Microtonal
Musical Robot
Research project on
the development of new tools for musical expression at the University
College Ghent
|
<Horny>
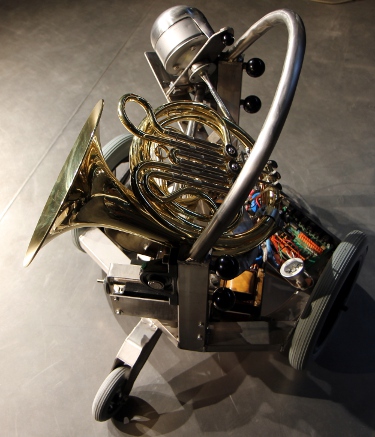
an automated french horn
Godfried-Willem
RAES
2013
|
The design and construction of this automated instrument started with the purchase
of a brand new F-horn, made by Arnolds & Sons, model nr. AHR-301, serial
number 121267. It came with an extra short piece of tubing, such that it can
be turned into a Bb horn as well.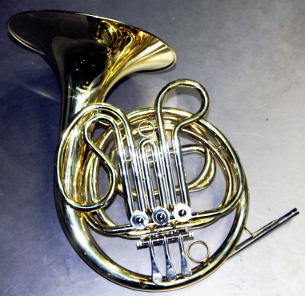
The horn has three rotary valves and force measurement revealed that the minimum
force required to start movement of the valves was 2 Newtons. The required movement
trajectory is 12 mm and the force required to fully push the valves raises to
2.5 Newtons. This determines the specification of the solenoid valves to be
used. The physical placement of the valves on the instrument however, dictates
a few more restrictions: the distances between the activation points of the
valves are 30mm and 20mm, so the use of standard Lucas Ledex tubular solenoids
(diameter 1" (25.4mm)) capable of meeting the specifications becomes problematic.
Hence we went for August Laukhuff register magnets with a pivoting action and
a force of 10 Newton.. The mounting width of these type is only 18mm. The solenoids
are connected in series with a 24V halogen bulb (10W), operating as a voltage
dependent resistor.
As we power the solenoids from 48V, we now doubled the force developed at the
start of the trajectory. The starting force of these solenoids, even after carefull
adjustment of the anchor and the trajectory is only marginally large enough
otherwize. The solenoids are mechanically coupled to the valves using tractures
made of flexible M4 threaded nylon rod. Nuts and felt washers were used to minimalize
mechanical noise production. The operation of the valves is controlled by a
Microchip PIC controller type 18F2525. There are selectable lookup tables for
both the fingering on the F-horn and the Bb horn.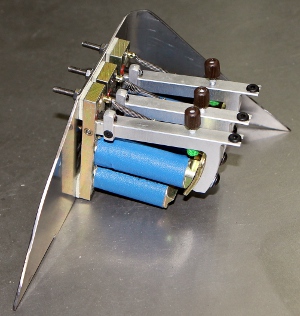
For the excitation of the horn we once again used a compression driver followed
with an acoustic impedance convertor. In this case we used the original mouthpiece
of the horn without any modification other than the construction of a new clamping
system to connect the mouthpiece firmly with the driver. The compression driver
is steered -after amplification- by an ARM-microprocessor.
Horns are normally played with the bell pointing backwards. On occasions, composers
do ask for the bell to be brought 'cor en haut', pointing to the audience. This
request can for instance be found in the score of Strawinsky's 'Le Sacre du
Printemps'. In our robot we also wanted to implement some form of control over
the sound projection from the instrument. Since the mounting of the horn appeared
to be quite complicated it was not possible to perform all calculations and
drawings beforehand since for fluent motion it is mandatory to know the axis
of equilibrium. Therefore we started by making the essential holding structure
including the valve solenoids and the compression driver and only after that
job was finished, we empirically found out where to place the balancing point.
Unfortunately this balancing point appeared to come too close to the compression
driver. Thus for technical reasons such as accessibility of mounting bolts and
nuts and for ease of disassembly, we did move the axis of movement slightly
to the backpoint. To restore equilibrium we sufficed by adding some extra weight.
A stainless steel ladle at the same time serving as a protection cap for the
compression driver fullfilled this function very well. As it came out, the final
result is a bit crab like as the wheels had to be placed under a weird angle
to the instrument.
Very probably this robotic horn is the very first horn player in music history
that ever succeeded in playing his musical parts always perfectly in tune. Users
and composers that like the 'out of tune-ness' of real hornplayers can always
implement this as we gave the instrument ample possibilities to play in just
about any imaginable tone system with high precision.
Power supply voltages and currents:
- + 48V, 1.5A dc for the valve solenoids (with 100% duty cycle)
- +24V, 2.5 A for the bidirectional movement solenoid (PWM controlled).
- bipolar -25 - + 25 V , 0.8 A for the compression motor driver
- +12V, 1A for the lights
- + 5 V/ 500 mA for the two processor boards and the logic. The 3V power for
the ARM chip is generated on board, derived from the +5V supply.
Midi Mapping and implementation:
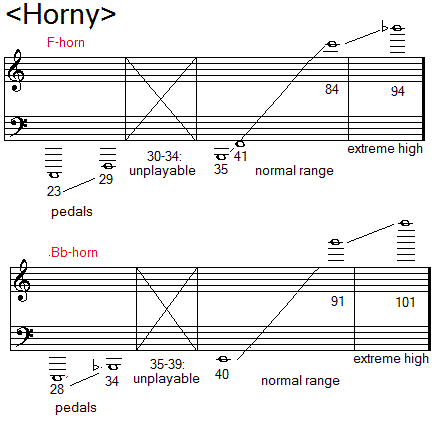
Midi channel : 14 (counting 0-15).
Midi note range: (23-29), 35-94 if used as an F-horn with the appropriate crook
and controller setting. Note on, with velocity is implemented and has a wide
control range. The external input may be mapped onto the note range 110-119
(way above the normal ambitus and the extended range) This implements vocal/instrumental
multiphonic playing. Note that the range 30 to 34 is only available when the
Bb tube is inserted and the appropriate controller (#33) is send..
Note Off commands are required, but can be dropped for pure legato playing.
A note-off releases the valves and unpowers them. It starts the fast decay section
of the mouth driver according to the parameter set with controller #19. The
note release byte, if not 0, can be used for what it's standard function is
for. If used, it will override the setting of controller #19.
Controllers:
Controller 1: Wind controller, steers the amount of noise in the sound. Default
= x. Advised setting: 20
Controller 2: LFO3 frequency applied to the filter. Default = x. Advised setting:
2
Controller 3: Vibrato depth (LFO1 amplitude). Default = x. Advised setting:
20, to turn vibrato off, set this controller to 0.
Controller 4: Vibrato speed. (LFO1 frequency). Default = x. Advised setting:
5
Controller 5: Tremolo depth, amplitude modulation. (LFO2). Default = 0
Controller 6: Tremolo speed. (LFO2 frequency). Default = 0. Advised setting:
16
Controller 7: Global volume control. Can be used for crescendo and decrescendo
effects whilst notes are sounding. This also affects the sound color of the
instrument, as normal for horns. Default = 80
Controller 16: Note attack speed controller (0= slow attack, 127= fast attack)
. Default setting: 100. Advised setting: 25
Controller 17 is used to control the maximum sound level reached after the attack
time. This controller is always larger than or equal to the level set by the
velocity byte. For sfz or staccato playing, this controller must be set to high
levels and the velocity byte kept rather low. Default setting: 127. Advised
setting: 0
Controller 18 is used to control the speed of the transition between the attack
level once reached and the sustain or hold value set by the velocity byte.(0=
slow transition, 127= fast transition) default setting: x. Advised setting 50
Controller 19: is used to control the release time after reception of a note
off. Here again a value of 0 will give a slow release whereas a value of 127
will give a very fast release. Note that with very low values, the note may
not even turn off completely. Default setting: 96. Advised setting: 65. Note
that if real note-off commands are used, the release value sent with them, if
this value is not zero, will override controller 19, such that the value of
controller 19 will be set to 128-release value.
The following graph gives a picture of the mutual dependencies of all these
controllers. Note that the implementation is different than what we have implemented
in monophonic instruments build prior to <Fa>, <Asa> and <Klar>!
Controller 20: Basic tuning of the instrument. The range is + or - a semitone.(Defaults
to value 64 for A=440Hz)
Controller 21: minimum solenoid power PWM controller (for
development only) (default = 64)
Controller 22: Vertical inclination controller. (0-63= downwards, 64=central,
unpowered, 65-127= upwards). (default = 64)
Controller 25: Filter cut off frequency. Default = 62. Advised setting: 49
Controller 26: Filter resonance amount. Default = 90. Advised setting: 120
Controller 27: Echo mix. Default = 0. Advised setting: 2. Only use this for
experimental sounds, as it can generate multiphonics.
Controller 28: echo feedback. Default = 0. Only use this for experimental sounds,
as it can generate multiphonics.
Controller 29: LFO3, filter depth. Default = 20. Advised setting: 20. (large
values give a wha-wha effect)
Controller 30: Valve release time out after note-off's.
Controller 33: F-horn or Bb horn selector. (0= F-horn, 127 = Bb-Horn). On cold
boot the firmware will always assume F-horn. The setting of this controller
obviously changes the lookup table for the fingerings.
Controller 40: Bendrange for the pitchbend. 0= no bending, 1=+/- 50 cents. Default
= 1.
Controller 43: Wait time for vibrato start after
reception of a note-on command. Note that in legato playing, vibrato will continue.
The wait time starts again after a note off is received. Default = 100. Advised
setting 8.
Controller 44: Wait time for the tremolo (AM modulation) to start after a note-on
command. Default = 10. Advised setting: 3
Controller 66: Power on/off switch (0 = off, any other value is on). Power off,
resets all controllers to their cold-boot values.
Controller 100: Can be used to override the fingering used in the lookup tables.
Only the three lowest bits of the value are used. Bit 0 corresponds to the 1/2-tone
valve (the middle valve, named valve 1), Bit 1 to the 1-tone valve (the valve
closest to the mouthpiece, named valve 2), bit 2 to the 1 1/2-tone valve (named
valve 3). This controller can be sent any time, even when no note is sounded.
If you want a note to be played with a fingering different from the fingering
in the default lookup table, you have to send this controller right after the
note on command.
Controller 123: switches the sounding note off, unpowers the movement solenoid,
dims all the lights. Does not reset any controllers.
Program change: not implemented so far. May be used later
for interactive robotic modes of functioning, exploiting the audio input possibilities
on the ARM-board.
Lights: The lights are mapped on very high midi-notes as follows:
- note 120: Yellow LED spotlight on the back side
- note 121: Yellow LED spotlight on the front side
- note 122: Festoon tungsten lights on the front (2x24V/5W)
With velocity values between 1 and 126, the lights will be flashing with speeds
proportional to the velocity value. To switch them just on, use velo = 127.
Velo=0 switches them off.
Pitch bend: implemented with a range of a semitone (a quartertone up or down).
The coding for a fragment of a quartertone scale (here shown for the <Heli>
robot, but its identical for <Horny>) is as follows:
Most good sequencer
software (such as Cakewalk or Sonar) use the signed 14 bit format. Note that
one unit of the msb corresponds exactly to a 0.78 cent interval. To convert
fractional midi to the msb only pitchbend to apply, follow following procedure:
if the fractional part is <= 0.5 then msb= 63 + (FRAC(note) * 128), if the
fractional part is larger than 0.5, we should switch on the note + 1 and lower
the pitch with msb= (1-FRAC(note)) * 128.
Note that the pitch bend range on <Horny> can be modified with controller
40. By default this controller sets the range to plus or minus a quartertone.
By setting this controller to higher values, large continuous glissandi become
possible. Setting this controller to zero disables pitch bending.
Classified by function, we have the following groups of controllers:
- Note Off, with release byte implemented, CC30
- Note On: ADSR: CC16,17,18,19, velocity byte
- Tuning related controllers: CC20, pitchbend, CC33, CC40
- Vibrato: CC3, CC4, CC43
- Tremolo: CC5, CC6, CC44 (can also be used to implement Flatterzunge effects)
- Sound color: CC2, CC25, CC26, CC29
- Position: CC22
- Fingering: CC100
Technical specifications:
- size: base: 650 x 650 mm. height: 700mm
- weight: 35kg
- transportation: requires flight case.
- Power: 230 V ac / 130 W
- data input: Midi and/or UDP/IP over Ethernet.
- Tuning: based on A = 440 Hz (within 1%). The tuning can be adjusted.
- Ambitus: F-Horn: 35-86, Bb-Horn: 40- 91 (make sure to insert the appropriate
crook!)
- External audio input: 0dB line level, 1/4" jack input.
- Insurance value: 12.500 Euro
Design and construction: dr.Godfried-Willem
Raes
Collaborators on the construction of this robot:
- Kristof Lauwers (GMT-player implementation & lookup tables)
- Sebastian Bradt (requisites and research)
- Blazers & Blazers (Horn supply)
- Hans Denayer (Horn advice, fingering data)
- Johannes Taelman (ARM firmware coding)
Music composed for <Horny>:
- <Horny> was introduced in the robot orchestra together with <Asa>.
They play important parts in the 'Namuda 3' production premiered 23,24,25th
of july.
- <Horny> was presented at the Brussels BEAF festival, september 2013
with radar controlled interactive compositions by Kristof Lauwers.
Pictures taken during the construction:
Valve solenoids:
Finished horn holding
part, with provisions for horizontal movement:
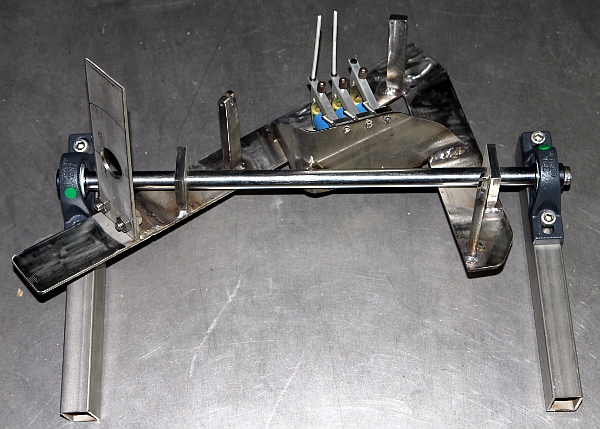
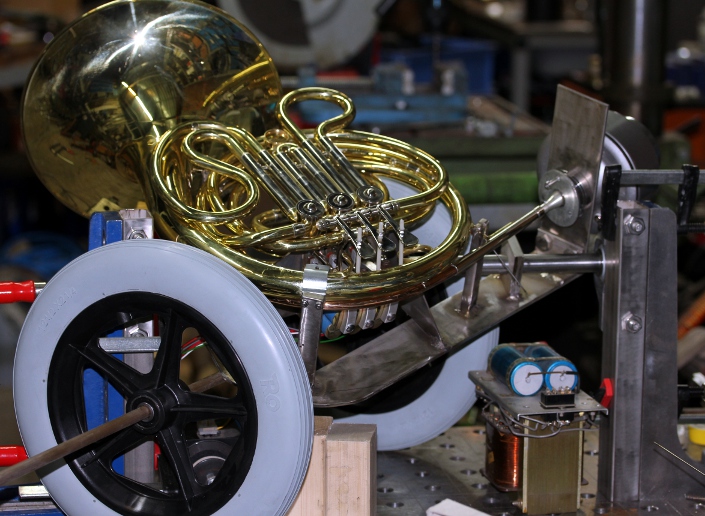
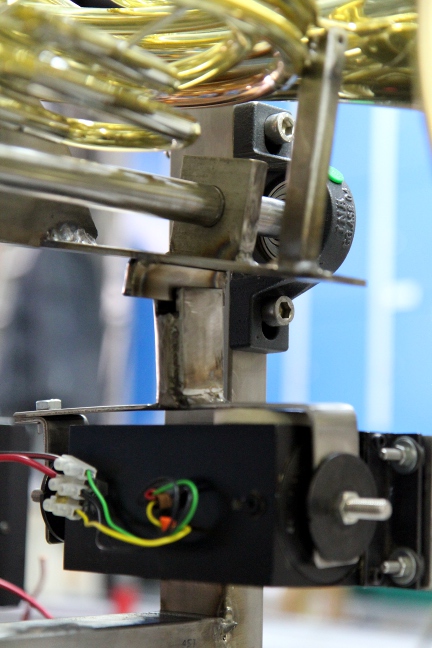

and
some views on the finished robot:
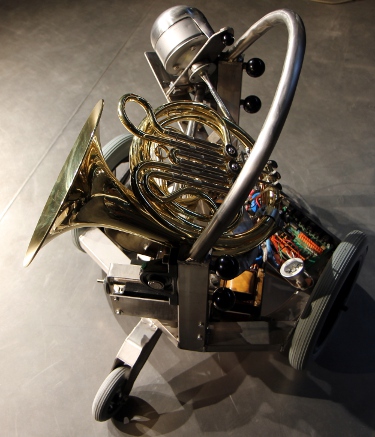
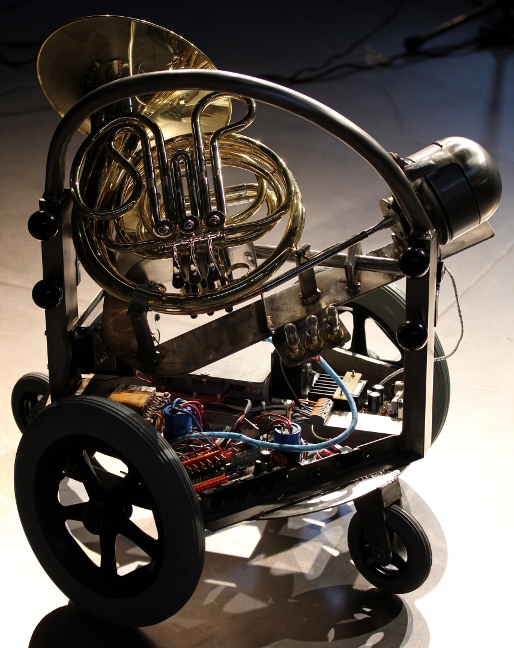
Nederlands:
Robot: <Horny>
Een nederlandse beschrijving is voorlopig nog niet beschikbaar.
Construction Diary:
- 27.03.2013: First sketches and designs. Hunting for a decent french horn
has started...
- 29.03.2013: First provisions made in GMT in order to implement test code
for <Horny>, Resources recompiled and extended.
- 03.04.2013: New connectors made by IMO came in from Farnell. These should
replace the Weidmueller parts we have used sofar. A note
on the connectors used in our robots added to the Logos site.
- 08.04.2013: Got some offers and prices for decent horns... Sebastian Bradt
was the hunter on duty.
- 10.04.2013: F-horn ordered. Delivery will take about two weeks.
- 20.04.2013: The ordered horn came flowing in from Arnold Stoelzel Gmbh...
Cheaper than we thought at first: about 500 Euro's. We can start the design
works.
- 21.04.2013: Measurement of the required trajectory and force to activate
the valves. Looks like Lucas Ledex tubular solenoids, as used in our player
piano design, may work well here, if we can live with a pretty horizontal
design. Should we implement the functionality of the players right hand in
the bell as well? Should we implement movement?
- 23.04.2013: Further drawing and design work. Finding a good tree-point mounting
system for the horn does not look like a trivial undertaking since the instrument
has tubes all over its circumference making it difficult to use clamps.
- 24.04.2013: Start construction of a solenoid test-assembly with tubular
solenoids to activate the valves. First attempts to make mounting brackets
for the instrument.
Valve automation could also be done with Laukhuff pull down magnets (type
300800), having a traject of 10mm at a force of 10 Newton. (12V types have
R=13.5 Ohm and draw 900mA current). These are by design a lot more silent
in operation than the tubular solenoids. Another advantage is the fact that
they have a rotary motion, more or less corresponding to the rotary traject
the valves have to make. Thus unavoidable friction resulting from the use
of tubular solenoids with inherent linear motion can be avoided. On the negative
side however comes the fact that these Laukhuff solenoids are a bit sluggish.
On
the picture we see clearly the mount for the compression driver and the mouthpiece
clamp. The driver can be taken away after loosening the two M10 bolts.
- 25.04.2013: Laukhuff solenoid assembly finished and welded in place, slightly
tilted.
These solenoids
consist of two coils connected in series, the shortest one has a DC resistance
of 25 Ohms and the larger coil, 32 Ohms. So when operated at their nominal
voltage of 24V, the shortest coil has 10.5V over it, the larger one 13.4V.
Design of the power supplies. Determination of a suitable horizontal balancing
point required to implement movement. Holes drilled in the valve-fingerplates
of the horn. Tractures made from M4 threaded nylon rod. Felt washers will
be required here.
- 26.04.2013: Upper part of chassis fully TIG welded. The pivoting mechanism
uses a 20mm axle and two ball bearings. The bearing holders are made in cast
iron and can be taken of by loosening the M10 bolts that hold them in place.
- 27.04.2013: Electric tests of the valve mechanism. Design of the wheel base.
First tentative assembly on the welding table. The mechanism for the valves
works but needs fine adjustment for traject and force. The starting force
excerted by the solenoids is only marginally large enough to move the valves.
We performed the test with an applied voltage of 30V, so we may have to go
as high as 48V. The circuit using series bulbs agains comes into sight. We
will try it out with 24V/10W halogen bulbs.
If this simple solution is not workable, we will have to use the pulse-hold
boards and a dual voltage power supply. Halogen bulbs rated for 24V ordered
from Conrad and from Farnell. Their sockets (BA15s) still pose a problem as
they are very hard to find on the market. Furthermore they have one pole connected
to ground - a usual practice in cars and trucks-, making a complicated mechanical
structure mandatory.
- 28.04.2013: Mechanism to clamp the mouthpiece firmly and leakfree against
the compression driver finished. We provided 3 M4 threaded holes in the M35x1,5
threaded nut to hold the compression driver in place. Seems we are running
out of stock materials in stainless steel... Order for stainless steel send
to Demar Lux. 35V / 160VA transformer (toroidal) ordered from Farnell.
- 29.04.2013: First tentative assembly... up towards a more definitive shaping.
This is what it looks like on the welding table:
With
the bell downward... And, with the bell upwards:
From the backside: 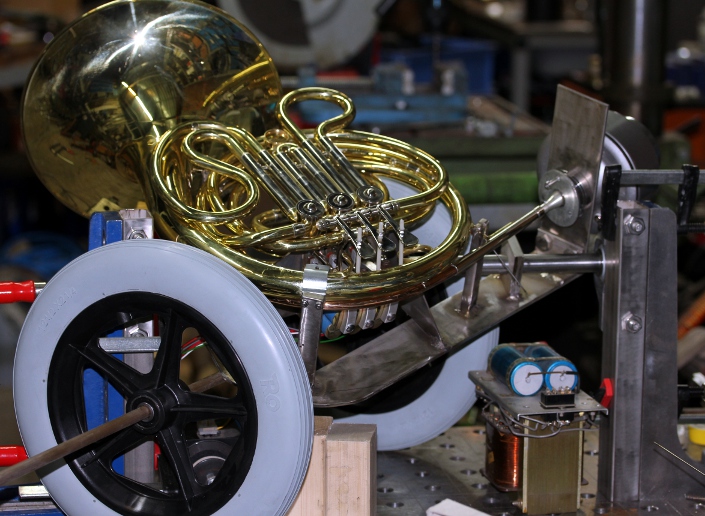
- 30.04.2013: The ordered toroidal transformer came flowing in from Farnell.
We can build up the solenoid power supply and test the bulb circuit.
- 01.05.2013: Working out and tests of the designs for the movement using
a bidirectional solenoid. HY2001 amps ordered from Farnell. Designs for a
round trolley worked out. Midihub board soldered together. Will we need a
position sensor here? With the trolley we have to wait until fresh stainless
steel stock comes in from Demar Lux.
- 02.05.2013: A full day of work on the mechanism to make the horn tilt...:
Some pictures:
The bidirectional solenoid draws some 2.5A from the 24V power supply but seems
to work properly.
- 03.05.2013: Experimental design for the placement of the electronic components.
- 04.05.2013: Power supply module 1 finished: using a Hans Klomp transformer
that had been sitting on our shelves for more than 30 years now... It has
split primary (2x 110V) and two secondary windings: 34V/1.4A and 5.5V/ 500mA
after the original label on the transformer. We measured, when connected to
our usual primary voltage of 238V, 36.9V and 6.22V on the secondary windings.
After rectification and a 4.7mF electrolytic the DC voltage, unloaded becomes
50V. With three valve solenoids pushed the current required will be 1.26A.
However there will be a maximum surge current of 2.28A when all three solenoids
are fired on the same moment. The duration of this surge is shorter than 25ms.
So given large electrolytic capacitors in the power supply, there is little
danger to burn out the power supply.
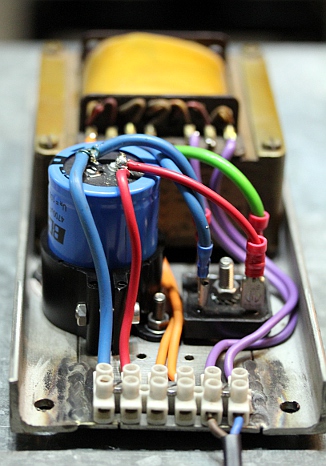
- 05.05.2013: We seem to get in trouble with the bulb design: it's awfully
hard to trace suppliers for both BA15s and BA15d bajonet bulb sockets. The
24V/10W bulbs themselves seem to be problematic as well. Further research
required... We could also use two 24V/5W bulbs in parallel, or, two 12V/5W
bulbs in series. Circuit overview:
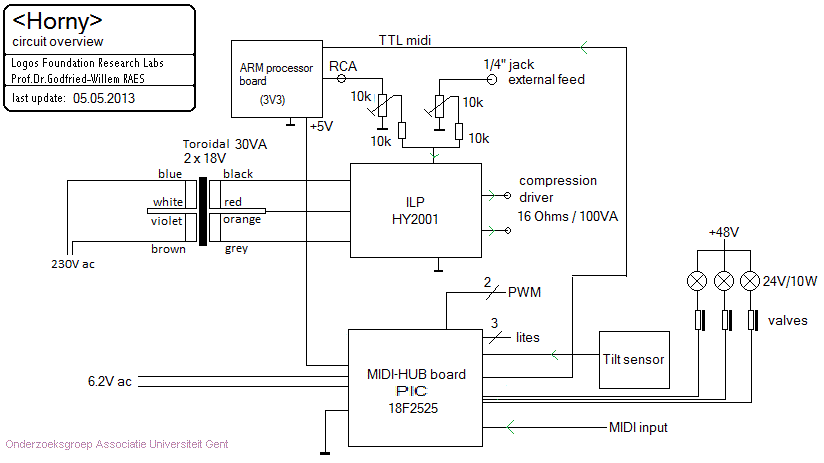
- 06.05.2013: Running out of professional quality 10k log potmeters for the
mixer circuit...
Power
amp assembly nearly finished. Light assembly with BA15d lamp fittings finished
and welded in place. First tests with the power supply and the 10W/24V bulbs.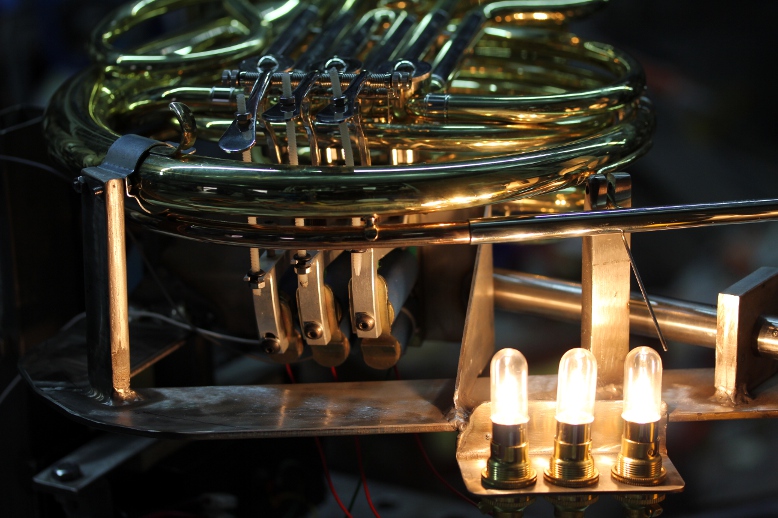
- 07.05.2013: Power amplifier module finished. We used two high quality 50k
log potmeters for the mixing circuit. Start coding for the firmware of the
midi-hub board, where we have to implement the fingering look-up tables as
well as the movement and some extra lights.
- 08.05.2013: Further code development for the 18F2525 pic on the hub board.
The fingering lookup tables, worked out after consulting with Hans Denayer,
can be found in this odt document.
- 10.05.2013: Working session with Johannes Taelman on the firmware development
on the ARM platform. The waveform to be generated by the driver should be
modelled after following formula:
The
values for s ought to be close to unity (a bit larger in fact) and require
a 16 bit resolution over the range. Above this, enveloppe shaping and formant
filtering will have to be implemented.
- 12.05.2013: Technical drawing scale 1:1 made for the welding works of the
underchassis and the placement of the circuitry. We can now take exact sizes
for the steel parts to be cut out directly from the drawing.

- 13.05.2013: Johannes Taelman finished the design for midihub board version
4. There are only slight changes as compared to version 3 from 2006: we now
have 2 analog inputs and 3 monitoring LED's for motor control and PID debugging
and adjustment. This is the image of the
new PC board. The complete circuit
looks like this.
- 14.05.2013: TIG Welding works on the mounting base, not yet the wheelbase.
The 1:1 drawing is an invaluable help here.
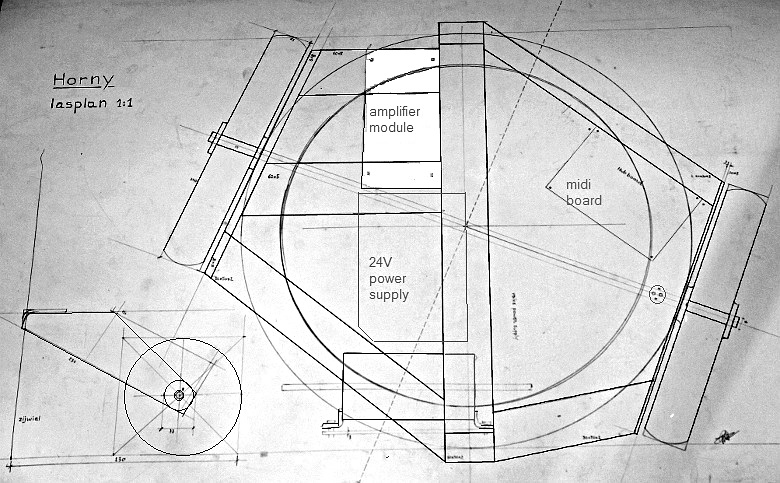
- 15.05.2013: Construction of the chassis for the 24V power supply module,
suspended from underneath the robot. This is constructed from 2mm thick stainless
steel, bend to a U-shape. It is bolted to the underchassis with two M6 bolts
and nuts.
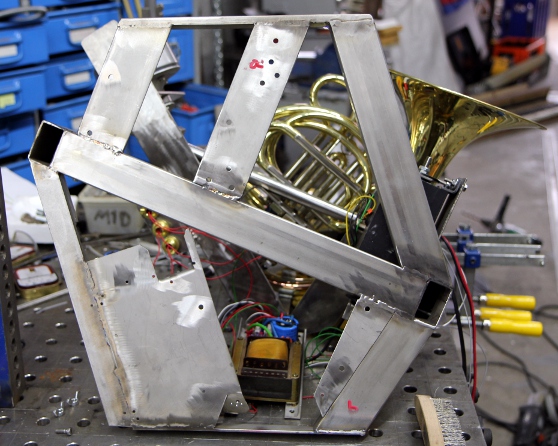
- 17.05.2013: Delivery of the ordered stainless steel is to be expected on
21th of may. So finishing the wheelbase has to be postponed it seems.
- 18.05.2013: Welding works on the 125mm diameter wheels:
- 19.05.2013: Further mounting and welding of the wheel base structure on
the rim.
Test assembly
of the complete robot. Mounting and soldering of the stabilized 12V power
supply for the lights. Seems we have to redesign the positioning of the 24V
power supply as the positioning as drawn in 2D is practically impossible:
either the wheel axis or the rim underneeth are in the way. Eiher we have
to find another way of mounting, or else redesign the entire power supply.
- 20.05.2013: A different way of mounting the 24V power supply found. Extra
bracket welded on the bottom structure.
The
power supply is now bolted on the chassis with two M6 bolts and nuts. It can
be taken out easily. Start wiring of all power supplies. Electric test, DC
voltages checked o.k. Wiring connectors to the midi-hub board. Note that the
board on the picture is not the one we will use in the final construction.
Sizes are identical though.
We
still have to make up our mind with regard to the lights to build into this
robot. The yellow 1W LED light on the back side is mounted. There is place
for one more 12V light and eventualy a single 48V tungten filament light.
Some kind of handle is still left to be designed as well. Waiting for the
newly designed piggy pack board fot the ARM discovery and the AXO firmware...
- 21.05.2013: At the drawing table... considering a handle. Wiring of the
compression driver finalized. Start bending works on the handle. This proves
more difficult than we thought, even using a Ridgid bending pump. The bend
shapers we have are only in 1/2", 3/4". 1" and 5 1/4"
gas pipe sizes not quite matching our metric stainless steel tubing.
- 22.05.2013: Protective cap made for the compression driver using a large
ladle in stainless steel. This is mounted on the driver with a single M6 bolt.
It also serves the double function of balancing the mounting cradle for the
horn. To avoid rattling, we applied a thin layer of Parabond compound on the
inside. Bend handle welded on. M8x70 bolts replaced on axles of the small
wheels. Engraved signature plate in brass mounted on the side with two M3
bolts. Welding of the wheel base to the chassis finished. Visually <Horny>
is now more or less ready. The mechanism still needs regulation and the firmware
has to be finished both for the valves and the compressor driver.
- 08.06.2013: News from Johannes: the piggy pack boards for the ARM development
board should be in production... Size will be Eurocard.
- 17.06.2013: Definitive stainless steel axle for the large wheels cut and
wheels mounted. Soldering work on a new midi hub board (version, 2013) started.
Further work on the firmware for the hub board controlling the valves.
- 18.06.2013: Soldering work on the midihub board finished. 74HCT14 schmitt
trigger inverters as well as 180 degree DIN PC mount entries reordered from
Farnell as we are running out of stock. Firmware version 1.0 loaded in the
18F2525 PIC controller on the midi hub board.
- 26.06.2013: Wheels fixed.
- 28.06.2013: The ARM board should be on the way from Johannes Taelman...
- 30.06.2013: Version 1.0 of the ARM firmware programmed.
- 01.07.2013: Holding board for the ARM board soldered and tested. Stainless
steel profile bend, drilled and mounted as a vertical support for the board.
Default parameter setting research for this preliminary version of the firmware.
- 02.07.2013: Holes drilled for mounting the ARM board assembly. This mounts
with two M5x16 bolts to the chassis. Movement tested. There is not enough
force as yet to bring the horn in an upward position if it starts from fully
down. Maybe we will have to balance the cradle better or else, to add a spring.
- 03.07.2013: It seems that we need to add a formant filter in the ARM firmware.
This filter ought to be tuned to a frequency range between 400 and 500 Hz.
Also the timbre of the instrument should be much more dependent on sound volume.
As a note gets louder, it should get more brassy. Finally we will have to
expand the dynamic range. Hub firmware upgraded to version 1.2 now, with implementation
of controller #100 for alternative fingerings. Bug discovered in the valve
wiring. The 5V supply voltage found to be marginal at 4.7V. The input AC voltage
measures only 6V. We either have to use a low drop type for the 7805 or use
another AC transformer. Failures discovered in the switching of the valves.
Only valve 3 seems to work as it should now. Must be hardware related as the
firmware performs to perfection on the test and programming board. Oddly enough,
as long as the PICkit2 programmer is connected, everything works fine.,..
- 04.07.2013: Further debug: apparently, as soon as the ground wire from the
programmer is connected to circuit ground, everything seems to run fine again...Apparently
there was no return line for the TTL midi input to the test board. However,
this does not explain why it's not working on the actual board. Let's check
the TTL buffers there... The power supply being low at 4.7V cannot be the
reason: first we tried with a sturdy 5V and the problem remains, furthermore,
after the spec sheet for the 18F2525, the supply voltage may be as low as
4.2V. Such low voltage might be not large enough to fully fire the IRL640
mosfets, but we do not even get pulses from the PIC. In any case, we ordered
a bunch of BA05CC0T low drop voltage regulators to replace the 7805 on the
hub board, even knowing that this is not the cure. After a full day of debugging
hard- and firmware, we could not trace any hardware problem. By inserting
assembly language instruction (btg's) in the code we could solve the problem.
Now firmware code version 1.4. This works even with the slightly low voltage.
Comments on this phenomenon and the cure can be found in the source code for
the midihub firmware.
- 07.07.2013: Wiring of movement solenoid corrected such that CC22=0 corresponds
to bell down and CC22=127 to bell upwards.
- 19.07.2013: Sockets for the festoon bulbs came in from Newark on line. So
the last missing light could be mounted on <Horny>. We use two 24V/5W
bulbs in series.
- 20.07.2013: Functional test of light mapped on note 122. OK.
- 26-28.09.2013: <Horny> presented at the BEAF (Brussels Electronic
Arts Festival), together with <Klar>, two robots using the Axo platform
to some extend.
- 29.09.2013: <Horny> returned safely from BEAF Brussels and took up
its place again in the robot orchestra.
- 28.10.2016: <Horny> on the road to Brugge for 'Iedereen Klassiek'
- 30.10.2016: <Horny> set up again in the orchestra and found fully
o.k.
- 22.10.2017: <Horny> joined the party at euRobotics in Brussels. However,
due to uncarefull treatment in transportation, it got an ugly bump on the
rim of its bell...
- 26.10.2020: <Horny> still in perfect condition. We started work on
a hunting horn as a component in the <Rumo> robot.
- 24.01.2021: The hunting horn became a robot for its own sake: <Hunt>.
- 22.07.2023: <Horny> returned safely from the open air tango performances
at the Ghent Feasts.
- 15.09.2023: <Horny> left for a trip to Berlin were it performs with
the robot orchestra in the Zeroth Law production at the Deutsche Oper, Tishlerei.
- 02.10.2023: <Horny> returned safely from its trip to Berlin.
- TO BE DONE:
- code revision of the ARM firmware with physical modelling of the mouthpiece
drive. This can use the Axo platform.
- improve fluency of movements
- add a small preamp between the ARM and the ILP to increase the gain with
a factor 2 to 4.
- writing out the user manual
- construction of a flightcase
- upgrade PIC firmware to take profit if the much better implementation of
periodic events developed for the <Whisper> robot.
- tracing a new good looking nude model for some more
robody pictures with <Horny>. Candidates?
Robody picture with <Horny>:
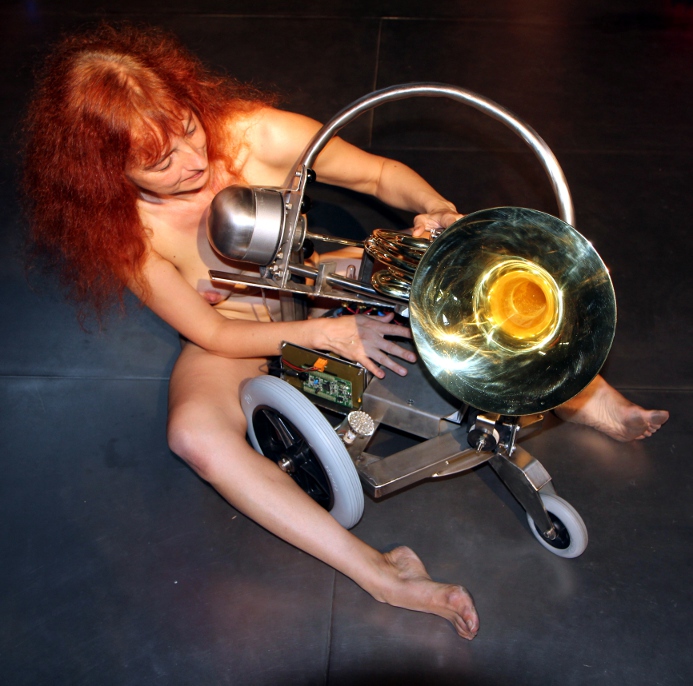
Last update: 2023-10-11
by Godfried-Willem Raes
Technical drawings and data
sheets:
Horn:
Arnolds & Sons, type AHR-301,
serial number 121267. Arnold Stoelzel Gmbh, Postfach 5523, D-65045 Wiesbaden,
Germany. Website: www.arnolds-sons.de
Mechanical parts & construction:
Ball bearings and flange holders
in cast iron for the horizontal movement: INA RASEY20-N, LAG135030273 (from
MEA)
Wheels: Spoke wheels with polyurethane
tires: Large wheels Tente, 350 mm diameter, width 45mm, axis: 12mm. Small wheels:
Tente 125 mm diameter, width: 35mm, axis: 8mm..
All chassis parts made from
stainless steel AISI 316 or AISI 304
Electronic circuitry:
Overview: 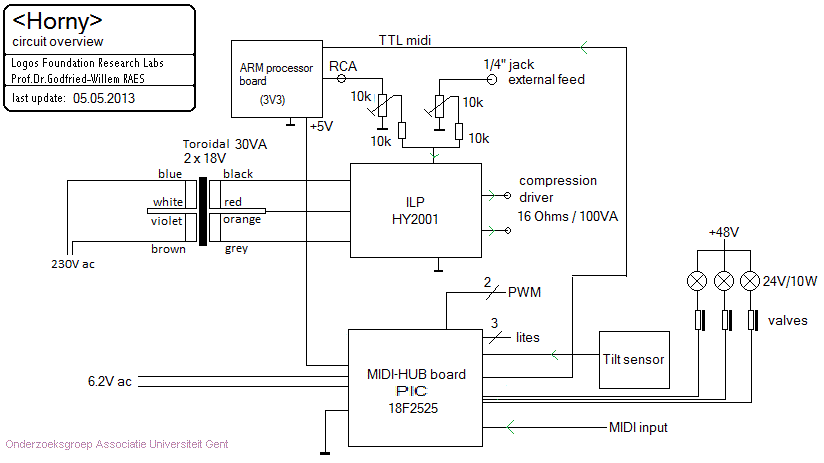
Midi-hub board:
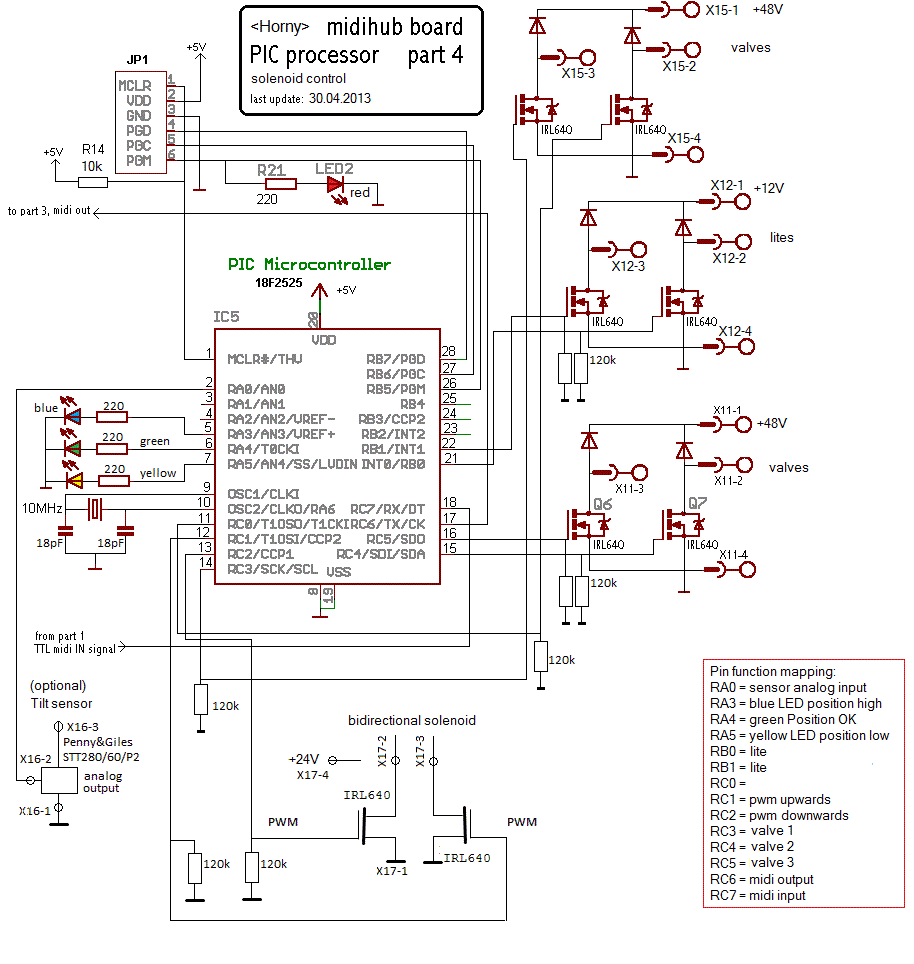
This board controls the three valves, the movement solenoids and three lights.
It also hold the components for the +5V power supply.
Driver generator:
A development board for an ARM microprocessor is used here:
An STM32f4 discovery board.
Power supply:
This is the picture of the valve power supply module:
Compression driver unit: Model PADU 100, power rating 100W, impedance 16 Ohms.
(Made in China) We have measured this component carefully and found the impedances
in function of applied frequency as follows:11.4 Ohms @ 100Hz, 23.68 Ohms @
1kHz, 26.7 Ohms @ 10kHz and 45 Ohms @ 25kHz. The acoustic load does influence
the measured impedance at 1kHz over a 1:2 range: with the mouth completely closed
it measures 32.8 Ohms and with the mouth completely opened but without any resonator,
15.35 Ohms. This phenomenon does not occur for the very low neither for the
very high frequencies. The measurements were performed with our Hameg LCR meter,
model HM8018. The frequency response is 100Hz to 10kHz. The thread for mounting
is 1 3/8"-18 TPI. The 100W rated power of this driver
must be understood as 'peak power', and thus in true rms terms would correspond
to ca. 35Watt sine wave. Thus the maximum voltage that can be applied to the
driver is 25V.
Solenoid valves:
Two different approaches were carried out. After evaluation, we decided to
go for the second approach, using Laukhuff solenoids, as they operate much more
silently than the tubular solenoid solution.
1.- Tubular solenoid assembly: (abandoned)
Solenoid type used for the valve pushers: Lucas Ledex (now distributed by Saia-Burgess)
STA type 195207-228 (13.8 V DC @ 100% duty), 10 Watt, 7.8 N @ 5mm with 60 degree
plungers. 26 mm diameter, height 52 mm. The required anchor displacement for
the horn valves is 12 mm.
Note on the push tubular solenoids used to activate the rotary valves:
The following specs are valid at 20 degrees Celsius. Maximum holding force
is 29 N
13.8V |
100% |
10 W
1.166 A.turns
|
17.78 mm in 41 ms
2 N starting force
|
2.54 mm @ 10 N |
19.6V |
50%
max. ON-time: 470"
pulsed: 360"
|
20 W
1.649 A.turns
|
17.78 mm in 32 ms
3 N starting force
|
2.54 mm @ 18 N |
28.0V |
25%
max. ON-time: 120"
pulsed: 32"
|
40 W
2.332 A.turns
|
17.78 mm in 22 ms
9 N starting force
|
2.54 mm @ 27 N |
44.0V |
10%
max. ON-time: 32"
pulsed: 8"
|
100 W
3.688 A.turns
|
17.78 mm in 15 ms
12 N starting force
|
2.54 mm @ 40 N |
These solenoids may not deliver enough starting force to start the valve movement.
Thus our design for pulse-hold solenoid drivers may be used here. This was the
approach in <Bono>. This approach necessitates a bipolar power supply.
The positive hold voltage can be reduced to 10 V, the negative velo-pulse voltage
should be between 24 V and 36 V.
2.- August Laukhuff pull down magnet assembly : Type 300810, having a traject
of 10mm at a force of 10 Newton. (24V types have R=57 Ohm and draw 420mA current).
We made this assembly as it performs inherently more silent than the tubular
solenoid version. However the starting force is only marginally large enough
to activate the valves. Hence the circuit with the series bulbs working as voltage
dependent resistors from a 48V supply voltage.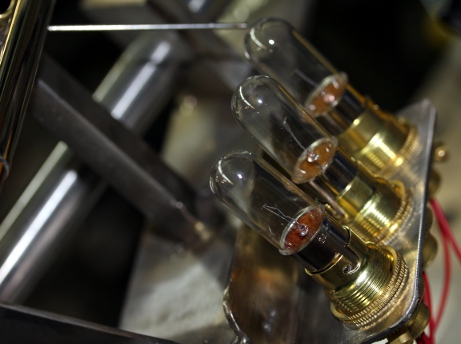
3-- The horizontal movement makes use of a single large August Laukhuff bidirectional
solenoid operated from 24V. The two windings have a DC resistance of 12 Ohms,
hence the current drawn is 2A. Since we never activate both coils with the same
power at the same time, a 2.5A power supply ought to be powerfull enough here.
Lights:
- Yellow 1W LED spotlight on the back (12V), with reflector.
- Yellow 1W LED spotlight on the front (12V), with reflector.
- Bulbs in series with the valve solenoids: 24V / 10W (bought from AST nv,
06.05.2013) type L54701615T, with BA15d socket. Cold resistance of this type
is 9 Ohms. These are normal tungsten filament types, halogen types would be
a better replacement, for they have a much lower cold resistance. The sockets
(BA15d) are brass, type HUP3401.
- Tungsten light 48V, frontal. This light consists of two festoon socketted
bulbs 24V/5W connected in series.
References:
- Beauchamp, J.W., "Analysis of Simultaneous Mouthpiece and Output Waveforms
of Wind Instruments" . In: j-aes, 1980, Preprint No. 1626,
- Benade, Arthur .H., "Fundamentals of Musical Acoustics". Ed.:
Oxford University Press, 1976.
- Fletcher, N.H. & Tarnopolsky, A. "Blowing pressure power and spectrum
in trumpet playing" In: J. Acoust. Soc. Am., volume 105, number 2, part
1, 1999.
- Martin, Daniel W., "Lip vibrations in a Cornet Mouthpiece", In:
J.Acoust.Soc.Am. vol13 . 1942
- Raes, Godfried-Willem, "Kursus Akoestiek", Ghent University College
1982/2013, Internet: http://www.logosfoundation.org/kursus/4023.html
- Raes, Godfried-Willem, "Expression
control in musical automatons", 1977/2013,
- Smith, Bob H., "An Investigation of the Air Chamber of Horn Type Loudspeakers",
in: The Journal of the Acoustical Society of America 25, 305-312 (1953); https://doi.org/10.1121/1.1907038