangen. Dit board krijgt wel de grootste
stromen te verwerken. Voor de power MOSFETS kozen we hier uiteindelijk voor
het type IRLZ34NPBF in TO220 behuizing. Ug= 2V, Uds = 55V, Ids=30A#, Ron=0.035
Ohm. Hier is de datasheet. Merk op dat we op
dit board geen terugslagdiodes monteren, gezien de VDR's over de spoelen.
- 23.09.2019: Tubo helemaal geimplementeerd in GMT. De firmware voor de midi-hub
werkt naar behoren, die voor het demperboard krijgen we maar niet werkend...
- 24.09.2019: Problemen met de firmware voor het demperboard opgelost: de
compiler eist klaarblijkelijk de aanwezigheid van een HRSout instruktie in
de kode als voorwaarde om de midi-in interrupt te kunnen starten.... Versie
1.0 van de demper firmware flashed op het demperboard. De demp pulsduren zijn
nu regelbaar tussen 35ms en 250ms. De timing resolutie is ca. 10us nu. Wachten
op de levering van de ontbrekende IRLZ34 power mosfets...
- 25.09.2019: Afwerking ontwerp van een PCB voor het 4865 beaterboard. Hier
is de film:
(Schaal 200%) Belichten, ontwikkelen, etsen ,boren en solderen van alle nodige
komponenten... Meteen ook twee boards geetst met 26 outputs voor de beaters
en dempers voor de notes 66 tot 91. Deze PCB's zijn grotendeels gelijk aan
die voor het demperboard voor de noten48-65. De film is V1.1- 24.09.2019.
Narekenen van de parameters voor het laag beaterboard: De Kuhke magneten hebben
een weerstand van 36 Ohm (berekend vanuit P=16W bij U=24V, uit het datablad).
Bij 100V trekken ze dus een stroom van 2.76A. Die stroom loopt door de mosfet,
die (voor de IRL640) een Ron heeft van 0.18 Ohm. Derhalve is de dissipatie
in de Mosfet bij bekrachtigde spoel 1.38W. Gezien de duty cycle in normaal
bedrijf beperkt blijft tot 5%, zitten we dus zeker safe wat dat betreft. We
zouden er goed aan doen de duur van de bekrachtigingpulsen te beperken tot
10ms teneinde zeker binnen de safe operation area van de mosfets te blijven.
Alle komponenten op het laag beaterboard gesoldeerd en de processor meteen
van een eerste versie van de firmware voorzien. De terugslagdiodes op deze
print zijn MUR620C types.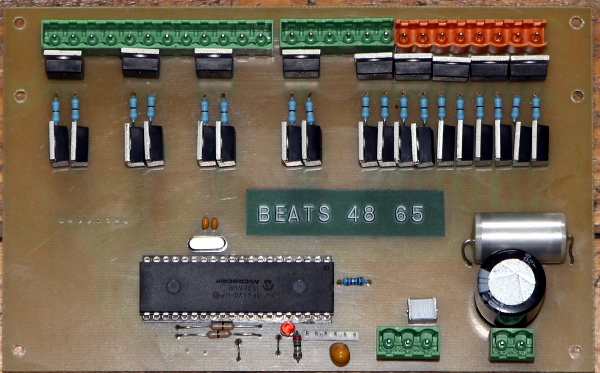
- 26.09.2019: Montagegaten geboord voor de boards op de ronde voedingsplaat.
Verder werk aan de firmware voor de lage dempers. Een eerste beveiliging werd
ingevoerd zodat snel opeenvolgende note-offs niet de aan-tijd van de dempers
steeds maar verlengen. Een begrenzer van de polyfonie moet nog worden toegevoegd,
al zou dat ook te verwezenlijken zijn in de hardware. Nieuwe metingen van
de loopspeed en de pulsduren op het laag beaterboard na aanpassing van de
velo-scaling lookup: loopspeed 111kHz max, 102kHz min. Puls-duur bij velo=1:
30ms, bij velo=127: 150ms. Resolutie: 25us.
- 27.09.2019: Solderen van de twee PCB's voor de dempers en beaters in het
bereik 66-91.
- 28.09.2019: Verder werk aan de bedrading en de assemblage van de voedingsmodule.
Bedrading hub-board. Montage van de blauwe LED spots. De drie processor boards
werken nu en alle voedingsspanningen zijn korrekt bevonden. De module is klaar
voor inbouw in de Tubo robot.
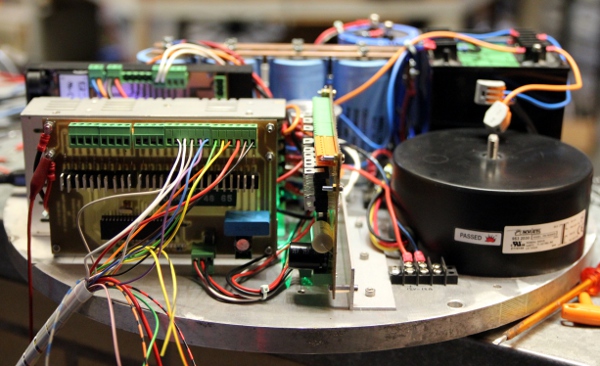
- 29.09.2019: Eerste test waarbij de demper unit, afzonderlijk, wordt verbonden
met de voeding en de overeenkomstige microprocessor. De scaling moet duidelijk
nog worden aangepast en eventueel moeten we het trajekt van de ankers mechanisch
nog verder beperken. Wanneer we met zes demper tegelijkertijd aktief, de voedingsspanning
meten, zakt deze tot 10V. De ingangsspanning van de regulator -gemeten over
de 220mF elko- valt dan terug tot minder van 12V, waardoor de regulering natuurlijk
niet meer kan werken. Met 10 dempers tegelijkertijd aktief, worden ge gelijkrichters
warm. We zouden kunnen de uitgangsspanning van de transformator verhogen door
die primair op de 220V aftakking aan te sluiten, wat leidt tot een 10% hogere
spanning op de sekundaire.
- 30.09.2019: Uitvoerige tests van de beater-module.
Velocity
scalings aangepast in de firmware. Meetgegevens opgenomen in de kommentaren
bij de bronkode voor de betreffende
microcontroller. De pulsduren zijn nu 7.5ms tot 40ms. De haalbare repetitiesnelheid
is beter dan wat we hadden verwacht, ondanks de grote massa van de ankers.
Uiteraard is die repetitiesnelheid groter naarmate de pulsduren korter worden
genomen. Boren van montagegaten in de 100x50 dwarsverstevigingsbalk. Hierop
moeten de PCB's van de noten 66 tot 91 samen met hun voeding gemonteerd kunnen
worden. Het boren moet het inlassen voorafgaan, want eens ingelast is boren
onmogelijk. Ontwerpen uitgetekend voor de bevestiging van de buisresonatoren.
- 01.10.2019: Tubo verlaat voor het eerst de lastafel. Tussenbalk (100x50x2)
aangepunt en hier en daar gelast. Voor het rechtzetten waren wel twee takels
nodig. Demper unit terug gemonteerd. Bestelling 6 elektromagneten voor de
kloppers van de noten 66 tot 71 bij Distrelec. Zagen en stemmen van de PVC
resonatoren voor het laagste oktaaf. De laagste negen noten worden als gesloten
pijp resonatoren uitgevoerd (noten 48 tot en met 56). Vanaf 57 gaan we door
met open pijpen. Op deze wijze wordt de bouwhoogte niet hoger dan de lengte
van de buis voor de laagste noot. Bochten 90 graden aan de resonatoren vastgekleefd
met PVC lijm. Begin van de konstruktie van de verschuifbare afsluitkappen
voor de gesloten pijpen. Voor de laagste pijp kunnen we een inox potje gebruiken
dat heel precies de juiste binnenmaat, 60 mm, heeft. Herkomst onbekend. Ikea,
Casa, Blokker, Hema...?
- 02.10.2019: Beater eenheid op de hoofdstruktuur gemonteerd. Hiervoor zijn
twee mensen nodig!
Voedings
unit op de basis ingepast en vastgezet. Berekening en ontwerp van het resonatormechanisme.
Voor de aandrijving van het vibratomechanisme zouden we kunnen gebruik maken
van een Dunker motor met vertragingskast, voorzien van een excentrisch wiel.
Op voorraad hebben we een motor, type BG40x50, voedingsspanning 24V, 2.1A.
Daarop zit een 4:1 planetaire vertragingskast type PLG42S (90Ncm), waardoor
we een omloopsnelheid krijgen van 910 rpm. De maximale vibratofrekwentie wordt
dan 15Hz, wat hoe dan ook veel te snel is voor de totale massa die we hier
in beweging moeten krijgen.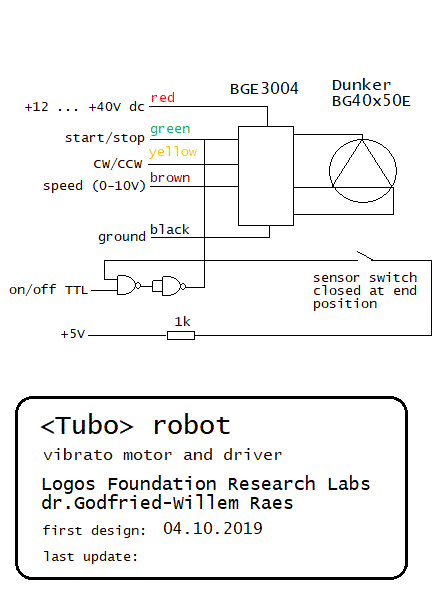
- 03.10.2019: Konstruktie van de lange as voor het vibrato mechaniek: 12mm
gehard inox, lengte 1170mm. De vier draaipunten gemaakt in 10 mm dik aluminium
(50x100x10), aan de onderzijde voorzien van twee ingetapte M4 schroefdraden
voor de bevestiging aan de inox plaat waarop de resonatoren gemonteerd worden.
Montage van de resonatoren met 10 mm dikke afstandhouders in aluminium, gemonteerd
met twee M4 schroeven en ingetapte schroefdraden in de aluminium plaatjes
(100 x 40 x 10). Hier is een zicht op de nog onvolledig gemonteerde resonator
zijde:
We hebben
wel een probleem met torsie op de montageplaat van de resonatoren, waardoor
de meenemer niet gelijktijdig alle resonators doet bewegen.
- 04.10.2019: Experimenten rond het verhelpen van het torsieprobleem: versteviging
van de bevestigingslat of plaatsing van een tegengewicht? Konstruktie van
de ontbrekende hoedjes voor de gesloten pijp resonatoren op de laagste buizen.
Vastkleven van de bochten op de resonatoren voor de noten 60 tot 65 met PVC
lijm. We zijn bijna halfweg de konstruktie van de <Tubo> robot nu...
- 05.10.2019: Verder werk aan de versteviging van de resonatordrager: Aluminium
L-profiel (50x30x3) vastgemaakt op de 10 mm dikke asdragers in aluminium.
Hiertoe werden M4 schroefdraden in de asdragers getapt. Aan de kant van de
hoge noten moesten we het profiel wat taps laten uitlopen om kontakt met de
klankbuisdragers te vermijden. Voor het terugplaatsen van de as zijn weer
twee mensen nodig. Voor de beweging aangedreven met de motor moeten we nu
nog een U-beugel lassen die zowel aan de voor- als aan de achterzijde vastgeschroefd
wordt op de resonator unit. Die gelaste beugel (4 M4 bevestigingsgaten , twee
aan elke zijde het de unit) met een inox plaat in de dikterichting wordt dan
door de motor met excentriek bestuurd. Doorbuiging wordt zodoende zo goed
als uitgesloten. Mekaniek volledig afgewerkt, getest op geluidloze werking
en meteen ook de kracht opgemeten nodig om het vibrato mekanisme in beweging
te brengen: 10 Newton, minder dan wat we hadden verwacht.
- 06.10.2019: We krijgen onze Dunker motor maar niet aan de praat... Dan maar
een ander type besteld bij RS-components: Een Crouzetmotor met vertragingskast,
24V, 147rpm, 5Nm. Bij Farnell bleek identiek hetzelfde type zowat het dubbele
te kosten: 493 Euro, versus RS: 246 Euro. (Prijzen zonder BTW). Dergelijke
motoren pasten we al eerder toe in robots zoals <Ob>. Met het hier gekozen
type moeten we voor de maximale vibrato frekwentie uitkomen op 2.45Hz, wat
gezien de toch wel grote massa van het mekanisme in de buurt moet komen van
het maximum haalbare. Voor een trajekt van 20mm -bepalend voor de vibrato
amplitude modulatie- kunnen we een excentrisch aswiel toepassen alsvolgt:
Deze
maatschets geldt voor een motor met een as van 8 mm. Om het wiel op de as
vast te zetten voorzien we een ingetapte M4 schroefdraad waarin een verzonken
M4 inbus stelschroef kan worden geschroefd. Elektrisch gezien kan de besturing
zo gebeuren:
De microswitch verbreekt het kontakt met de voedingsspanning op het moment
dat de eindpositie (die waarbij de resonatoren het dichtst bij de klankbuizen
staan) bereikt is. Deze sensor-switch wordt overbrugd met een relais waardoor
bereikt wordt dat bij ontvangst van een motor stop kommando, de motor steeds
blijft draaien tot die eindpositie is bereikt. Dit systeem werkt natuurlijk
alleen wanneer de PWM uitsturing steeds minstens die waarde heeft, nodig om
de motor te doen draaien. Voorwaarde voor een goede werking is dat de microswitch
lang genoeg ingedrukt moeten blijven om de inertie van de motor te overbruggen.
Precieze mechanische afregeling is hier aangewezen.
- 07.10.2019: Er moet een kortsluiting ontstaan zijn op de geel-rode draad
voor demper 65. Wellicht in de lampvoet. Voor het overige blijkt alles goed
te werken, maar uiteraard moeten hamers en dempers nog worden afgesteld. Begin
met het uitzagen en boren van de ophangstukjes (inox plat 20x3) voor de klankbuizen
66-91. Op de bestelde Crouzet motor wachten we nog...
- 08.10.2019: Begin TIG laswerk buisdrager achterzijde.
- 09.10.2019: Zagen, boren, frezen en oplassen ophangplaatjes bovenrij klankbuizen...
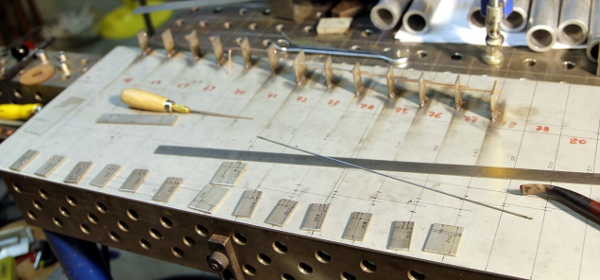
- 10.10.2019: en meer daarvan, al komt het einde nu wel in zicht. De Crouzet
motor is inmiddels aangekomen... Eerste test van het mechanisme met de excentriek.
- 11.10.2019: Klankbuizen voor de noten 84 tot 91 gezaagd en nauwkeurig gestemd.
Ophanggaatjes in de buizen geboord. (3 mm boormaat)
30mm / 20mm tube: (1.060 kg/m)
midi note |
frequency (Hz) |
length (mm) |
suspension |
m constant |
weigth kg |
84 |
1046.5 |
391.5 |
87.8 |
1.1203 |
|
85 |
1108.7 |
380 |
85.2 |
1.1182 |
|
86 |
1174.66 |
369 |
82.7 |
1.1171 |
|
87 |
1244.51 |
357 |
80 |
1.1078 |
|
88 |
1318.5 |
347.5 |
77.9 |
1.112 |
|
89 |
1396.9 |
336 |
75.3 |
1.1014 |
|
90 |
1479 |
326.5 |
73.2 |
1.1019 |
|
91 |
1567 |
316.8 |
71.0 |
1.0991 |
|
Laatste faze boren, vijlen en oplassen van de ophangplaatjes voor het hoogste
oktaaf.
Hiervoor
maakten we geen afzonderlijke werktekening, maar tekenden het ontwerp meteen
uit op de inox plaat zelf.
- 12.10.2019: Splitten van de gelaste dragerplaat. Plasma snijwerk. De nodige
afstand tussen beide montageplaten is nu 110 mm. Uittekenen van de montagemogelijkheden
en de aanhechting op het hoofdchassis. Het wordt bijzonder moeilijk om binnen
de maten van de wielbasis te blijven... Voor de kloppers staan we voor de
keuzemogelijkheden: 6 x Kuhnke H6288RF (66-71), 6 x Tremba ZMF3865 (72-77),
14 x Tremba ZMF3258 waarbij we moeten rekening houden met de verschillende
bouwdieptes en kracht kurves, ofwel 28 Tremba ZMF3258, waarbij de massa van
de ankers echter aan de kleine kant is voor het laagste oktaaf hier.
- 13.10.2019: De logische bouwvolgorde dikteert dat we eerst de drager voor
de resonatoren moeten maken. De as waarrond deze drager kan draaien moet bevestigbaar
zijn op de achterzijde van de klankbuizendrager. Begin konstruktie van de
drager voor de resonatoren 66-91. Hiervoor gebruiken we inox plat 60x 1135
x 5. Gaten geboord (4 mm) voor de bevestiging van de resonatoren met nylon
kabelbinders, in totaal 134 gaatjes... Om resonatoren te maken vanaf de buizen
78 en verder, moeten we PVC buis inkopen, ofwel 25 mm koper bochten gebruiken
met messing buis (in voorraad). As van 12 mm hebben we niet meer in voorraad.
Kunnen we ook 10 mm gebruiken?
- 14.10.2019: Ontbrekende bouten, moeren en kogelknoppen besteld bij Fabory.
Montageplan voor de resonatoren uitgetekend:
Voor de resonatoren van de noten 83 tot 91 gaan we koperbuis (buitendiameter
28 mm, 3/4" gasbuis) gebruiken, met haakse soldeerbochten en moffen om
te stemmen. Audenaert, onze gebruikelijke sanitair handel, is evenwel gesloten
op maandag... De afwerking van de resonatoren moet dus nog wat worden uitgesteld.
- 15.10.2019: Konstruktie van de asdragers voor de resonator eenheid. We gaan
uit van een geharde as van 10 mm. Vier inox platen, na boren van het asgat,
gelast op de resonatordrager. Tegenlassen uitgevoerd om de kromtrekking te
kompenseren.
Alle
resonatoren voor de noten 83 tot 91 gemaakt en gestemd. Uitvoering in rood
koper, niet omdat dat beter zou zijn dan PVC, maar gewoon omdat we dat in
voorraad hadden. Audenaert had gelukkig de nodige bochten op voorraad.
Voor
de aandrijving met de vibrato motor lasten we meteen ook een stuk plat op
de drager. (20 x 3 x 25). De hoge noten eenheid krijgt daarmee dus definitief
een afzonderlijke motor. Een synchroon blijvend vibrato tussen lage noten
(48-65) en hoge (66-91) kan niet worden gegarandeerd op grond van de eigenschappen
van de gebruikte DC motoren.
- 16.10.2019: Testmontage van de resonatoren. Konstruktie van de afstandhouders
voor de resonatoren. Hiervoor gebruikten we houten latjes, vastgekleefd met
epoxyhars. De roodkoperen resonatoren krijgen een klemlatje eveneens in rood
koper. Voor de resonator voor noot 91 dienden we een kunstgreep uit te halen:
hiervoor maakten we een beugeltje. Lijmen van de kniestukjes.
- 17.10.2019: Korrigeren van de stemming van de resonatoren. Sommige moeten
we opnieuw bouwen, zonder stemflens, want deze verhindert de doorgang van
de lange as. De resonator module is nu afgewerkt:
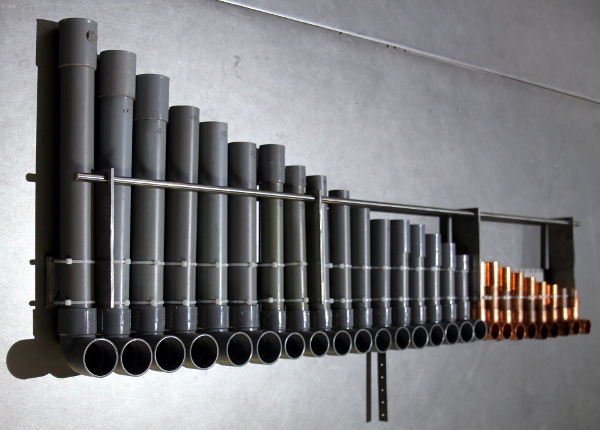
- 18.10.2019: Zagen en boren van de asdragers voor de resonator eenheid op
de klankbuizen drager. Uitzagen en boren van de verbinding tussen boven- en
onderdeel van de klankbuizendrager. Asdragers (vier stuks) gelast op de achterzijde
van de bovenplaat. Test montage van de as waarmee beide eenheden worden verbonden.
Bewegingstest van het vibrato mechanisme. Dit lijkt te werken, maar we moeten
de amplitude zeker beperken. Ook moeten asborgingsringen (10 mm) op de as
worden gezet om horizontaal verschuiven van de resonatoren onmogelijk te maken.
Testmontage met een zestal klankbuizen. Uittekenen van de konstruktie van
de klopper-eenheid.
- 19.10.2019: Aanlassen van de onderkant van de klankbuizenhouder. Konstruktie
van de afstandhouders tot het hoofdchassis: hiervoor gebruikten we vier uitgezaagde
stukken kokerprofiel 100x100x6 afgezaagd op 50 mm lengte.
Konstruktie van een excentrisch aandrijfwiel voor het vibratomechanisme.
De
beweging hiervan verloopt inherent sinusoidaal, aangezien het de projektie
is van een punt op een cirkel. De motor wordt op de onderste klankbuishouder
bevestigd middels een paar stevige inox beugels gelast op een 10 mm dikke
onderplaat. De beugels worden met een laagje rubber bekleed om het motorgeluid
zoveel mogelijk te dempen . Het excentrisch wieltje, 10 mm dik, werd op de
draaibank vervaardigd uit sinterstaal, uitgaand van een onderdeel gedemonteerd
uit een defekte platendraaier.
- 20.10.2019: Verdere afwerking en afregeling van het vibrato mechanisme 66-91.
Kracht nodig om
de resonatoren te doen bewegen nagemeten met een veerbalans: 5 Newton. De
motor maakt evenwel meer geluid dan wenselijk is... Volgens de opgave van
de fabrikant is het moment van de motor 0.9Nm op een as van 8 mm. De kracht
leverbaar bij maximale uitwijking van onze excentriek (32.4mm) moet dan volgens
onze berekening 7.29 Newton zijn, groter dus dan de 5 Newton die we nodig
hebben. De wrijving lieten we hier buiten beschouwing. De formule voor de
maximale kracht in funktie van de draaiingshoek wordt dan K= 2.7 + sin(a).
4.59 (In Newton), wat betekent dat die kracht negatief wordt bij terugvallende
beweging. De stroomopname van de motor verloopt evenredig met deze kracht,
met dien verstande dat de stroom nooit negatief wordt en de motor dus nooit
generatorisch werkt. Dit is o.i. toe te schrijven aan de relatief grote wrijving.
Om de wrijving (en het bijgeluid...) wat te verminderen, bevestigden we een
uitgefreesd stuk PTFE (Teflon) om het plat inox waarmee het mechanisme aangdreven
wordt.
- 21.10.2019: Konstruktie van het vibrato mechanisme voor de noten 48-65.
Hier gebruiken we de wat krachtiger Crouzet motor. De basisplaat is inox 240
mm x 100 mm x 2 en wordt gemonteerd op zes M6 MF trillingsdempers.
De meenemer, ook hier weer bekleed met een stuk uitgefreesd Teflon, op maat
gesneden en gemonteerd:
Motor gemonteerd met de excentriek, hier buitendiameter 60 mm, amplitude van
de beweging 30 mm. De gemonteerde unit ziet er nu zo uit:
Het excentrisch wiel werd met een gatfrees gemaakt uit 10 mm dik roestvast
staal. Tests uitgevoerd met een labo voeding. Het stroomverbruik bij maximale
belasting beloopt 300 mA bij 24 V. Bij aansturing met 1.5 V loopt de motor
nog steeds goed en is de stroom maximaal 240 mA. Ook deze motor maakt meer
lawaai dan wenselijk is... Het lawaai is recht evenredig met het toerental.
Voor de positie sensors zagen we uiteindelijk toch af van het gebruik van
microswitches. De Pepperl+Fuchs inductieve sensors (NJ2V3N) die we gebruikten
in robots zoals <Chi> en <Korn> blijken niet langer in productie
te zijn... Dan maar geopteerd voor Omron sensoren. Type E2A-M12KS04-WPC12M
hadden we nog in tweevoud op voorraad.
- 22.10.2019: Montage van de sensoren voor de vibrato motoren. Voor de 66-91
kant, lasten we een L-beugeltje op de dragerplaat, voorzien van een sensor
montagegat van 12 mm. Voor de 48-65 kant met de Crouzet motor gebruikten we
een 30 mm brede L-beugel, vastgezet met een lange M6 bout. Hoewel het perfekt
mogelijk is beide motoren met een enkele microprocessor te besturen, beslisten
we toch om voor elke motor een afzonderlijke PIC microprocessor in te zetten.
De modulaire opbouw blijft zo gehandhaafd en het afregelen en debuggen wordt
op die wijze aanzienlijk eenvoudiger. Alleen de noodzakelijke 24V voeding
voor motoren en sensors kan gemeenschappelijk worden gehouden. Begin ontwerp
van een motor besturingsschakeling, gebruik makend van een Microchip 24EP128MO202
controller:
Hiervoor moeten we uiteraard nog een PCB ontwerpen. Het signaal van de nabijheidssensor
wordt na verzwakking tot 2.85V, verbonden met de external interrupt ingang
van de processor. Wanneer een vibrato-off kommando via midi wordt ontvangen,
vertraagt de motor tot een mininale snelheid en pas wanneer dan de sensor
interrupt (op de neergaande flank van het sensor signaal) wordt ontvangen,
wordt de motor uitgeschakeld. De processor zorgt ook voor parsed midi-out,
waarmee het tweede vibrato board kan worden bestuurd.
- 23.10.2019: PCB layout uitgetekend voor de besturing van beide vibrator
motors:
Deze print heeft de afmetingen 80 x 110, zodat hij op maat is voor montage
op de 100 mm brede tussenliggers in Tubo. De afbeelding hier is op 200% en
moet dus 50% worden verkleind voor de aanmaak van de films. Van deze print
hebben we twee exemplaren nodig. Film gemaakt, print belicht, ontwikkeld en
geetst. Iets moet wat fout zijn gegaan want de print vertoonde nogal wat dooretsingen.
Ofwel was onze fotoprintplaat al te oud, onze ontwikkelaar uitgeput of ons
etsbad te warm... Met wat extra soldeer is een en ander echter wel recht te
zetten. Na boren, beide prints bestukt en gesoldeerd. Hier is een foto van
de afgewerkte PCB's: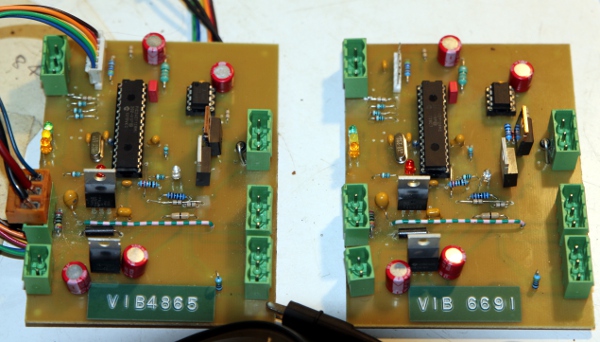
- 24.10.2019: Hardware tests van de bestukte prints voor de vibrato motoren.
Tests met alle voedingsspanningen aangesloten, maar nog zonder motor. Begin
van de redaktie van de firmware. Tegen het eind van de dag hadden we een eerste
werkende versie van de firmware klaar. De PWM blijkt goed te werken, de midi-thru
eveneens. De geleidelijke slowdown bij het uitschakelen van de motor werd
geimplementeerd en op werking getest op de skoop. Het sensor signaal doet
wat het geacht wordt te doen. Hoewel vrij simpel te realiseren, verzaken we
aan het implementeren van een ramp-up bij versnelling van de motoren. De inertie
van de motoren zelf maakt dit eigenlijk overbodig. Voor de kompilatie van
de firmware voor beide board gebruiken we dezelfde kode. Voor kompilatie van
de hex-dump voor elk van beide boards moet de metacompiler konstante Vib4865
ofwel Vib6691 in de source code worden gedefinieerd. In de robot moet de midi-in
van het Vib6691 board verbonden worden met de midi-out konnektor van het Vib4865
board. Lees aandachtig de source
kode!
- 25.10.2019: Testkode in GMT aangepast aan de nieuw geintroduceerde Tubo
controllers. Eerste tests met de gemonteerde Crouzet motor voor 4865. Na alles
te hebben aangesloten blijkt helemaal niks te werken... Grondig nazicht van
de vibrato PCB's maakten duidelijk dat we de MOSFET's verkeerd hebben ingesoldeerd...
Na korrektie blijkt de motor bij ctrl66 > 0 perfekt te doen wat we verwachten,
maar daarna niks meer...
- 26.10.2019: Op de oscilloscoop, zonder aangesloten motor, ziet alles er
goed uit. Met motor aangesloten konstateren we heel wat glitches op de voedingslijnen
en op ground. Die zouden er de oorzaak kunnen van zijn dat midi kommando's
niet goed worden ontvangen wanneer de motor loopt. Enkele 2u2 polyesterkondensatoren
bijgeplaatst over de 24V voedingslijnen, maar dat maakte niet bijzonder veel
verschil. Uiteindelijk de bug gevonden: het had helemaal niks te maken met
het ontwerp van het motorboard, maar het midi-hub board van <Tubo> blokkeerde
gewoonweg de nodige controllers voor de motor boards. Hub board firmware aangepast...
Teruggekomen op de eerste beslissing om geen ramping te gebruiken bij acceleratie.
Dit hebben we nu wel geimplementeerd omdat uit experimenten bleek dat heel
plotse versnellingen motorboating kunnen veroorzaken op de 24V SMPS voedingsmodule
(hick-up behavior).
- 27.10.2019: De moeilijke bereikbaarheid van het midi-hub board, dat we nu
van nieuwe firmware moeten voorzien, speelt ons parten. Zonder de 12V SMPS
voeding los te nemen, is het bijzonder moeilijk om de programmeerkonnektor
te bereiken en aan te sluiten. Daarom maakten we een speciale haakse konnektor
op een 160mm lang stukje gaatjesprint met doorlopende banen:
Met dit hulpstuk kan het midi-hub board met het PICkit3 interface geprogrammeerd
worden zonder ook maar iets te moeten losnemen. Het vibrato mechanisme en
de besturing ervan werken nu helemaal naar behoren. Alle komponenten gemonteerd
en bedraad op het chassis. Alles blijkt nu naar behoren te werken.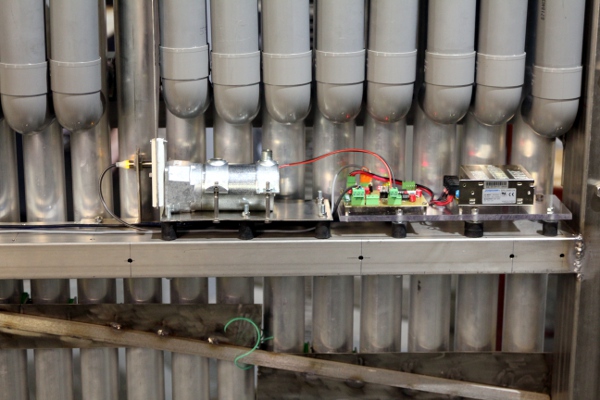
- 28.10.2019: Resonator voor noot 56 opnieuw gebouwd en gestemd als halve
golflengteresonator. (60 mm PVC). Klopppers voor 48-65 voorzien van een dubbele
laag vilt, de aanslag was immers nog veel te hard. Verder nu met de kant voor
de noten 66-91... De minimale motorspanning voor een zekere aanloop bij de
McLennan vibrato motor is 2.7V. Firmware alvast aangepast met deze parameter.
Bouten M6 x 55 te bestellen evenals M6 FF trillingsdempers. Voorraad elektronische
komponenten aangevuld met een bestelling bij Farnell. Drager voor de elektromagneten
66-91 gelast: twee 30x30x3 L profielen en stukjes plat 90 x 10 x 3 op de uiteinden,
voor verstelbare montage met M10 bouten. Lengte 1172 mm, hoogte 309 mm, diepte
60 mm. Nu moeten de maten voor de positionering van de kloppers heel precies
worden overgebracht op deze unit.
- 29.10.2019: Aanmaak van boormallen voor de plaatsing van de kloppermagneten.
Boorwerk in de kloppermagneetdrager 66-91. Alle gaten oversized op 4 mm om
uitlijning mogelijk te maken. Doorvoergaten boren (6mm) voor de bedrading
evenals montagegaten voor de soldeerlijsten. De Tremba magneten moeten op
een verhoging van 3.1 mm gemonteerd worden. PTFE plaat gebruiken?
- 30.10.2019: Afslijpen voetplaten van 14 Tremba magneten op 40 mm breedte,
voor de hoogste kloppertjes. Afsnijden van PTFE strips op 40 mm breedte. Boren
van de montagegaten voor de 66-91 unit op de vertikale kolommen van het hoofdchassis.
Montage van de elektromagneten op de drager.
Zoektocht
naar een leverancier van soldeersteuntjes... Wachten op levering van de Banggood
magneten voor de hoge dempers. Nieuwe bestelling bij Fabory: onze voorraad
M3 inox boutjes raakt uitgeput...
- 31.10.2019: Konstruktie van de verstelbare houder voor de klopper-unit 66-91.
Uitzagen twee stuks kokerprofiel 50x50x160x8. Werktekening:
Het
kloppermechanisme wordt zijdelings vastgezet met vier M10 cilinderbouten.
Aan de buitenzijde werden grote gaten (20mm) uitgespaard om deze bouten door
te laten zonder zijdelingse uitsteeksels. Kokerprofielen (50x50x5x160) vastgelast
aan de 10 mm dikke montageplaten. Eerste testmontage van de klopper-unit op
het chassis van de noten 66 tot 91. 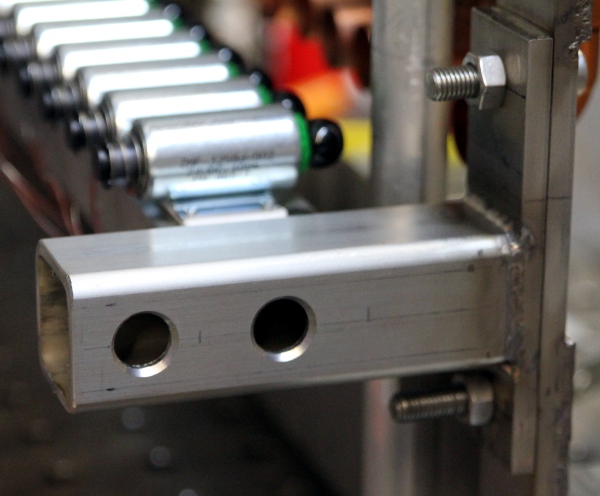
- 01.11.2019: Verifikatie van de maatvoering. Om de overgang tussen noten
65 en 66 geleidelijker te maken kunnen we de ankermassa van de magneten voor
66 e.v. wat vergroten met blokjes rood koper. Schakelschema voor de beater-
en demperboards opnieuw uitgetekend. Het schema stemt nu weer perfekt overeen
met de PCB's.
Bedrading van de klopperunit voor 66-91. Ook hier voorzagen we een witte LED
strip onderin de unit, vastgekleefd met dubbelzijdig plakband. De draadsteuntjes
(4 10 polige steuntjes) werden gemonteerd op PTFE strips om ze van het chassis
geisoleerd te houden. Hier is het bedradingsschema met aanduiding van de gebruikte
draadkleuren:
Alle met rode cirkels aangegeven punten zijn onderling doorverbonden en worden
aangesloten op de gemene 100V voedingsspanning. De witte LED-strip heeft een
voedingsspanning van 12V en moet worden aangesloten op het midi-hub board
in het hoofdchassis.
- 02.11.2019: Solderen van alle komponenten op het beater-besturingsboard.
De MOSFET's op dit board zijn IRL640, onze voorraad raakt echter uitgeput.
Opnieuw besteld bij Farnell. Polykarbonaatplaat uitgezaagd voor dit PCB en
montage op de rechterachterzijde van de 6691 unit. De montage op de 4 mm dikke
inox plaat gebeurt middels vier M4-FF trillingsdempers. Alle Weidmueller konnektors
(2x 8 polig en 2x5 polig) bedraad en aangesloten.
Hoe
we de twee draden voor de LED strip elegant kunnen verbinden met het midi-hub
board is voorlopig nog onopgelost. Ideaal ware hier een enkele konnektor voor
lichtjes, voedingsspanningen, motor en midi signalen. Experimenten uitgevoerd
met gebruik van 32 mm bakeliet kogelknoppen op de Kuhnke 66-71 magneten. Daarvoor
moeten we wel schroefdraadadapters M8-M4, lengte 10mm, maken. Ideaal zouden
we dan voor de noten 72-77 kogelknoppen van 25 mm moeten gebruiken. Eerste
versie van de firmware voor dit board uitgewerkt. De lookup tabellen voor
de velocities moeten nog aangepast worden aan metingen op het instrument zelf.
- 03.11.2019: Konstruktie van schroefdraad adaptors M8-M4. Hiervoor vertrekken
we van korte M8 bouten waarin we op de draaibank een doorlopend gat van 3.3
mm boren. Hierin tapten we dan handmatig M4 schroefdraad met een 3-tappensetje.
Na het tappen wordt de kop van de bout op 10 mm lengte afgedraaid. .Op deze
wijze monteerden we de zes kloppers, diameter 32 mm, voor de noten 66 tot
71 op de Kuhnke magneten. Voor de noten 72 tot 77 gingen we uit van 10 mm
M8 bouten met verzonken kop. Voor de noten 78 tot 83, hetzelfde procede toegepast
maar nu voor voor M6 naar M4 schroefdraad, dit om 25 mm kogels op de M4 ankers
te monteren. Dit blijkt heel wat moeilijker te maken, zeker in inox... Voor
de hoogste noten kunnen we M4 kogels gebruiken op een M4 MF afstandbus.
- 04.11.2019: Solderen van de komponenten op het 66-91 demperboard. De MOSFET's
hier zijn IRLZ34NPBF en de diodes BYV32-200 types. Eerste versie van de firmware
voor dit board geschreven en geprogrammeerd in de microprocessor. Eerste hard-
en firmware tests passed. Het pulsduurbereik voor de dempers is in deze eerste
versie van 30 ms (voor release=1) tot 280 ms (release=127). De lussnelheid
-en dus ook de resolutie van de timers- is ca. 7 us. In de firmware voorzagen
we nu ook een kontrole op het aantal gelijktijdig aktieve dempers. Met onze
12A voeding moet het gelijktijdig bekrachtigen van 40 spoelen die elk 300mA
trekken, nochtans mogelijk zijn. Levering boutjes van Fabory toegekomen. We
beginnen te begrijpen waarom Thorlabs Gmbh meer dan 4 euro per stuk rekent
voor M4-M6 schroefdraadadapters (type AE4M6M) : meer dan de helft van onze
pogingen om ze zelf te fabriceren mislukt... Niettemin monteerden we onze
gelukte zelfgefabriceerde adapters al voor de noten 78,79,80 en 81.
- 05.11.2019: Levering Farnell: IRL640 MOSFET's. Afwerking van het PCB voor
de kloppers 6691 met de verse IRL640's. M3 aansluitingen voor de voeding opgesoldeerd.
Verder afregelen van de kloppertjes. Aanmaak van nog enkele M6-M4 schroefdraadadapters.
- 06.11.2019: Proton compiler upgrade gedownload. Nu Proton 8, versie 3.7.3.1
en Proton 24, versie 1.0.6.4. Dit bleek geen bijzondere problemen op te leveren.
Levering van M6-M4 adapters door Thorlabs Gmbh. Eerste presentatie van de
6691 unit op het hoofdchassis met de hulp van Mattias Parent en Bert Vandekerkhove.
De bevestigingsgaten moeten bijgewerkt worden en er moeten afstandsbussen
van 10 mm tussen beide modules komen. Zoniet, raken de resonatoren elkaar
in hun uiterste stand. Onze voorziene M12 bouten worden dan wel te kort...

- 07.11.2019: Onze oude handboormachine (een Metabo uit 1973...) blijkt niet
opgewassen tegen de kracht nodig voor het uitboren van de gaten in 8 mm dik
inox. Uitkijken dus naar een nieuwe Fein machine. De BOS16 lijkt wel geschikt:
boorkapaciteit tot 16 mm in inox.
Bij
Welda blijken ze uit voorraad leverbaar. Daarheen dan maar. Meteen uitgetest
en uistekend bevonden. Alle gaten voor de bevestiging van de 6691 unit aan
het hoofdchassis zijn nu geboord. Tussen beide unit voorzagen we nylon rondellen
(11mm dik, gat 12mm, diameter 40mm).
- 08.11.2019: Levering van de Banggood magneten, typeJF-0530B. Uitgetest en
niet goed bevonden: ze trekken 1A bij 12V, ver van de gespecifieerde 300mA
dus. Bovendien worden ze vervaarlijk heet bij 12V. De responssnelheid is bovendien
erg traag en de aanvangskracht veel te gering voor onze toepassing. Dan maar
besloten om alvast voor de noten 66 tot en met 77, Tremba magneten te gebruiken,
type ZMF-3258d.001, werkend op 12V. De DC weerstand is 11 Ohm, in koude toestand.
Alvast acht dempermagneten klaargemaakt: 10mm dik vilt uitgestanst, aluminium
plaatjes met M4 schroefdraad getapt en op de magneten gemonteerd. Voor de
demping van de terugslag brachten we groene viltjes aan van 5 mm dikte.
- 09.11.2019: Uittekenen van de diverse mogelijkheden voor de konstruktie
van de demper 6691 unit. Voor de hoogste 14 tonen zouden we ook hetzij Lucas-Ledex
195-225-229, hezij Black knight 121-420-620-620 kunnen gebruiken. Dit zijn
cilindrische solenoids met een diameter van 20 mm. De koudweerstand van de
Lucas-Ledex types is 12.4 Ohm (vier stuks op voorraad) , die van de Black
Knight's 19.8 Ohm (11 stuks op voorraad). Beide types hebben een anker uitmondend
in een staaf van 2.5 mm. Daarop kunnen we -hoewel een moeilijk werkje- schroefdraad
M2.5 tappen. M2.5 moeren moeten we dan wel bestellen, want niet in voldoende
aantal op voorraad. De dragerplaat kunnen we uitsnijden uit 2 mm dik inox,
maar dan zijn wel versterkingprofielen op de achterzijde nodig, om doorbuigen
tegen te gaan. Ook deze module kunnen we losneembaar maken door ze op twee
stukken kokerprofiel 100x100x8x50 vast te lassen. Hier is een eerste ontwerp
van maatvoering:
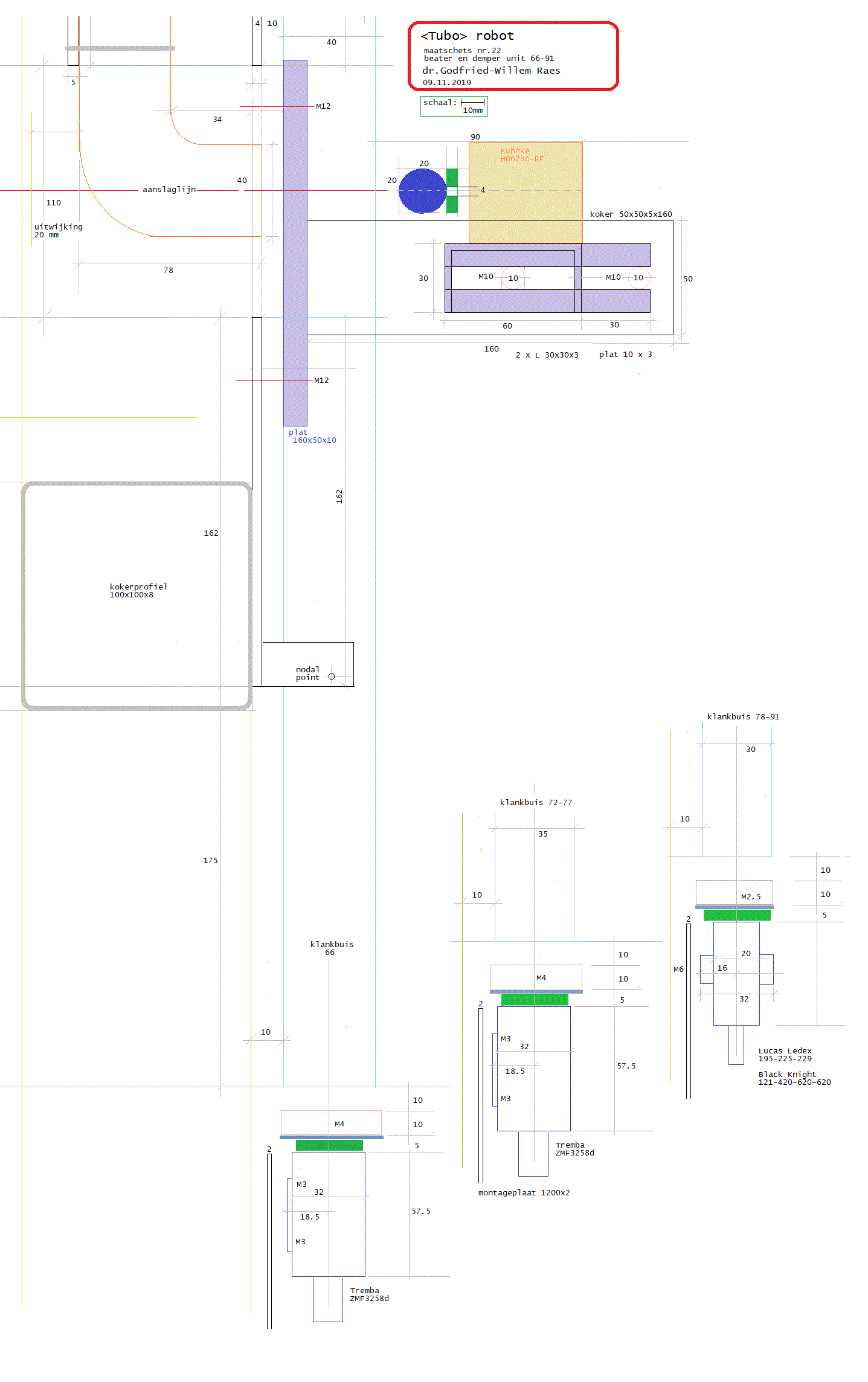
- 10.09.2019: Uitsnijden en aftekenen montageplaat voor de dempers. Afdraaien
van de nylon afstandhouders, boren van de montagegaten in de hoofdstruktuur.
Bijsnijden van de 4 mm dikke bevestigingsplaat vanaf noot 80 tot en met 91:
de onderzijde van de klankbuizen moet vrij zijn om de dempers foutloos te
kunnen laten werken. Atelierbezoek van Prof.dr.Yu Wakao, uit Hiroshima en
dr. Junko Tanaka. Meteen ook het <Plus-Minus> projekt voorgesteld.
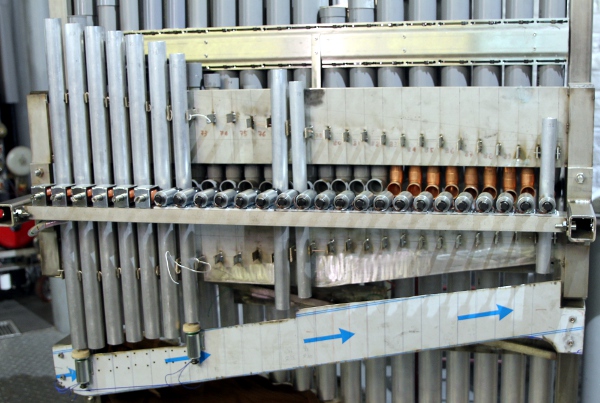
- 11.09.2019: Er blijken wat foutjes in onze maatschetsen voor de 6691 demper-eenheid
te zijn geslopen. Opnieuw alles goed nameten is de boodschap. De montageplaat
voor de dempers zal in elk geval een versteviging nodig hebben om oscillaties
en doorbuiging te voorkomen. Hiervoor kunnen we 25x25x2 kokerprofiel gebruiken
of ook 30x30x3 L-profiel. Montageplaat helemaal uitgesneden, met afrondingen,
en met 4 M8 bouten gemonteerd op de twee 100x100x5 kokerprofielen. Eerste
reeks van 7 x 4 gaatjes geboord voor de bevestiging van de Tremba magneten.
Testassemblage. Lucas-Ledex en Black Knight solenoiden voorzien van M6 stelschroeven,
stelringen en buitenmoeren voor montage op de dempereenheid.
- 12.09.2019: We zijn dringend aan de vervanging toe van onze kobalt boren
in de maten 8 tot 16 mm... Maten 9, 9.5, 10.5, 11, 11.5, 12.5 en 13mm ingekocht
bij De Coene. Snijden van M2.5 schroefdraad op de veertien ankers van de Lucas-Ledex
en Black Knight solenoiden. Een houder voor die snijplaten hebben we niet
(diameter 16mm) en dus dienden we eerst een bruikbaar werktuig te maken uitgaande
van een stelring met een 16mm binnenmaat. Levering van de ontbrekende Tremba
magneten door Conrad. Uitsnijden van de metalen bevestigingsplaten diameters
32-36 mm voor de vilten van de hoogste dempers. In deze plaatjes (voor sommige
gebruikten we grote muntstukken...) moeten we een M2.5 schroefdraad tappen.
Die tappen hebben we echter niet op voorraad... dus besteld bij Fabory. Gaatjes
(2 mm) alvast geboord op de draaibank.
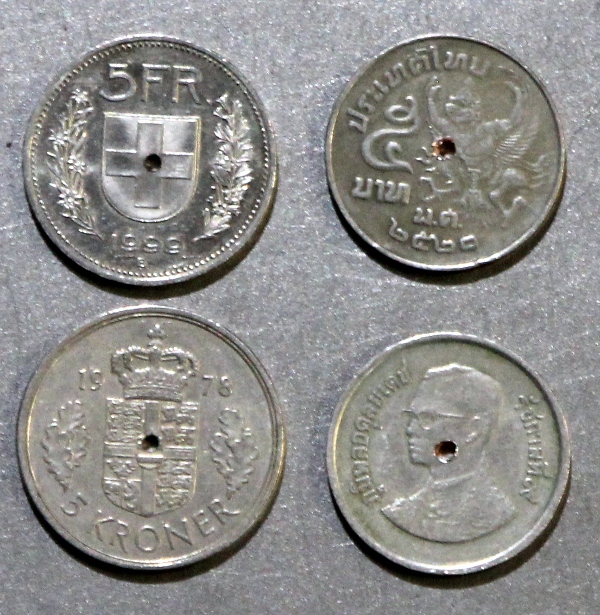
- 13.11.2019: Verwachte leveringen vandaag: Fabory (tappen) en Farnell (M2.5
moeren). Montage van de dempers 72-77, na boren van de gaten op de basisplaat.
Alle viltringen afgewerkt en met kontaktlijm vastgekleefd op de demperplaatjes
waarin we telkens een M2.5 schroefdraad tapten. Alle montagegaten voor de
demperspoelen afgetekend en geboord. Test ophanging van alle klankbuizen.
Zover staan we nu:
Onze pas gekochte M2.5 machinetap brak echter bij het maken van de vierde
schroefdraad af zodat we voorlopig vastzitten met de afwerking van de hoogste
dempers. Verstevigingsprofiel (koker, 25x25x2) aangebracht over de gehele
lengte van deze dempereenheid.
- 14.11.2019: Montage van de draadsteunen waaraan de aansluitingen van de
dempermagneten gesoldeerd moeten worden. De PCB voor de besturing kan een
plaats krijgen op de dempereenheid zelf. Haakjes voor de bevestiging daarvan
op een stuk polykarbonaat vervaardigd en gemonteerd. PCB gemonteerd. Aanbrengen
van twee blauwe LED-strips op de achterzijde van deze demper eenheid. Firmware
voor het processor board aangepast aan de drie verschillende soorten solenoids:
drie verschillende look-up tables gemaakt: Tremba, Ledex en Black Knight.
Ook meteen een beperking voorzien op het aantal toelaatbaar gelijktijdig aktieve
dempers. Wanneer dit aantal overschreden is, wordt het demp kommando automatisch
genegeerd.
- 15.11.2019: Bedrading van de demper eenheid.
- 17.11.2019: Preliminaire demonstratie van <Tubo> en het bouwproces
ervan naar aanleiding van de kinderkunstendag bij Stichting Logos.
- 18.11.2019: Wachten op de levering van de M2.5 tappen...
- 20.11.2019: Vastknopen met 1 mm dik nylon visdraad van de klankbuizen 66
tot 91, een geduldwerkje dat we toevertrouwden aan Bert Vandekerckhove.
- 22.11.2019: Nog steeds zijn de bestelde M2.5 tappen niet geleverd, waardoor
het werk nu wel wat stil ligt...
- 23.11.2019: Dan maar een alternatief voor de M2.5 schroefdraad: montage
met twee moertjes. De konstruktie van de dempereenheid wordt voortgezet.
- 24.11.2019: Konstruktie van een mechanisme om de lage demperunit te kunnen
afregelen, zo dat de dempers in lijn komen te staan met de onderkant van de
klankbuizen. Dit mechanisme bouwden we met een 50 mm lang stuk kokerprofiel
50x50x5 en een aangelast stuk plat 150 x 50 x 10, waarin we een M8 schroefdraad
tapten waarin dan weer een rubberen trillingsdemper past.
- 25.11.2019: Verder werken aan de bedrading. Spirawrap aangebracht over de
vele kabelbundels.
- 26.11.2019: Eerste tests van de beater hardware met de firmware. Bij het
aansluiten veroorzaakten we een kortsluiting, waardoor de 18F4620 chip in
rook opging... Na vervanging en herprogrammeren van een nieuwe chip werkt
een en ander redelijk goed, behalve noten 80 en 81. Daar moet een hardware
fout achter zitten. De firmware is in elk geval o.k. wat dat betreft. Lookup
tabellen in een eerste versie gemaakt. Hierbij is de scaling lineair verlopend
tussen de minimale velocity waarbij de klopper de klankbuis nog net raakt
en de maximale waarde. Hierdoor is -gezien de diversiteit van de gebruikte
magneten- het verloop van de dynamiek in elk register voorlopig nog verschillend.
Nameten pulsduren voor het 6691 board:
noot |
velo1 |
velo127 |
solenoid |
66-68 |
5 ms |
10 ms |
Kuhnke |
69-71 |
6 ms |
9 ms |
Kuhnke |
72-77 |
5 ms |
7.5 ms |
Tremba |
78-91 |
5 ms |
7.5 ms |
Tremba |
De meting werd uitgevoerd met onze Tektronix TDS2024C oscilloskoop. Bedrading
Midi-Hub board afgewerkt. Hier is de dokumentatie:
Fout
met noten 80,81 ligt niet aan de beater unit zelf, maar moet op het PCB te
situeren zijn... Gevonden! Een haarfijn koperrestantje tussen de gate-lijnen
voor de mosfets voor de noten 80 en 81 was de schuldige... Board opnieuw gemonteerd.
- 27.11.2019: Demper unit 66-91 gemonteerd en alle verbindingen (+12V, +5V
en MIDI data) afgewerkt. Eerste test: geen sluitingen. Afregeling van de afstanden
tussen dempers en onderkant klankbuizen. De montagegaten voor demper 71 zitten
te laag. Die moeten opnieuw, 5 mm hoger geboord worden. Aan de firmware (look-up
tables) is nog heel wat werk hier. Streefdoel is voor release waarde 64 een
gelijke demping te hebben voor alle klankstaven. Die waarde stemt dan overeen
met de default waarde voor controller 25. Tappen voor M2.5 schroefdraad geleverd...
weliswaar te laat nu. Zover staan we nu:
Tubo gewogen (met 4 personenweegschalen): 227 kg, heel wat meer dan we hadden
ingeschat.
- 28.11.2019: Verder werk aan de afregeling van de dempers 66-91. Montagegaten
voor demper 71 opnieuw geboord. De veren op de tremba magneten kunnen eigenlijk
beter helemaal verwijderd worden. De zwaartekracht volstaat hier ruimschoots
om de ankers te laten terugvallen. Alle veren voor de dempers 66 - 77 verwijderd.
Voor de Banggood magneten zouden we ook beter de veren verwijderen, maar daar
zijn de eindstopplaatjes op de ankers gepuntlast.
- 29.11.2019: Alle veren op de Banggood demper magneten (destruktief) verwijderd.
Testkode toegevoegd in de GMT module voor Tubo: lichtjes en individuele noten
+ dempers. Tubo gedemonstreerd voor Mutation Fest: robot in opbouw.
- 30.11.2019: Konstruktie van 18 terugvalblokjes uit middelhard schuim. Afgesneden
onder een hoek van 71.5 graden zodat we de ankers zo kunnen afregelen dat
de afstand tussen de vilten dempers en de onderkant van de klankbuizen overal
gelijk is. Na afregeling fixeerden we de blokjes met een streepje transparant
siliconenkit op het inox draagprofiel. De lage kwaliteit van de Chinese Banggood
spoelen blijft ons parten spelen: de ankers zitten te los in de spoelen waardoor
bijgeluiden kunnen ontstaan. Montage van M12 dopmoeren op de uitstekende draadstangen,
een zuiver estetische operatie.
- 01.12.2019: Testkode toegevoegd in GMT om de scalings voor de dynamiek van
de diverse registers te kunnen vergelijken en te kunnen korrigeren. De schaling
van de dynamiek gaat nu uit van objektieve meetgegevens (onze gekalibreerde
sonometer): bij een velo kommando van 32 is de geproduceerde geluidsdruk nu
76dBA. We definieren dit, in muzikale termen, als p (piano). Bij velocity
64 is de geluidsdruk nu 90dBA, in muzikale termen een f (forte). Meetvoorwaarden:
dBA meting met uitlezing van de piekwaarden, toestel opgesteld op 1m afstand
van de geluidsbron, noot-repetitie ingesteld op 2 aanslagen per sekonde, demping
vast op 64. De resonatoren bevinden zich in hun rustpositie, bij de klankbuizen,
voor maximale resonantie.
- 02.12.2019: Nog twee bruikbare inox gesloten cilinders (binnendiameter 60
mm) gevonden op de rommelmarkt gisteren. Deze zijn afkomstig van een Ikea
keukentimer. We monteerden ze meteen op de gesloten pijpresonators. Verdere
opmetingen van geluidsdrukken in dBA: opmeten pulsduren en velocities voor
102dBA (muzikaal ff). Deze geluidssterkte willen we vastleggen voor velocity
= 96. De uiteindelijke velocity kurves worden dan bepaald op grond van drie
vaste meetpunten en twee uiterste waarden. Binnen het bereik 36 tot 96 moet
de velocity scaling nu kommensurabel zijn over de gehele toonomvang van het
instrument.
- 03.12.2019: Verder werk aan de firmware voor de lage dempers (48-65). Drie
verschillende look-up tabellen, eentje voor elke reeks van zes klankbuizen,
voor de demptijden geimplementeerd. De demptijden zijn nu, bij release = 1,
34ms, bij 64 102 ms en bij 127 250 ms. De implementatie voor controller 25
verbeterden we ook substantieel. Sommige dempers voorzien van een extra laagje
kalfsleder. De bijgeluiden van de Banggood magneten blijken vooralsnog onvermijdelijk.
- 04.12.2019: Verder werk aan de firmware voor de hoge dempers (66-91). Gans
de eenheid voor de noten 66-91 losgenomen en terug op de lastafel geplaatst.
Nu kunnen we de
bedrading van de vibratomotoren afwerken en de eindmontage uitvoeren. Sensoren
vastgezet met Loctite borging. Tweede afstelbaar mechanisme gezaagd en gelast,
voorzien van een neopreen demper, voor een nog betere afstelling van de onderlijn
van de klankbuizen 48-65. Extra asborgringen aangebracht op de as van de resonatoren
66-91.
- 05.12.2019: Korrigeren van de kortsluiting aan het halogeenlampje bij de
demper van noot 65. Korrektie van de montagegaten van sommige Banggood magneten
zo dat ze in lijn komen te staan met de klankbuizen. Hiertoe maakten we een
plaat in polykarbonaat met dertig in register geboorde gaatjes voor M4 x 16
boutjes. Voor de centrale boutjes moet M4 x 10 of M4 x 12 gebruikt worden!
Twee extra blauwe
lampes (LED-spots, 12V 1W) toegevoegd, gemapt op de noten 124 en 125. Video-snippet
gemaakt van de werking van het vibrato-mechanisme en gepost op Facebook.
- 06.12.2019: Tubo weer helemaal geassembleerd met de hulp van Bert en Lara.
M12 inox dopmoeren aangebracht op de uitstekende M12 draadstangen. Midi-hub
firmware opnieuw geprogrammeerd, er zat nog een bug in de implementatie van
de lampjes. Verdere afregeling van de dempers, die nog veel teveel bijgeluiden
veroorzaken. Nieuwe 45mm afstandsbus (hoogte 30 mm) gedraaid uit PVC voor
de hoge dempereenheid. Me fecit gegraveerd naamplaatje aangebracht...
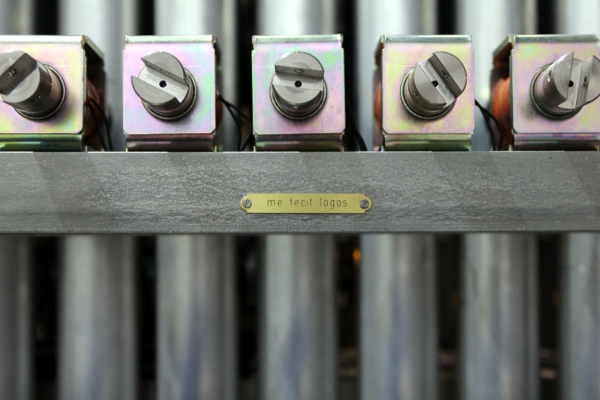
- 07.12.2019: Verdere afregeling dempers met vilt en/of zacht kalfsleder.
Test van de implementatie voor controller #25, vanuit GMT: dit blijkt perfekt
te werken. De lookup tabellen voor de dempers met de Lucas-Ledex magneten
moeten aangepast worden. Enkele dempermagneten vertonen enige scheefstand,
wat moet gekorrigeerd worden.
- 08.12.2019: Nieuwe firmware voor dempers 6691 geschreven en geprogrammeerd.
Onderzoek naar de oorsprong van het voorkomen van onregelmatigheden in de
pulslengtes: met tussenpozen van ongeveer 30 sekonden zijn er af en toe pulsen
te observeren op de skoop die veel korter zijn dan de ingestelde waarde. De
opgewekte pulsen overschrijden nooit de ingestelde duur. Oplossing gevonden:
in de interrupt handler voor timer0, moet Cnt.Word0 = TMR0.Word gesteld worden.
Na deze ingreep waren alle onregelmatigheden verdwenen. Alle boards voor kloppers
en dempers opnieuw geprogrammeerd. Op de rommelmarkt nog een inox thermosfles
gekocht, waaruit twee gesloten cilinders, binnenmaat 60 mm, te distileren
vielen. Nog drie inox potjes ontbreken we nu om alle gesloten pijpresonatoren
af te werken.
- 09.12.2019: Inox potje aangetroffen in de keuken, en meteen gemonteerd...
Nu nog twee potjes tekort. Enkele portretfoto's gemaakt van <Tubo>.
Begin werk aan een demo-kompositie van Tubo.
- 10.12.2019: Implementatie van allnotesoff kommando gewijzigd, zo dat klinkende
noten toch gedempt worden bij ontvangst van dit kommando. Begrenzing ingevoerd
voor het maximaal aantal toelaatbare gelijktijdig aktieve dempers. Voor de
noten 48 tot 65 is deze grens bepaald op 10, voor de noten 66-91 op 12. Wanneer
dit aantal wordt overschreden word het demp-kommando genegeerd en zal de noot
dus blijven klinken. Verder werk aan een eerste demo-kompositie voor <Tubo>.
- 19.12.2019: Avant-premiere van 'Eindjes' voor <Tubo>, met performance
door Emilie De Vlam. Premiere van een nieuw stuk voor de tubo robot van Kristof
Lauwers.
- 20.12.2019: <Tubo> heeft zijn vuurdoop goed overleefd. Op nu naar
verdere perfektionering en de derde en laatste bouwfaze die de robot ook zelfstandig
interaktief moet maken.
- 17.01.2020: Ophanging van de klankbuizen 48 - 53 verbeterd door iets dunner
nylon draad te gebruiken en ook de viltjes wat dunner te nemen. De galmtijd
van deze buizen is nu aanmerkelijk beter.
- 22.01.2020: Dezelfde verbeteringen aangebracht voor alle buizen aan de lage
kant van de robot. Dit geduld-werk werd uitgevoerd door Bert Vandekerkhove.
- 01.10.2020: <Tubo> gaat voor de eerste keer op reis: op naar Keulen
voor een koproduktie met Sebastian Gramms.
- 03.10.2020: <Tubo> heeft de reis naar Keulen goed overleefd.
- 07.12.2020: Bug ontdekt in de firmware voor de DC motoren (24EP128MC202
processors). Timer 2/3 werd foutief gelezen. Fout hersteld in de kode. Moet
wel nog naar Tubo ge-upload worden nu.
- 22.08.2021: Overweging om <Tubo> ook op te stellen in het SMAK. Daarom
begin met het programmeren van een radar-board met gesture analyse kode voor
de automatische interaktieve bestepeling van Tubo. Radar_4 board, gebouwd
in 2017, was nog vrij voor dit doel. De kode kan nauw aansluiten bij die gemaakt
voor <Aeio>.
- 23.08.2021: Kode verder uitgewerkt en getest. Opbouw op een polykarbonaatdrager
afgewerkt zodat de radar op een microfoonstatief met 3/8" schroefdraad
gemonteerd kan worden.
- 24.08.2021: Uitvoerige tests in opstelling met tubo en flex. Hier is een
foto van de radar module:

- 25.08.2021: Konstruktie van een inox montagebeugel voor de radar-module
op de <Tubo> robot. Een enkele M12 bout volstaat om de module te monteren/demonteren.
Een goede oplossing voor het wegwerken van de bedrading moeten we nu nog zien
te vinden.
- 02.09.2021 - 30.09.2021: <Tubo> interaktief in werking in het Gentse
SMAK museum.
- 14.09.2023: <Tubo> gaat mee op reis naar de Deutsche Oper Berlin.
- 16.09.2023: Bij aankomst in Berlijn blijken de nylon ophangtouwtjes van
een zestal buizen losgekomen te zijn. De herstelling werd terplaatse uitgevoerd
met een lage Mi gitaarsnaar...
- 02.10.2023: <Tubo> komt terug aan in Gent, zonder noemenswaardige
schade, al zijn er wel wat flinke krassen op het aluminium buizenwerk bijgekomen.
Wellicht door onoordeelkundig vastmaken met singels. Een definitieve herstelling
van de ophanging is nog uit te voeren.
Todo:
- Betere (mechanisch stillere...) motoren zoeken voor de aandrijving het met
vibrato mechanisme, vooral voor de motor die het hoge noten mechanisme stuurt
is dit belangrijk.
- Verbeteren van de bijgeluiden bij de dempers
- Vervangen halogeen lampvoetje bij klankbuis 65.
- Vaste montage van het radar interface board en verbetering van de kode voor
meer algemeen interaktief gebruik.
Afmetingen & andere technische specifikaties:
- hoogte: 1935 mm
- breedte: 1272 mm
- diepte: 620 mm
- gewicht: 228 kg
- ambitus:48 - 91
- maximale geluidsdruk: > 102dBA
- elektrische aansluiting: 230V ac - 500 VA
- data-poort: MIDI port.
- midi channel: 4
- Verzekeringswaarde (produktiekost): 56.000 Euro
Belangrijke nota voor gebruikers:
- De robot moet zuiver waterpas opgesteld worden, zoniet worden de aanslagen
minder betrouwbaar en ontstaan er allerlei onbedoelde bijgeluiden.
Design en konstruktie: dr.Godfried-Willem
Raes
verdere medewerkers:
- Lara Van Wynsberghe
- Peter De Vlaeminck (Polo bvba)
- Peter Van Lancker
- Moniek Darge
- Bert Vandekerkhove (assemblage)
- Mattias Parent
- Emilie De Vlam
- Laura Maes
- Philippe Druez
Firmware:
Compiler: Proton+ (Proton8, version 3.7.3.1 and Proton24, version 1.0.6.4),
nu, 2022: Positron compiler.
Programmer: MPLAB-IPE with Pickit3 (Microchip)
Test en evaluatiekode: (Power Basic compiler)
- gekompileerde versie (exe file): slagwerk.exe
(GMT)
- source code voor de <Tubo> robot:
tubo.inc (GMT)
Bibliography, references and datasheets:
- Kuhnke Magnet catalog
- Nijgh Versluys 'Verspanen Kernboek 1', Baarn Nederland, 1999.
- Raes, Godfried-Willem 'Logos @ 50, het kloppend hart van de avant-garde
muziek in Vlaanderen', ed. Stichting Kunstboek, Oostkamp, 2018
Onderdelen specifikaties en bron:
Witte LED strip: 12V (Farnell)
Blauwe LED strips: 12V OMC part.nr.1226696 www.omc-uk.com
Kuhnke magneten voor noten 48 tot 65: HD8286-R-F (Distrelec), 24V - 16W, Rdc=36
Ohm.
Halogeenlampjes: Osram 12V 35W GY6.35 socket. (Conrad) (18 stuks)
Linear, LT1084-12 datasheet
Dunkermotoren BG40x50
Epcos MOV dataheet
Linear power supply 12V - 25A, PCB ontwerp
@ 200%
Beater VDR's: Philips type 2322 592 1512. ac 150Vrms, dc 200V, Iph 400A (8us),
Varistor voltage 216-264V @ 1mA, clamping voltage @50A: 470V, 90pF
International Rectifier (IOR) , Mosfet IRLZ34N
(mosfets op de demperboards)
Mosfet IRL640 (mosfets op de beaterboards)
Microchip manual for 18F2620 and
18F4620
MUR620C datasheet (terugslagdiodes op de beaterboards)
Crouzet motor datasheet (RS-Components)
Omron Proximity sensor E2A-M12KS04-WPC12M
(Farnell , order nr. 1603084)
Tapmaten versus boorgaten: tabel
Onderhoud en (de)montage instrukties:
Algemene voorwaarden:
- De <Tubo> robot mag niet langdurig worden blootgesteld aan ultraviolet
licht. Dit tast immers de uit PVC vervaardigde onderdelen aan.
- Ook voor vochtigheid moet de robot worden beschermd. Vocht veroorzaakt immers
korrosie op de elektronische komponenten evenals op de aluminium buizen.
- De robot dient bewaard en opgeslagen te worden bij een temperatuur tussen
14 en 28 graden.
<Tubo> is opgebouwd uit verschillende modules die kunnen worden losgenomen:
1.- Beater unit voor de noten 48 tot 65: frontaal vastgezet met 4 M12 bouten.
Vooraleer de module los te maken moet de 30-polige konnektor worden losgemaakt.
2.- Demper unit voor de noten 48 tot 65: frontaal vastgezet met M12 bouten.
Vooraleer de module los te maken moeten de Weidmueller konnektors op het demper
4865 PCB losgemaakt worden.
3.- Resonator unit voor de noten 48 tot 65: om die module los te nemen moet
de lange as (12 mm diameter) volledig uitgetrokken worden aan de kant van noot
65. Om de as te kunnen uitschuiven boorden we een gaatje ter hoogte van het
draaipunt aan de kant van noot 48. De stelringen moeten worden losgeschroefd
om de as te kunnen verwijderen.
4.- Resonator unit voor de noten 66 tot 91: los te nemen na verwijdering van
de lange as (10 mm diameter). De stelringen moeten worden losgeschroefd (inbus
sleuteltje gebruiken) om de as te kunnen verwijderen.
5.- Klankbuizen unit voor de noten 66 tot 91: Met bouten vastgeschroefd op
het hoofdchassis. De vibrato motor met excentriek evenals de sensor, bevinden
zich vast gemonteerd op deze module.
6.- Beater unit voor de noten 66 tot 91: frontaal vastgezet met M12 bouten.
Zijdelings verstelbaar met vier M10 bouten. Om deze unit los te nemen moeten
de konnektor aan de kabelboom van de PCB worden losgenomen. Vooraleer deze eenheid
los te nemen, moeten de elko's van de voeding ontladen worden!
7.- Demper unit voor de noten 66 tot 91: frontaal vastgezet met vier M8 bouten
en moeten aan de binnenzijde van de 100x100x5x50 kokerprofielen.Om deze unit
los te nemen moet de 12V (rood zwarte draad) verbinding op het aansluitblokje
van de basisplaat worden losgenomen. Verder moet ook de driepolige Weidmueller
konnektor met de ene groene draad naar het midi-hub board en de midi/5V aansluiting
zelf losgemaakt worden.
8.- Besturingsunit 1: Power supply en midihub board. Vanhieruit vertrekken
alle bedradingen voor de andere boards. Het midi-hub board is moeilijk toegankelijk:
om het te bereiken kan best de 12V SMPS voedingsmodule worden losgenomen van
de ronde basisplaat. Deze module bevat ook de beater- en demperbesturingsboard
voor de noten 48 tot 65.
Onderdelen die enig onderhoud kunnen vergen zijn in eerste plaats de viltjes
op de kogels van de kloppers. De viltschijven op de dempers kunnen onderhevig
zijn aan motten, al zijn ze daartegen behandeld. Die behandeling moet zeker
om de vijf jaar opnieuw uitgevoerd worden. De resonators zijn in principe stabiel
gestemd, maar -indien de hulzen (moffen) op hun bovenkant zouden verschuiven-
kunnen ze, indien niet vastgelijmd, worden bijgestemd. De stemming van de klankbuizen
is voor vijftig jaar gegarandeerd stabiel. Wanneer piepgeluiden hoorbaar zijn
bij geaktiveerd vibratomechanisme, moeten de draaipunten van de lange assen
waarop de resonators kunnen draaien, van een druppeltje smeerolie of wat wagenvet
worden voorzien.
Belangrijk: vooraleer welkdanig ook onderzoek en demontage van deze
robot te ondernemen, moeten de elco's voor de 100V voeding volledig ontladen
worden. Gebruik daarvoor een weerstand van 47 Ohm (1W volstaat). De 100V spanning
blijft immers nog dagen na gewone uitschakeling over deze vier elco's behouden
en -hoewel niet letaal- kunnen ze wel een flinke elektrische schok veroorzaken.
Debug informatie m.b.t. de motor-besturingsboards:
Betekenis van de LED's op het board:
- blauwe LED: licht op wanneer de motor vertraagt tot de sensor deze uitschakelt.
Dus alleen na een vibrato off commando. Wanneer de blauwe LED aan blijft,
is er iets mis met de positionering van de sensor. Deze genereert immers de
interrupt die de motor moet uitschakelen. Merk op dat ook de sensor een ingebouwde
gele LED heeft, die moet oplichten wanneer de eindpositie is bereikt. Wanneer
dit werkt en de blauwe LED toch niet dooft is er ofwel iets fout met de bedrading
ofwel iets in de firmware.
- groene LED: licht op wanneer het power-on kommando ontvangen wordt. (Controller
66). Bij ontvangst van het power-on kommando, wordt steeds een korte kallibratie
routine uitgevoerd waarna de motoren worden uitgeschakeld.
- gele LED: monitor voor de vibrato motor. Lichtje is aan wanneer de motor
bekrachtigd is.
- oranje LED: licht op wanneer de motor accelereert tot de gewenste waarde
is bereikt.
- rode LED: knippert ca. tweemaal per sekonde zolang de microprocessor aktief
is.
Enkele midi controllers werden geimplementeerd voor research doeleinden. Het
is niet de bedoeling dat ze bij normaal gebruik worden verstuurd:
- Controller 40: stuurt de 7 low bits van het 14 bits woord dat de PWM sturing
van de lage vibratormotor bepaalt. Controller 20 bepaalt alleen de hoogste
7 bits. De controller werkt alleen als de motor draait en gebeurlijk aktieve
ramping is afgewerkt.
- Controller 41: doet hetzelfde voor de hoge vibratormotor. Controller 21
bepaalt ook hier alleen de hoogste 7 bits. Zelfde konditie als hiervoor.
Tentatieve kostprijsberekening:
Aluminium buizen (Demar-Lux) |
200 kg |
|
|
1200.00
|
Kuhnke magneten HD8286-R-F (Distrelec)
[beaters 48-65] |
18 |
|
|
4134.00
|
Kuhnke magneten H6286-R-F (Distrelec)
[beaters 66-71] |
6 |
|
96,- |
576.00
|
Blauwe magneten (Laukhuff) |
25 |
75,- |
niet gebruikt |
|
Tubular solenoids
Tremba ZMF-3865d-15.002 - 24V (Conrad)
|
50 |
64,- |
|
3200.00
|
Tremba ZMF-3258d.002 - 12V (Conrad) F9545173455 [dempers 66-77] |
28 |
33.73- |
|
944.57
|
Banggood magneten 12V - 1.5 Ohm (Banggood)[dempers
48-65] |
25 |
17.33- |
|
433.25
|
Banggood magneten JF-0539B 12V - small - ongeschikt bevonden |
36 |
4.50- |
niet gebruikt |
162.00
|
Banggood 12V - 2A, 10mm 20N 25x25x22mm JF-0826B1 |
|
5.35 |
niet gebruikt |
140,31
|
Banggood 12V -500mA |
|
7.53 |
niet gebruikt |
|
Lucas-Ledex 12V push solenoids |
4 |
|
|
|
Black Knight 12V push solenoids |
10 |
|
|
|
Inox (Demar-Lux), ca. 140 kg |
|
3.50 |
|
490.00
|
Wielen en lagers (De Coene) |
|
|
|
500.00
|
PVC (resonatoren) (Eriks, Audenaert) |
|
|
|
500.00
|
Vilt en rubber (De Mulder) |
|
|
|
300.00
|
Hasberg reflektor |
|
|
niet gebruikt |
100.00
|
Hub PCB |
1 |
|
|
500.00
|
Mosfet driver PCB's |
4 |
500,- |
|
2000.00
|
LT1084-12 regulators (Farnell) |
5 |
|
|
98.25
|
EREA tranformator 300VA 12V |
1 |
|
|
350.00
|
Toroidal 2 x 35V 350VA (Farnell) |
1 |
|
|
400.00
|
SMPS 12V 12.5A - XP Power (Farnell) |
1 |
|
|
180.00
|
70HFLR20S01 diodes (4) (RS-Components) |
4 |
14,25- |
|
57.00
|
Lasercutting van de viltschijven (Polo) |
|
|
|
50.00
|
Kogelknoppen M8, 40, 36, 32, 25 mm (Fabory) |
|
|
|
|
Kogelknoppen M4 20, 16 mm (Fabory) |
|
|
|
|
Kogelknoppen M6, 25 mm (Fabory) |
|
|
|
|
Lasgassen en elektroden (Air Liquide) |
|
|
|
270.00
|
aluminium plaatmateriaal en profielen (Demar-Lux) |
|
|
|
|
Varistors 150V ac Philips 2322 592 1512 (old stock) |
|
|
|
27.00
|
MOV's 14Vac Epcos B72210S0140K101 (Farnell) |
|
|
|
|
Holpijpen (Decoene) |
|
|
|
215.00
|
Dunkermotor BG40X50 + PLG42S 24V / 2.1A |
1 |
|
niet gebruikt |
|
Crouzet Motor 80835004 (24V-147rpm)
(RS Components) |
1 |
|
|
297.00
|
Micromotor McLennan E192-24-25, 166
rpm 24V, 21W 90Ncm (Farnell) |
1 |
|
|
92.72
|
Shock absorbers M6 - MF (Farnell / Fabory) |
6 |
|
|
|
PTFE staff material (MEA), 16 mm diameter |
|
|
|
|
PTFE plate material, 3.5mm thickness |
|
|
|
|
Omron sensors E2AM12KS04WPC12M (Farnell) |
2 |
36.00 |
|
72.00
|
Motor control PCB's |
2 |
280.00 |
|
560.00
|
Schroefdraadadaptors M4 int, M6 ext. Thorlabs AE4M6M |
30 |
|
|
169.84
|
Stelringen 20x32x16, inox (MEA) |
14 |
|
|
|
Kobalt boren (Decoene-Simons) |
|
|
|
160.00
|
Stelringen 12 mm (Fabory) |
|
|
|
|
Epramid , 40 mm staff material |
|
|
|
|
Dun wit vilt (Veritas) |
|
|
|
|
Blauwe 1W multi-LED spotlights, 12V (Conrad) |
2 |
|
|
12.00
|
Nylon draad voor buisophanging, 1 mm (Brico) |
50m |
|
|
7.49
|
Nylon draad 1.2mm (Discount Office) + tekenstiftjes |
25m |
|
|
37.08
|
Radar_4 board (2021) |
1 |
|
|
1000.00
|
geschat totaal: 20.000 Euro [nu 19178.94]
Arbeid:
geschat op 9 maand FT. (ca. 37.500 Euro)
Last update: 2023-10-11
by Godfried-Willem Raes