Microtonal
Musical Robot
Research project on
the development of new tools for musical expression at the University
College Ghent - School of Arts
|
<Asa>
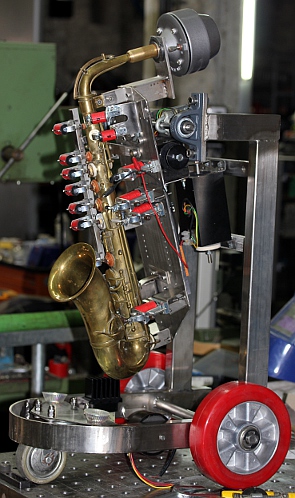
an automated alto saxophone
Godfried-Willem
RAES
2013-2014
|
The instrument used to start off this robot building project was an alto saxophone
made by Ancienne Maison Muller, Louis Cousin successeurs, in Lyon, France. This
is the label:
We
presume it dates from the early interbellum, as it must have been made after
the death of the late Louis Cousin. Certainly not older than 1890. We started
by thoroughly cleaning and restauring the instrument and bringing it back to
full playing conditions. This it what it looked like as we got it:
As
it is a pretty old instrument, it misses some features in the mechanism typical
for more modern instruments, such as automatic octave keying, palm keys and
a few trill keys. An advantage as it turns out, for an instrument to be automated.
This is the fingering for <Asa>:
Following
the recipe applied in most of our wind-instrument robots sofar, we decided to
drive the saxophone using a membrane compression driver followed by an acoustic
impedance convertor. This convertor with its typical double coned design with
a capilary connecting both cones, had to be calculated anew, as it had to fit
the drive requirements for an alto saxophone. Our design is an attempt to match
as closely as possible the characteristics of a normal mouthpiece with a reed
for such an instrument. The design resulted in following drawing,
which we constructed in real on the lathe from a piece of solid brass rod. The
picture shows both our impedance convertor and the modeled mouthpiece:
For obvious reasons, the quite complicated internal bore cannot be made visible
in a photograph. To make the central conical part, we grinded an existing 12mm
drill to a conical shape of the required proportions on the lathe, putting the
drill bit rotating in the chuck of the lathe and grinding it off with an angular
grinder.
For the implementation of the valves, we could build further on the experience
we had build up during the realisation of our <Klar> robot. In fact, the
case of a saxophone is even a bit easier as there are less valves that have
to be operated. The two octave valves appeared to be dispensible, as with our
driver mechanism the octaves actually even sound better without activation of
these keys. So the double octave valve on the crook as well as the lower thumb
operated valve could be left closed all the time. This left us at first sight
with no more than 16 valves to be automated. However the native mechanism on
a saxophone tends to be rather noisy. Therefore we decided to replace as many
of the valves, pads and mechanisms as possible with solenoid driven pads acting
directly on the tone holes. Therefore we unsoldered the posts holding the mechanism
for valves 9,10,11,12, Av2, 15,16, 17 and 18. The mechanism on the crook for
the double octave, although not required, was left in place as well as valve
8, as we found no place for a directly driven solenoid pad here. The 'automatic'
valves Av1 and Av2 thus also required solenoids, bringing the total up to 18
valves.
Power supply voltages and currents:
- + 12V, 10A dc for the valve solenoids (with 100% duty cycle) and the lights
(PWM controlled)
- bipolar -25 - + 25 V , 0.8A for the compression motor driver (30VA transformer)
- + 5 V/ 500 mA for the three processor boards and the logic. (10VA transformer)
- + 24V, 4A dc for the movement solenoids
Midi Mapping and implementation:
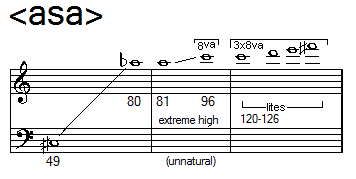
Midi channel : 3 (counting 0-15).
Midi note range: 49-92. Note on, velocity is implemented and has a wide control
range.
Note Off commands are required, but can be dropped for pure legato playing.
A note-off releases the valves and unpowers them. It starts the fast decay section
of the mouth driver.
The lights are mapped on notes as follows:
- note 120: Yellow LED spotlite, front left
- note 121: Yellow LED spotlite, front right
- note 122: Bright red LED lite, front
- note 123: Four white Viesmann SMD-LED's on the front.
- note 124: white LED lite strip on the saxophone assembly
- note 125: blue quad LED module on the saxophone assembly
- note 126: LED- strip yellow, front left on the saxophone assembly
- note 127: round white LED lite on the backside of the saxophone.
With velocity values between 1 and 126, the lights will be flashing with speeds
proportional to the velocity value. To switch them just on, use velo = 127.
Velo=0 switches them off.
Controllers:
Controller 1: Wind controller, steers the amount of noise in the sound. Default
= 3. Advised setting: 6
Controller 2: LFO3 frequency applied to the filter. Default = 2. Advised setting:
1
Controller 3: Vibrato depth (LFO1 amplitude). Default = 20. Advised setting:
20, to turn vibrato off, set this controller to 0.
Controller 4: Vibrato speed. (LFO1 frequency). Default = 8. Advised setting:
8
Controller 5: Tremolo depth, amplitude modulation. (LFO2). Default = 0. Advised
setting: 2
Controller 6: Tremolo speed. (LFO2 frequency). Default = 0. Advised setting:
14
Controller 7: Global volume control. Can be used for crescendo and decrescendo
effects whilst notes are sounding. This also affects the sound color of the
instrument. Default = 80
Controller 16: Note attack speed controller (0= slow attack, 127= fast attack)
. Default setting: 100. Advised setting: 20
Controller 17 is used to control the maximum sound level reached after the attack
time. This controller is always larger than or equal to the level set by the
velocity byte. For sfz or staccato playing, this controller must be set to high
levels and the velocity byte kept rather low. Default setting: 127. Advised
setting: 120
Controller 18 is used to control the speed of the transition between the attack
level once reached and the sustain or hold value set by the velocity byte.(0=
slow transition, 127= fast transition) default setting: 90. Advised setting
85
Controller 19: is used to control the release time after reception of a note
off. Here again a value of 0 will give a slow release whereas a value of 127
will give a very fast release. Note that with very low values, the note may
not even turn off completely. Default setting: 96. Advised setting: 89. Note
that if real note-off commands are used, the release value sent with them, if
this value is not zero, will override controller 19, such that the value of
controller 19 will be set to 128-release value.
The following graph gives a picture of the mutual dependencies of controllers
16 to 19.
Controller 20: Basic tuning of the instrument. The range is + or - a semitone.(Defaults
to value 64 for A=440Hz)
Controller 22: Vertical inclination controller (gradual). (0-63= backwards,
64=central, unpowered, 65-127= forwards). (default = 64)
Controller 23: Left-right inclination controller (discrete) (0-63= left, 64=central,
unpowered, 65-127= right). (default = 64)
Controller 25: Filter cut off frequency. Default = 62. Advised setting: 100
Controller 26: Filter resonance amount. Default = 90. Advised setting: 81
Controller 27: Echo mix. Default = 0. Only use this for experimental sounds,
as it can generate multiphonics.
Controller 28: echo feedback. Default = 0. Only use this for experimental sounds,
as it can generate multiphonics.
Controller 29: LFO3, filter depth. Default = 20. (large values give a wha-wha
effect) Advised setting: 10
Controller 30: Valve release time out.(only used for code development) By default
this takes the value 100.
Controller 31: Does the same thing as aftertouch: fingered vibrato. However,
it does not require to be sent again and again in a sequencer. The parameter
sets the fingered vibrato speed. Default = 0
Controller 40: Bendrange for the pitchbend. 0= no bending, 1=+/- 50 cents. Default
= 1.
Controller 43: Wait time for vibrato start after reception of a note-on command.
Note that in legato playing, vibrato will continue. The wait time starts again
after a note off is received. Default = 100.
Controller 44: Wait time for the tremolo (AM modulation) to start after a note-on
command. Default = 10. Advised setting 19
Controller 66: Power on/off switch (0 = off, any other value is on). Power off,
resets all controllers to their cold-boot values.
Controller 100: special fingerings , bit settings for valves 1 to 7
Controller 101: special fingerings, bit settings for valves 8 to 14
Controller 102: special fingerings, bit settings for valves 15 to 18
Controller 123: switches the sounding note off, unpowers the movement solenoids,
dims all the lights. Does not reset any controllers.
Pitch bend: implemented with a range of a semitone (a quartertone up or down).
The coding for a fragment of a quartertone scale (here shown for the <Heli>
robot, but its identical for <Asa>) is as follows:
Most good sequencer
software (such as Cakewalk or Sonar) uses the signed 14 bit format. Note that
one unit of the msb corresponds exactly to a 0.78 cent interval. To convert
fractional midi to the msb only pitchbend to apply, follow following procedure:
if the fractional part is <= 0.5 then msb= 63 + (FRAC(note) * 128), if the
fractional part is larger than 0.5, we should switch on the note + 1 and lower
the pitch with msb= (1-FRAC(note)) * 128.
Technical specifications:
- sizes: width 440 mm, depth 500 mm, height: 900mm.
- weight: 40kg (estimate)
- transportation: requires a specific flightcase. Flightcase sizes: 480 x
570 x 926 mm. For mounting and packing details, refer to the maintenance instructions
at the bottom of this page.
- Power: 230 V ac / 130 W
- data input: Midi, RS485 and/or UDP/IP over Ethernet.
- Tuning: based on A = 440 Hz (within 1%). The tuning can be adjusted.
- Ambitus: 49-102
- External audio input: 0dB line level, 1/4" phone
jack.
- Insurance value: 14.000 Euro.
Design and construction: dr.Godfried-Willem
Raes
Collaborators on the construction of this robot:
- Kristof Lauwers (GMT-player implementation & lookup tables)
- Johannes Taelman (ARM firmware coding, Axo project)
Music composed for <Asa>:
- Bram Stadthouders "Stuk voor elektrische gitaar and <Asa> robot
(2017)
- Godfried-Willem Raes "Symphony #3, Die Jahreszeiten' (2017)
- Godfried-Willem Raes "Linac Elekta" (2020-2022)
- Jonas Runa
Pictures taken during the construction:
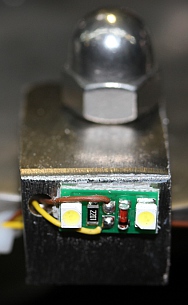
Nederlands:
Robot: <Asa>
een nederlandse beschrijving is niet beschikbaar.
Construction Diary:
- 27.03.2013: First sketches and designs. Digging up of an old decent alto
sax from our collection. We bought it years ago on the local flea market in
Ghent as a replacement for the beautifull ancient Buffet-Crampon instrument
we owned before but that got stolen in the University Hospital (UZ), as we
lended it to a medical doctor (Marc Vandeweghe) working there... He never
properly compensated us for the loss. The maker of this replacement saxophone
is pretty obscure: Louis Cousin in Lyon. Google didn't reveal any more information,
neither is Cousin mentioned in the Groves dictionary of musical instruments
nor in the MGG..
- 29.03.2013: First provisions made in GMT in order to implement test code
for <Asa>, Resources recompiled and extended.
- 01.04.2013: Repair of leaking pads on the saxophone. We used soft brown
Loctite silicone for glueing the pads rather than the usual shellack.
- 03.04.2013: Decision made to use the ARM discovery board as a driver base
for the compressor driver:
This is the board Johannes Taelman is working on for his AXO project. A
project description is here. (link to PDF file).
- 03.04.2013: New connectors made by IMO came in from Farnell. These should
replace the Weidmueller parts we have used sofar. A note
on the connectors used in our robots added to ther Logos site.
- 06.04.2013: Further repairs on the instrument.
- 08.04.2013: Designs drawn for an x-y movement for <Asa>. Instead of
using stepping motors, we could also use two bidirectional linear solenoids,
as movements are expected to be rather slight.
- 09.04.2013: Construction of a suitable impedance convertor fitting a PADU
compressor driver on the lathe:
On the picture, the turned brass piece is shown as well as - for comparison-
an altosax mouthpiece:
Obviously we cannot show the quite complex internal bore of our impedance
convertor on the picture.
- 11.04.2013: Start working out fingering tables for <Asa>. We need
at the most 18 valves but could suffice with 16 if we leave out the octaving
valves.
- 21.04.2013: Further cleaning up of the saxophone.
- 22.05.2013: Different solutions for the realisation of X-Y movement drawn
out.
- 23.05.2013: Asa project taken up again. We will try to replace as many pads
as possible with solenoid valves acting directly on the tone holes, for this
solution guarantees the most silent operation of the mechanics. However, due
to the placement of the holes, this is not always possible. Obviously if we
replace valves 9,11 and 12 with pads, we have to implement a pad for tone
hole AV2 as well, as this hole is closed whenever either 9,11 or 12 are closed.
Valve 15 and 16, as well as AV2 removed from the instrument. This alone already
seriously reduces the force required to close valves 9,11 and 12. The height
of the standoff to the mounting plate should be minimum 55mm. A brass part
may have to be made and hardsoldered lengthwize to the bottom of the instrument.
If we automate both AV1 and AV2, the total number of solenoids required will
be 18.
- 24.05.2013: Further study of the mounting problem for this instrument. There
simply is not enough space to clamp it properly.
- 25.05.2013: Construction of a mounting system. We can use a ring clamp made
of brass on the neckpiece, an M10 bolt through the straphole and, after drilling
a 5mm hole in it, a stud on the thumbrest. Unfortunately, during drilling
that hole, we caused a small bump in the instrument... Resoldering required.
Positioning off the required components on the welding table in our workshop:
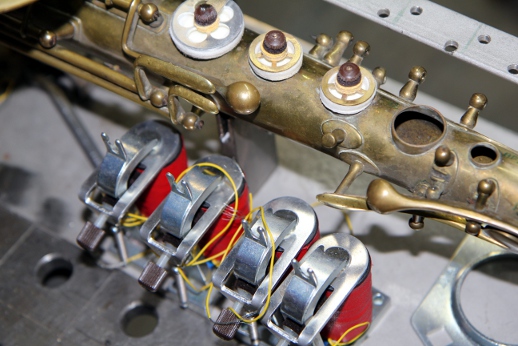
- 26.05.2013: Cutting and drilling of the bottom mounting plate for the instrument.
Construction of the holder for the compression driver. Construction of a holding
bridge for the solenoid pad drivers on the opened toneholes. These components
can be seen on the pictures:
AV1 valve removed from
the saxophone.
- 27.05.2013: Solenoids for organ building ordered from August Laukhuff (type
300900). Awaiting deliveries of steel, solenoids and PC boards... Studs for
mounting the solenoids for valves 3 and 4 prepared.
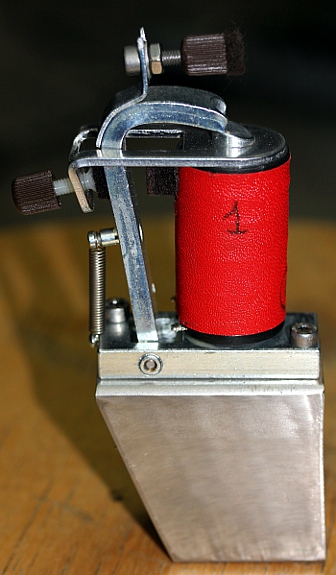
Fingering solenoid
assembly for valves 7,6 and 5 started. Pads for the valves 15, AV2, 12, 11,
10, 9 and AV1 mounted with Loctite 5920 brown silicon.
- 28.05.2013: Finishing work on valves 5,6 and 7.
This
is a single unit.
Fresh
stainless steel flew in from Demar-Lux.
- 29.05.2013: Further work on the automation of valves 15 and 16, these tone
holes being situated on the side of the instrument, they pose some specific
mounting problems. A new supply of 24 Laukhuf valves, type 300900 (Tonventileinheit)
came in. Fresh load of midi-hub PC-boards came in from Eurocircuits. Neck
piece holder welded on, using a piece of stainless steel T profile 40x40x3.
All mounting holes drilled in the bottom plate. Polishing and grinding.
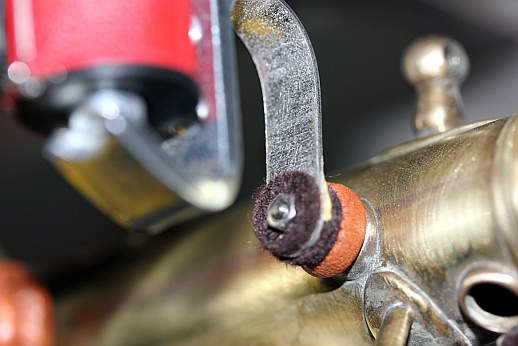
- 30.05.2013: Definitive mounting of the solenoids on the bottom plate. Adjustment
of the pads, checking for leaks. Silencing mechanics with felt strips and
pads. Design of a gallows type suspending construction for this robot with
its two degrees of freedom movement.
Some of these pictures
posted on Facebook in the album robot details on my fan-page. Large in-between
clean-up of the workshop... Start mounting of the ball bearing for the horizontal
(left-right) movement. Axis made from a M20 stainless steel bolt. Through
this bolt we drilled a hole, 12mm diameter, to accomodate the axis for the
forward-backward movement. We still have to find out how to design the automation
of these two degrees of movement freedom. Mounting of the Laval-cone with
the capilary on the saxophone crook and mounting of the Padu compressor driver.
For sealing we used brown Loctite gasket silicone.
- 31.05.2013: Purchase of cast iron ball bearing holders for the 12mm axis
on the gallows. Design for the gallows worked out.
- 01.06.2013: Start construction of the gallows. Horizontal: 50x30x2 length
160mm, vertical 50x30x2 length 525mm. The cast iron ball bearing holders mount
on a piece of 30x10x 125mm with 10mm holes, using two M10 bolts. This piece
is welded on the horizontal profile. Experiment to hold the place for the
movement solenoids on a 130mm x 130mm x 3mm plate with two U bolts, size M10.
Can we prevent this to rotate under load conditions? If not we either have
to weld it on -to the detriment of demountability- or find another solution.
Back wheels selected from out stock. These will be 200mm diameter types with
red polyurethane tires. Axis: 20mm. The construction will be almost a copy
of what we did for <Ob>.
- 02.06.2013: Recovering from a serious burn caused by touching a just welded
piece. Large blister... First tentative vertical mounting on the welding table.
Measurement of required forces for the movement. Construction of the left-right
movement with a bidirectional solenoid. This solenoid should be powered on
24V DC.
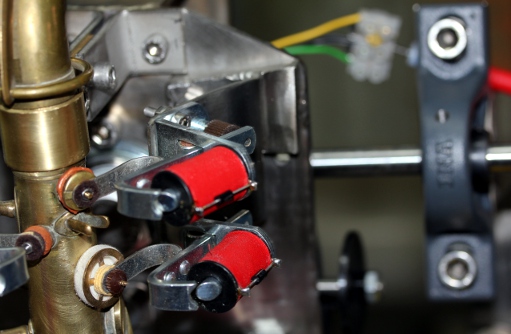
- 03.06.2013: Calculations and drawings for the wheelbase, taking into account
space requirements for the power supplies and the electronics. Test mounts
for the solenoid driving the forward-backward movement. First lay out and
assembly of the 12V/24V 300VA power supply. Holder bars for the back solenoid
drilled and welded in place (30x10x250mm).
- 04.06.2013: Positioning of the ILP amplifier module and the toroidal transformer
to power it up. Wheel construction started. Bending works for the front side:
semicircle, 165mm radius, 6mm thick. Ridgid tube bending pump modified for
work on flat materials. The new rollers are mounting on the base with two
M24x160 bolts.
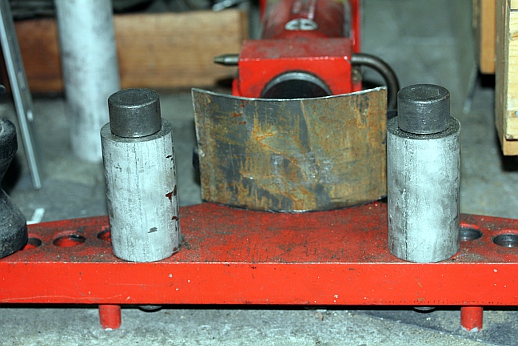
- 05.06.2013: Design and welding of the front side of the robot. Should get
two bright yellow LED spotlights. Mounting plate for the front wheel cut and
drilled. 30x30x3 L-profile cut out with slots for 6 midi DIN plugs, mains
power entry and on/off switch. Welded on the back side of the wheel base.
We find no place to accomodate an audio input jack here. Power transformer
for the 5V power supply finds a place on the backplane with the midi hub board.
Encountering spacing problems to fit the ARM board... we may have to make
2 layers of circuitry on the backside.
- 06.06.2013: Main axis welded in place after making 2 mm wide grooves on
the lathe, for circlips to secure the large wheels in place. Wiring of the
12 V/24 V 300 VA power supply. This power supply is a removable assembly,
it can be taken out of the robot from underneath and mounts with 4 M6 bolts
on a 20 mm stand-off.
Position found for both the toroidal transformer and the ILP30 module on the
chassis. It may not be possible to mount a frontwheel with a brake mechanism
though. A difficult task on the menu: lifting the Asa assembly and mounting
it on the wheelbase to weld both together... More than two hours of mounting
work on the welding table to bring everything in place for this final welding.
Operation succeeded. Big difficulties encountoured in an attempt to mount
the first 200 mm wheel... apparently the 3 mm thick 20 mm diameter seamless
tube we used as an axis is not very precise 20mm... Even 50kN of force was
not enough to mount the wheel.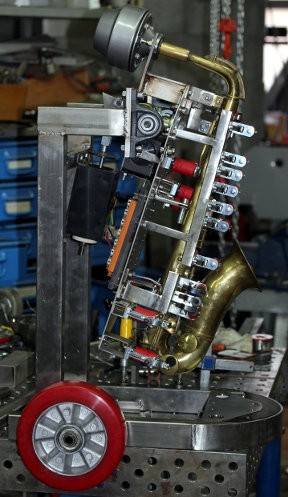
- 07.06.2013: First wheel mounted with the brute force approach... After this
operation we noticed a slight deformation of the seemless tube on the other
end where the second wheel ought to come. Grinding, filing, sanding en polishing
of the tube to prepare it to take the second wheel. Unfortunately we cannot
do this on the lathe. Precize measurement revealed that the diameter of the
tube is 20.04 mm and not 20.00 mm! Dummy front wheel temporary mounted. Second
wheel mounted in place. Mounting of the power supply transformers.
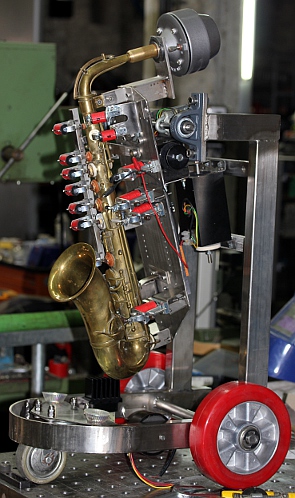
- 08.06.2013: Wiring of the mains power lines: on/off switch (unipolar), transformer
primaries and 3-prong connector. Mains ground connected to chassis of the
robot.
Midi hub board
soldered. The resistors R23 and R22 in the circuit diagram substituted with
BY229 diodes in a 2-pin TO220 package. The diodes D5 and D6 substituted by
a wire bridge. The complete circuit diagram
is available here. Start coding for the PIC18F2525 firmware on the midi
hub board, controlling four lights and all motion of the robot. The source
code can be found here.
- 09.06.2013: Further writing of the firmware for the midi hub board. Soldering
of the valve microcontroller board, using a PIC 18F4620 processor.
Note
that on this board we do use the power supply and voltage regulator circuitry,
so it has to get 6V ac power on connector X11. The board is wired for operation
with TTL-midi input signals received on connector X6. Double diodes D10, D11,
D12, D13, D14 not mounted yet, as we may need to operate lights from a different
voltage. Electric and functional tests of this board o.k. Start design of
the firmware for the valve-control board, using the same code model as for
<Klar> and <Fa>. Back mounting plate in transparent polycarbonate,
8mm thick, for the valve board finished.
- 10.06.2013: Further working out of the fingering tables.
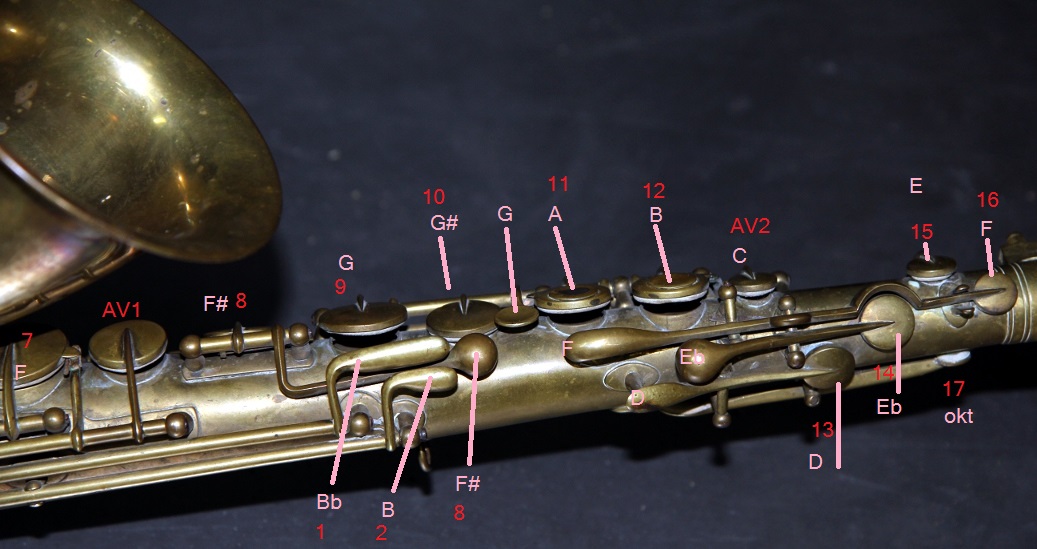
- 11.06.2013: Wiring of the ILP amplifier to the toroidal transformer as well
as to the input (using screened cable) and output to the compression driver.
Wiring of the movement solenoids to the midihub board. Powerlines to the valve
board. AC-lines to hub board and valveboard.
- 12.06.2013: Welding of a 10mm wide wire bundle holding profile to the side
of the gallows construction. Wiring of the valve solenoids to the 28-output
board.
Wire colors
correspond to valve numbers in our numbering scheme, except Av1 and Av2, wherefore
red/green wire color is used. To avoid confusion with the positive supply
lines, valves 2 and 12 are wired using orange/red colored wire.
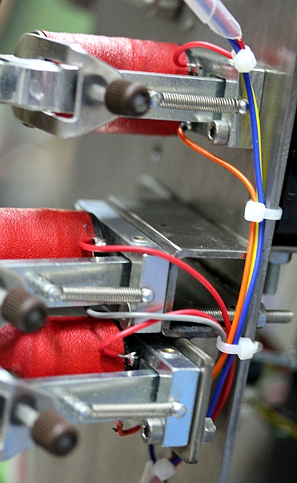
- 13.06.2013: Code added to GMT in order to make testing possible. Further
wiring works. Firmware version 1.0 programmed into the midi-hub PIC controller.
First tests of the electronics and the firmware: O.K. The movements are pretty
smooth and we may not need to implement a movement/position sensor at all.
The valve tables have to be reprogrammed though. The movement control seems
to work fine. Polycarbonate back plate for the valve board finished and mounted.
Slots sawn out for the lights. Board carrier constructed for the ARM board
assembly, in top of the hub board. This is fixed with two clamps on the wheel
axis with a piece of 20x20mm L profile. The carrier plate for this board is
cut out from 8mm thick polycarbonate. Waiting for the ARM boards to fly in...
- 14.06.2013: Designing light effects and general lighting for <Asa>.
Redrawing the nose part. Further work on the fingering lookup tables. Red
LED light assembly calculated and soldered:
Since
the LED's work at 30% of their rating, lifetime expectancy even without cooling
should be pretty good.
Stainless
steel light holder cut out and welded for these red lights. Blue LED assembly
(Conrad car tuning part) mounted on saxophone carrier as well as a strip of
white LED's (OMC) rated for 12V. Since these strips are not autoadhesive,
we used a thin layer of Parabond High Tack to glue them on the chassis.
- 15.06.2013: Detailed working out of the fingering tables such that we can
make and finalize the lookup tables. We will extend the range up to note 102,
this being the highest note found documented anywhere in the saxophone literature.
Fingering tables converted in bit positions for the PIC controller ports.
- 16.06.2013: Although maybe not usefull, we did also implement fingered vibrato
after the model developed for <Fa> and applied earlier as well in <Klar>.
There is definitely no historical base as to the use of any kind of fingered
vibrato on the saxophone family though. The instrument only came into existence
after the period this practice was common. Firmware for the 18F4620 upload
and placement of the programmed board in the robot. Construction of two SMD-LED
holders for the front of the robot. These mount on the frontal wheel nuts.
Round white LED assembly glued on the backside.
Yellow
LED strip added on the front side.
All light outputs are confined now. Documentation updated accordingly and
implementation in GMT worked out (code module g_MM.inc).
- 18.06.2013: The ordered 1.7W 32-LED yellow spotlights for the front part
came flowing in from Conrad. We mounted them immediately. The orientation
of the lights is fixed with some Parabond glue from the underside on the lamp
assembly.
- 25.06.2013: Johannes Taelman came along to show the results of PC board
fabrication using his self made laser drawing machine for boards. The results
after etching look quite good. Of course this way, we cannot make a solder
mask.
- 30.06.2013: ARM board assembled on the carrier board. Serious problems in
soldering this one as the insulating lines between the copper pads are way
too fine. A solder mask is really no luxury. First version of the firmware
programmed. <Asa> can play its first notes and scales...
- 01.07.2013: First tests and research on parameter optimalisation for the
ARM firmware. Prelimirary advised controller settings added to midi implementation.
Do not stick to this, as these values will change with an improved version
of the firmware.
- 27.09.2013: Start construction of a flightcase for <Asa>, as <Asa>
has to go to the Venice Biennale. Stainless steel L-profiles 30x30x3 as a
base. The frame is a TIG welded structure.
The bottom plate
is 2mm thick stainless steel and is welded on the profiles.
- 28.09.2013: Flightcase construction. Special wood for the side panels ordered
from Flightcase-brico.be.
- 29.09.2013: Mechanism designed and constructed to block all movement on
Asa during transportation.
This is how it should be mounted on the <asa> robot prior to transportation:
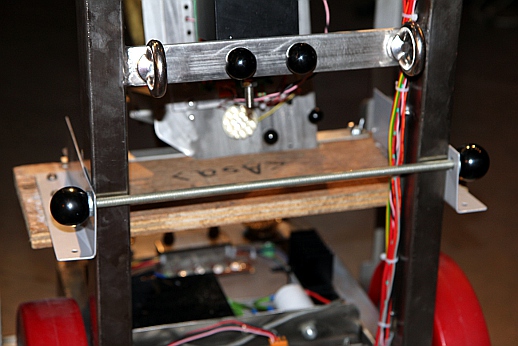
- 30.09.2013: Further work on the flightcase. It should be ready soon as <Asa>
is expected to perform on the Venice Biennale on october 12th.
- 03.10.2013: Plywood panels delivered, so we can go on with the construction
of the flightcase. Jonas Runa at work on <Asa> during his artist-in-residence
stay at Logos.
- 04/10.2013: Further construction of the flightcase. All panels mounted together
with the strong handles. Clamping system designed and documented.
- 04.10.2013: Flightcase for <Asa> finished and tested with the robot.
This is how it fits:
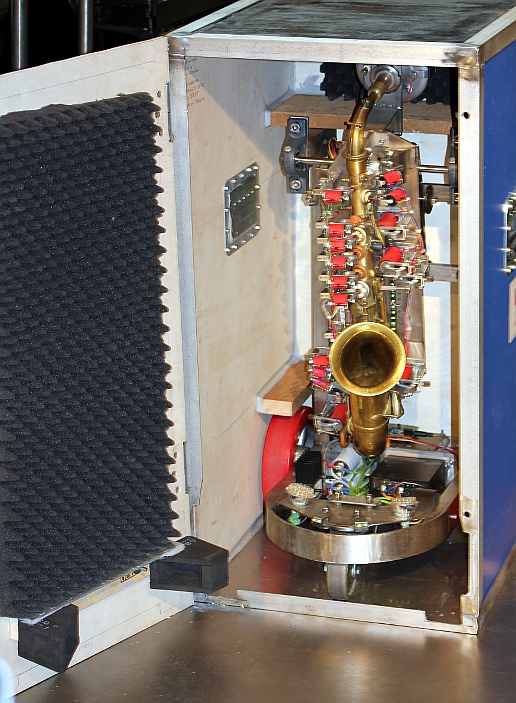
- 09.10.2013: <Asa> left this morning for its appearance on the Venice
Biennale on october 12th...
- 28.07.2015: Power supply leads to the valve control board found broken off.
These should be replaced with a more flexible kind of silicon wire. Wiring
repaired
- 09.12.2015: a check of the firmware for the fingering and the valves seems
indicated, as they fail to work as they should for some reason. The implementation
of the aftertouch must have a minor bug sonewhere.
- 11.12.2015: Firmware upgraded to version 1.3 for the valve board. However,
there seems to be something wrong with the midi signal. The board is not getting
midi... Debug required. Something wrong with IC1 (7414) on the hub board?
The ARM chip is getting midi as it should. Problem solved: the Schmitt-trigger
midi buffer chip (74HCT14) was found defective caused by a short during movement
of the saxophone. We insulated the heads of two bolts underneath the board
with felt washers now. Firmware uploaded with version 1.3. Asa is fully operational
again.
- 14.12.2015: Light and movement documented
for all robots.
- 26.09.2016: <Asa> transported to Berlin for participation in the 'Wir
sind die Roboter' Festival.
- 03.10.2016: <Asa> fully checked on its return from Berlin. No failures
found.
- 28.10.2016: <Asa> on the road to Brugge for 'Iedereen Klassiek'.
- 30.10.2016: <Asa> set up again in the orchestra and found fully o.k.
- 01.08.2017: <Asa> on the road to Liepaja Letland),
- 09.08.2017: <Asa> returned safely from Liepaja.
- 13.07.2018: <Asa> joined the party for the opening of the Ghent Feasts
at Sint-Jacobs.
- 22.07.2023: <Asa> returned safely from the open air tango production
at the Ghent feasts, Baudelopark.
- 14.09.2023: <Asa> joined the orchestra for the Zeroth Law production
by Gamut Inc at and in the Deutsche Oper Berlin.
- 02.10.2023: <Asa> returned safely from Berlin.
Robody pictures with <Asa>:
|
Last update: 2023-10-09
by Godfried-Willem Raes
Technical drawings and data
sheets:
Mechanical parts & construction:
- Bearings for the front/back movement: INA type GG.ASE03, cast iron with
12mm ball bearings.
- Bearing for the left/right movement: INA type, 20mm ball bearing.
- Front wheel: Pivoting wheel with brake and red polyurethane tire, 100x40mm,
Kaiser & Kraft order nr. 760529
- Back wheels: 200x 60 with red polyurethane tires.
- All chassis parts made of AISI 306 stainless steel.
Fingering table for the low octave, notes 49-64 (Bb to C# for saxophonists):
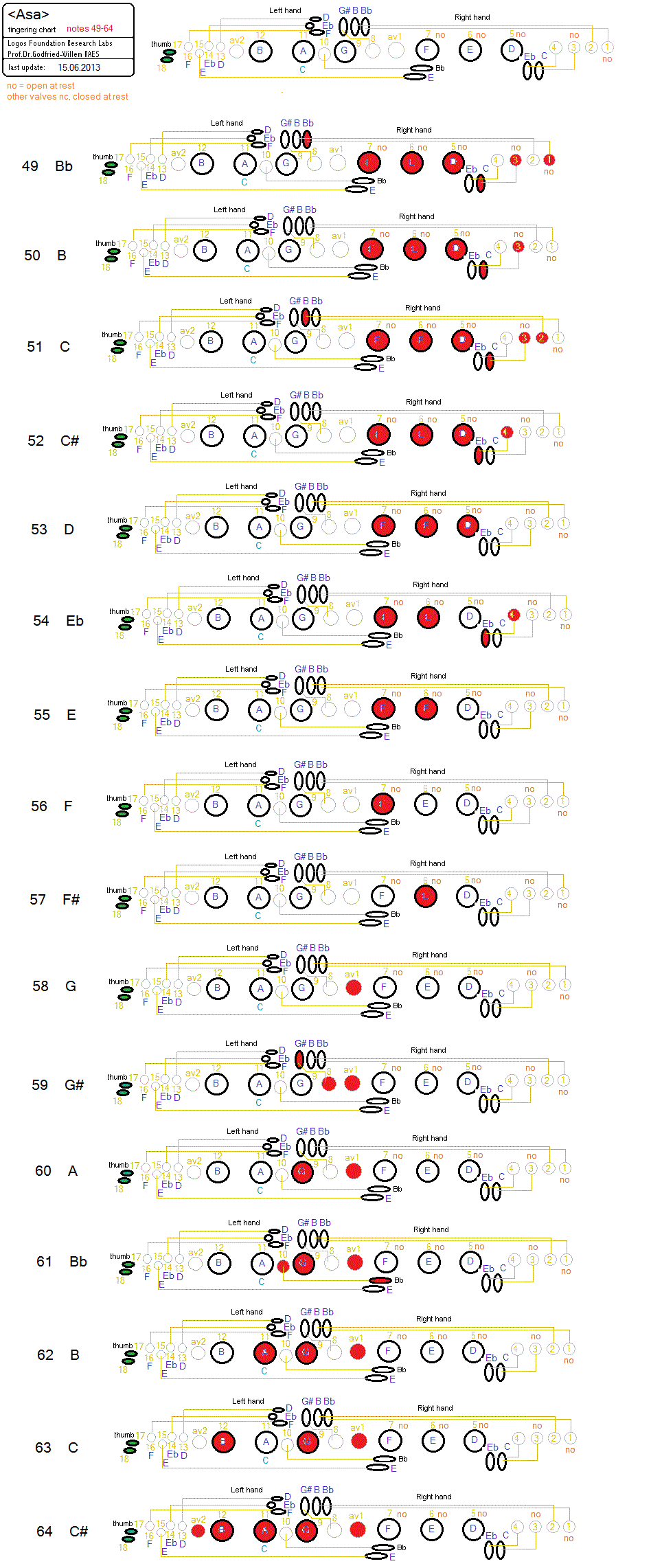
Fingering table for the second octave, notes 65-80 (Bb to C# for saxophonists):
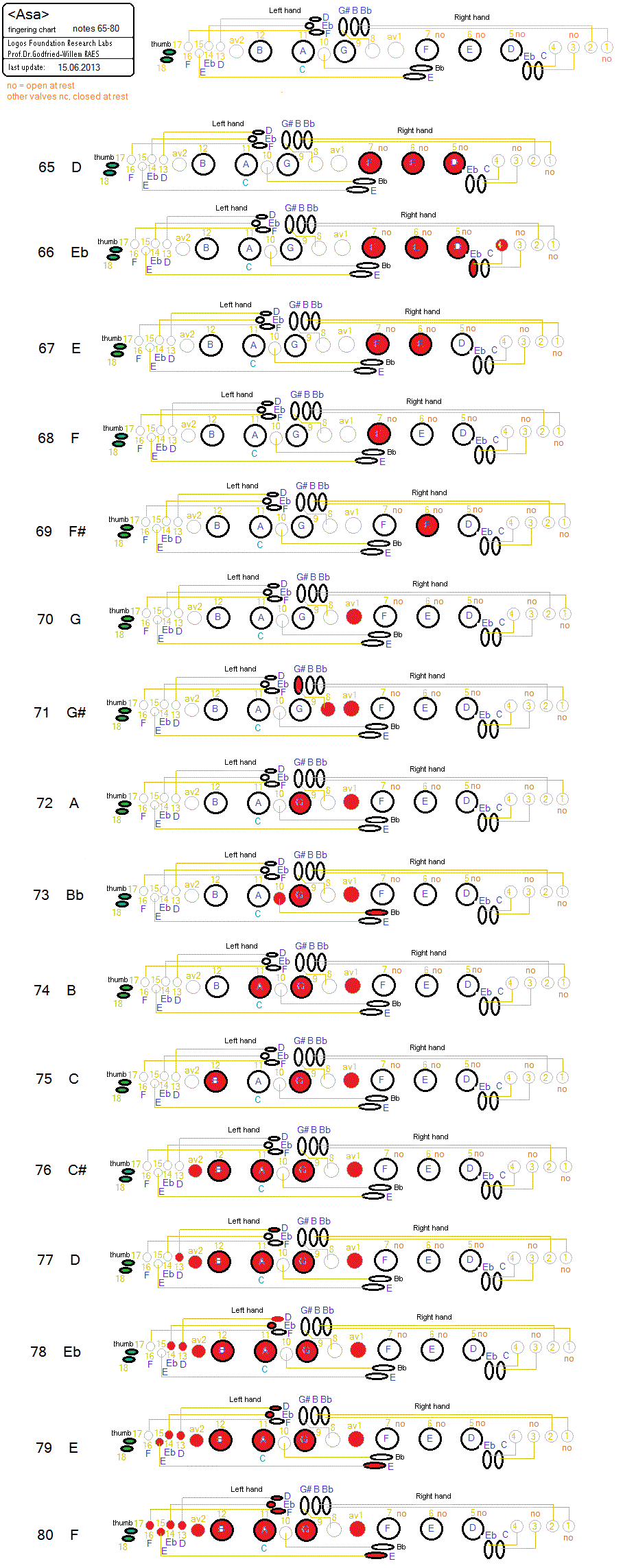
Fingering table for the lower, middle and high altissimo notes 81-96 (F#6 to
A7 for saxophonists):
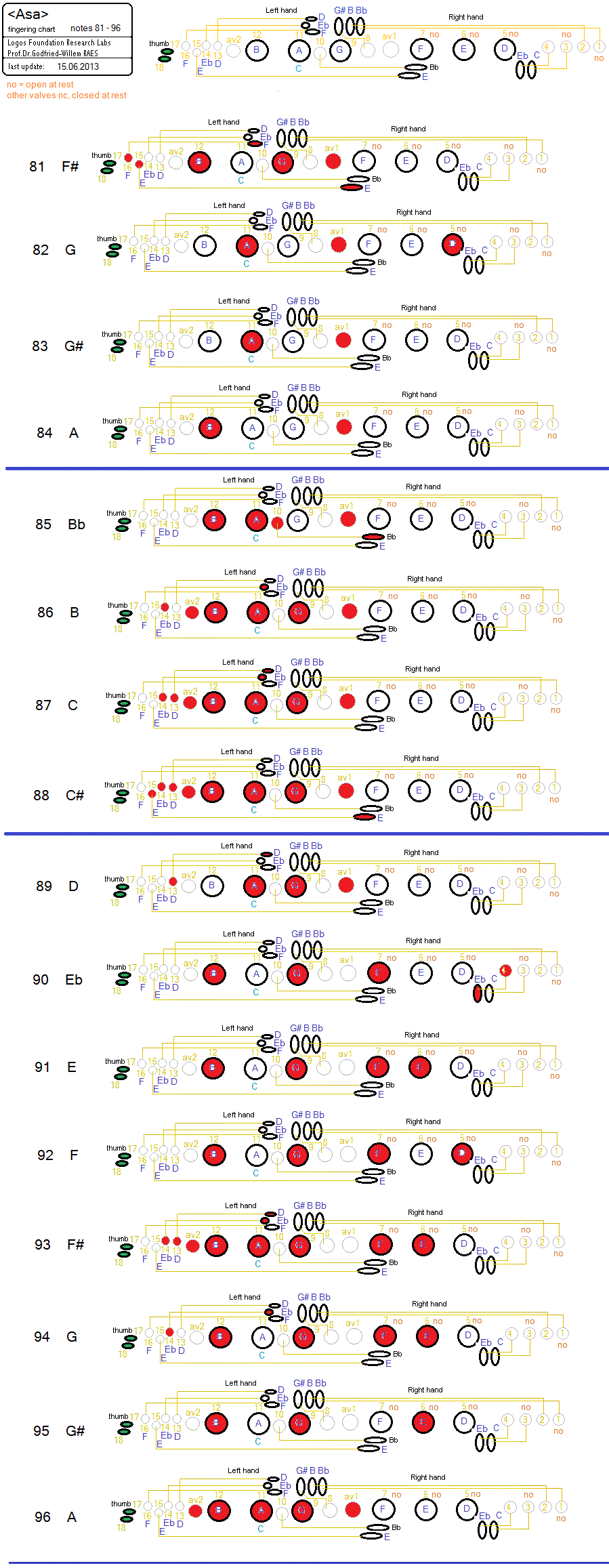
Fingering table for the extreme high notes 97-102 (Bb7 to Eb8 for saxophonists):
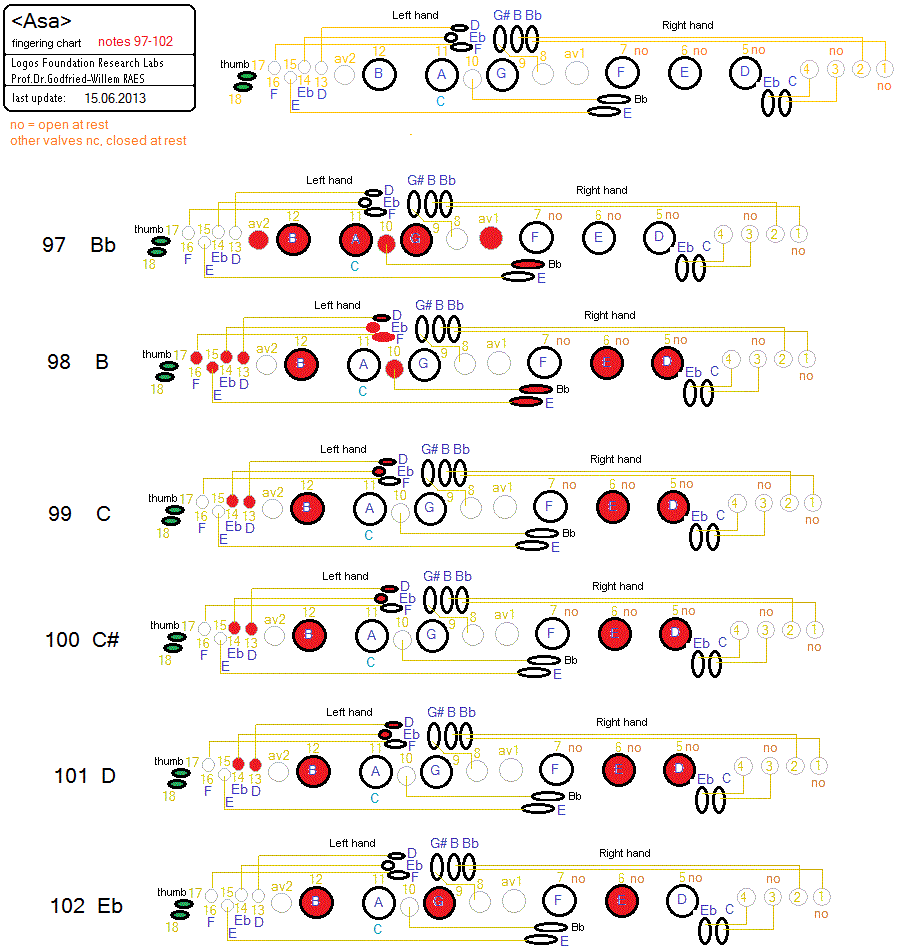
Connectors
Midi-hub board:
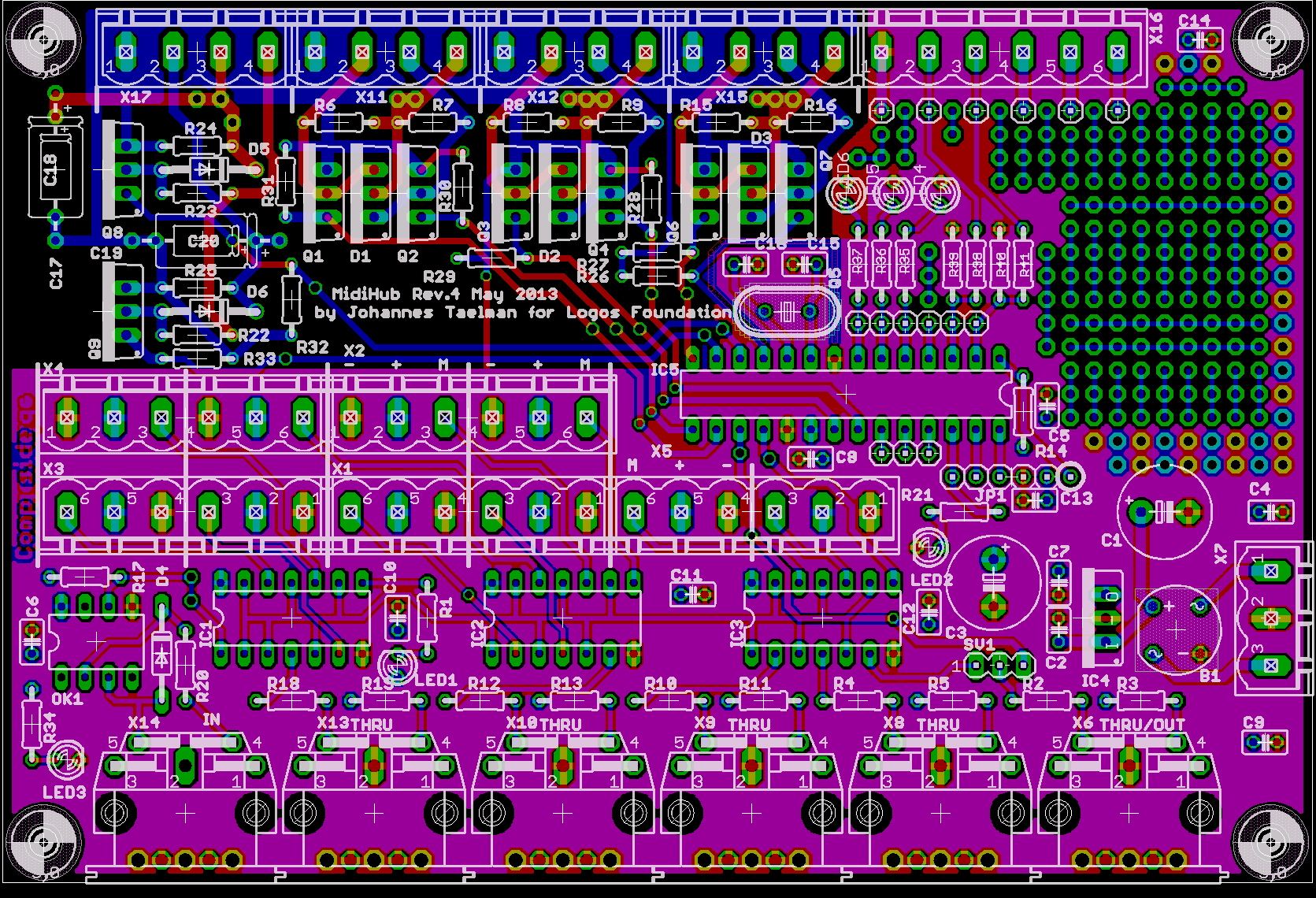
Circuit drawing:
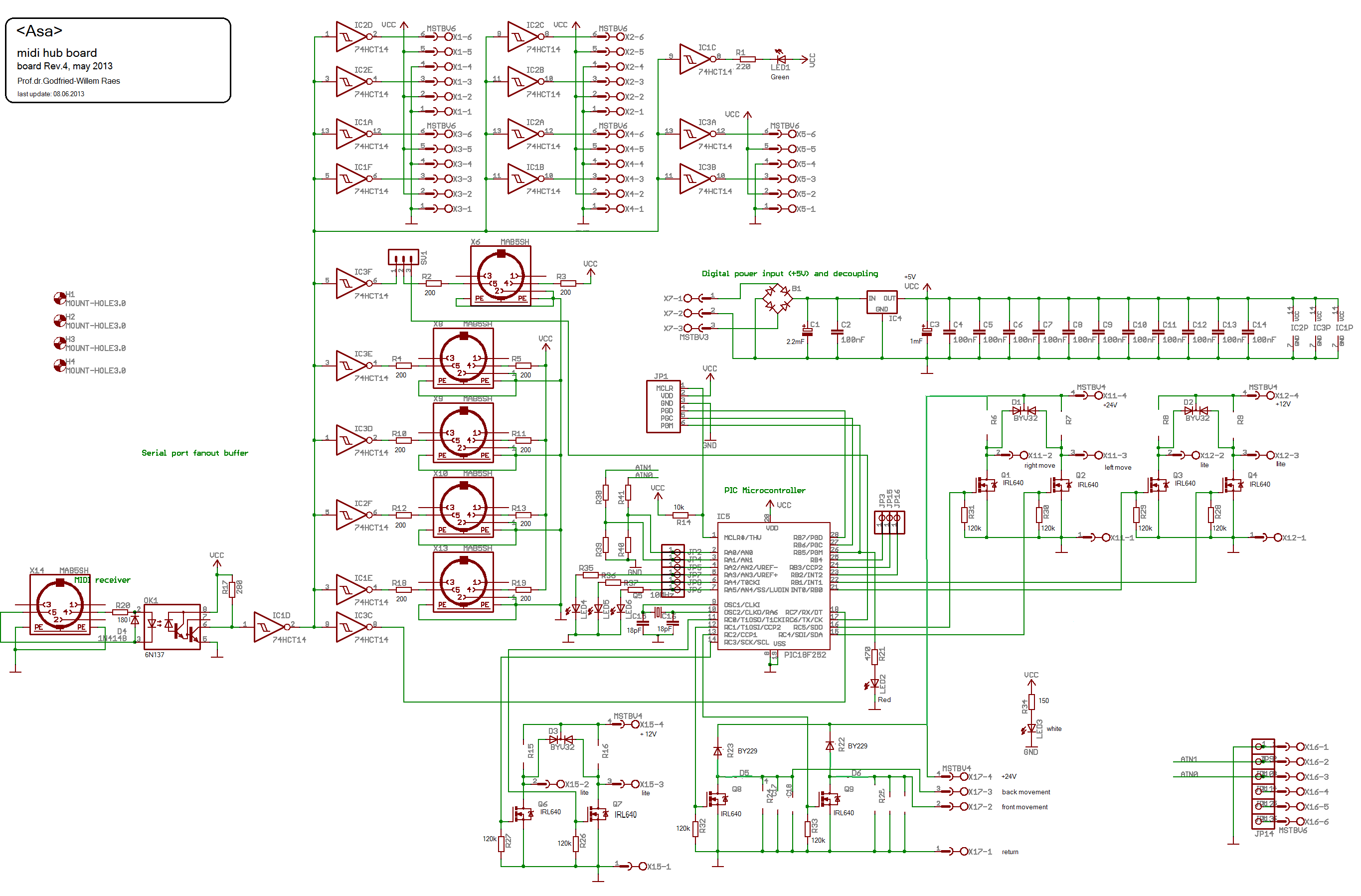
Firmware for this board. (Hex dump)
Valve board:
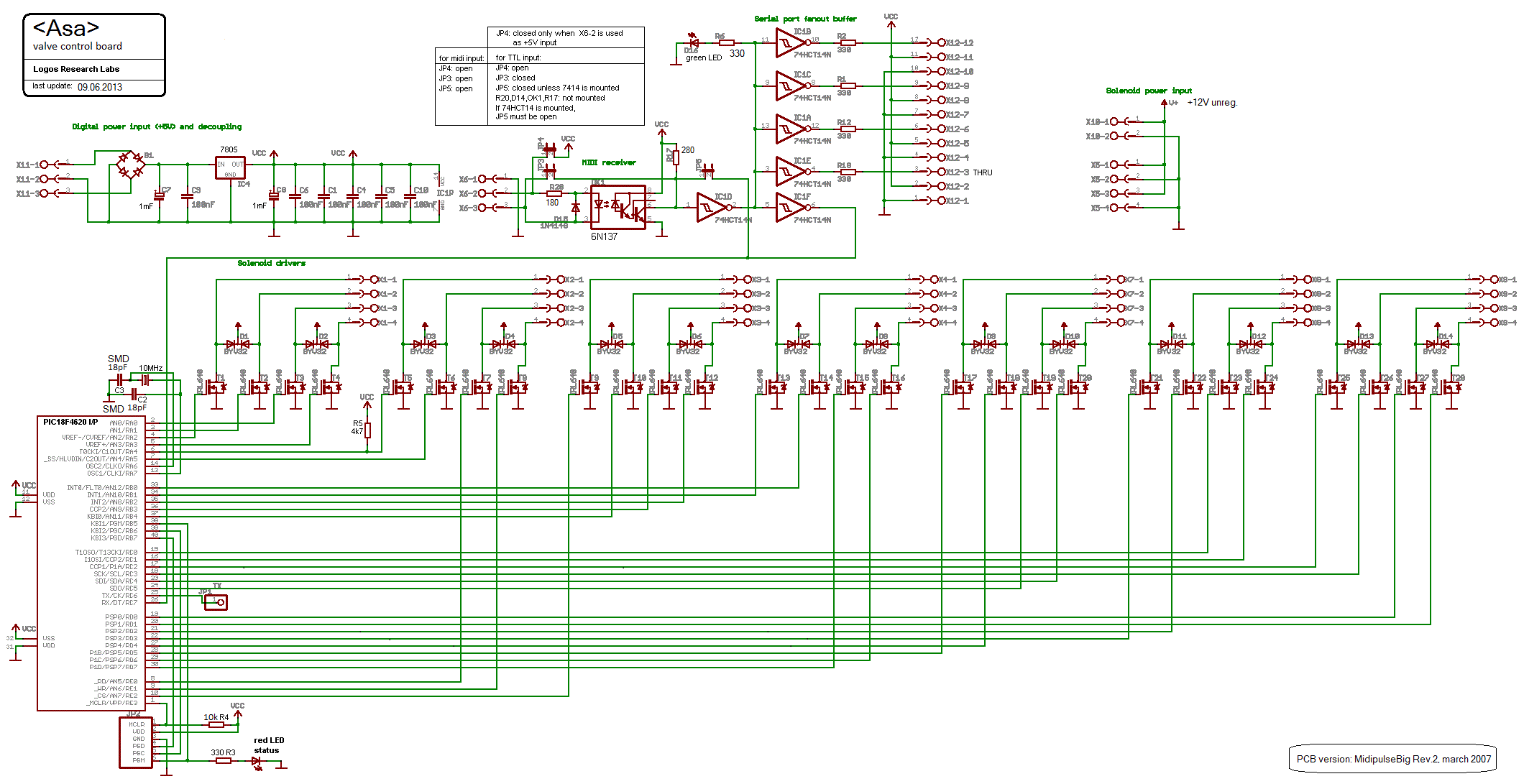
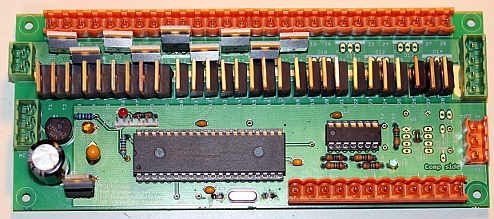
Firmware for this board:
Driver generator:
ARM discovery board:
Firmware for this board developed by Johannes Taelman as part of the
AXO project.
Power supply:
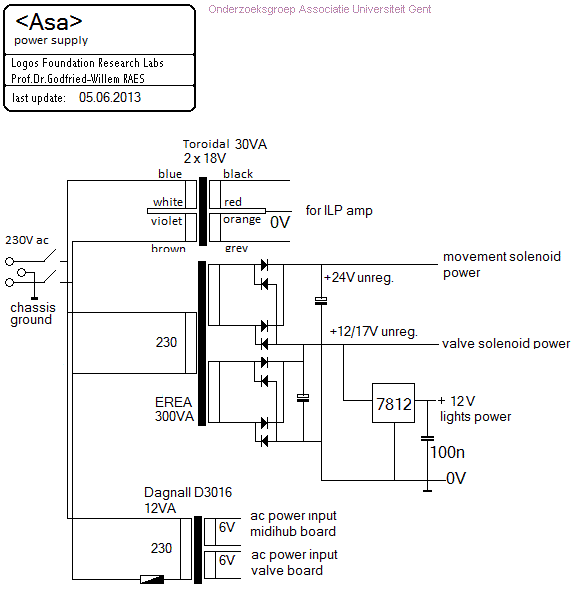
Dagnell transformer ordered from Farnell, order nr.116-6160. Mounting with
4 M3 bolts on the chassis.
Erea transformer: Type E212SC300SK, rated 300VA, two secondary windings, each
11.6V / 12.3A. Primary 230V.
Compression driver unit: Model PADU 100, power rating 100W, impedance 16 Ohms.
(Made in China) We have measured this component carefully and found the impedances
in function of applied frequency as follows:11.4 Ohms @ 100Hz, 23.68 Ohms @
1kHz, 26.7 Ohms @ 10kHz and 45 Ohms @ 25kHz. The acoustic load does influence
the measured impedance at 1kHz over a 1:2 range: with the mouth completely closed
it measures 32.8 Ohms and with the mouth completely opened but without any resonator,
15.35 Ohms. This phenomenon does not occur for the very low neither for the
very high frequencies. The measurements were performed with our Hameg LCR meter,
model HM8018. The frequency response is 100Hz to 10kHz. The thread for mounting
is 1 3/8"-18 TPI.
The impedance convertor designed for this driver was sized after following
sketch:
This part is mounted on the saxophone and on the Padu driver using brown Loctite
gasket silicone.
Wheels:
- Back wheels: 200 mm diameter, 60mm wide, red polyurethane heavy duty tires,
axis 20mm with ball bearings.
- Front wheel: 100mm diameter, 40mm wide.
Solenoid valves: (3 types for the valve operations):
August Laukhuff types as used for organ building:
Tonventilmagnet, August Laukhuff nr. 300900, 12/14V, 30 Ohm, 470mA . Force:
6 - 7.5N.
Ventilscheibenmagnet, August Laukhuff nr. 300701 (19mm), 300703 (21mm), 300704
(25mm), 300706 (30mm), 300708 (35mm). 12/14V, 75 Ohm, 190mA. 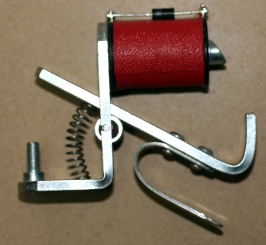
Wippmagnet, August Laukhuff nr. 300600, 12/14V, 75 Ohm, 190mA 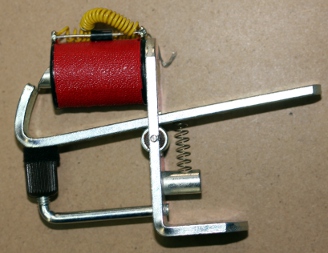
Kleiner Trakturmagnet: August Laukhuff, 24V (used for horizontal movement).
DC resistance of the windings:
The forward-backward movement makes use of a single large August Laukhuff
bidirectional solenoid operated from 24V. The two windings have a DC resistance
of 12 Ohms, hence the current drawn is 2A. Since we never activate both coils
with the same power at the same time, a 4A power supply ought to be powerfull
enough to feed both solenoids.
Lights:
two yellow LED spotlights, Paulmann, 12V, 1.7W on the front, oriented upwards.
Ordered from Conrad. Mapping on notes 120 and 121.
1 red LED assembly:
Mounting behind the front wheel. Mapping on note 122
2 dual white SMD Led assemblies pointing to the front. Viesmann, type 6018,
ordered from Conrad. 12-16V. Mapped on note 123.
1 White LED strip on the instrument assembly. (9 white SMD LED's) OMC part
no.1226698. http://www.omc-uk.com. Mapping on note 124
1 Blue LED assembly, 12V. Conrad Electronics. Mapped on note 125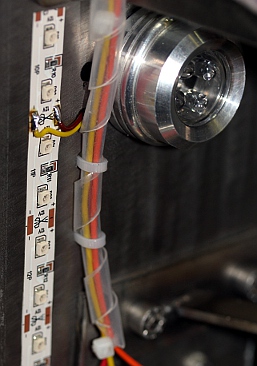
1 Yellow LED strip, 12V on the front, left of the saxophone carrier plate.
Mapped on note 126
1 Round white LED assembly, 1W mounted on the backside, 12V. Mapped on note
127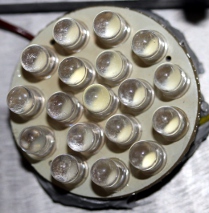
Transportation, packing and mounting instructions for <Asa>
<Asa> has a flightcase specialy designed for its transportation. Prior
to placing the robot in the case, it should be fixed such as to block its movement
completely. A special part is made to do this:
First
insert this part carefully between the instrument and the vertical poles. Next
insert the M8 threaded rod through the holes on the back, secure with the two
bakelite spherical knobs with internal M8 thread. Do not forget the thick washers
on both ends.
Next bring
the L-profile in place such that the instrument is clamped. Secure the profile
to the wood plate using the two M6 x 40 mm bolts and the wingnuts provided.
No tools required. Once
this has been done, the robot can be driven vertically -in its normal playing
position- in the flightcase. The door of the flightcase should be closed and
locked with two M12 bolts. Do not overtighten these bolts as the thread in the
side panels is only 3 mm thick.
References:
- Beauchamp, J.W., "Analysis of Simultaneous Mouthpiece and Output Waveforms
of Wind Instruments" . In: j-aes, 1980, Preprint No. 1626,
- Benade, Arthur .H., "Fundamentals of Musical Acoustics". Ed.:
Oxford University Press, 1976.
- Haine, Malou "Adolphe Sax", ed. Universite de Bruxelles, Bruxelles
1980 (ISBN 2-6004-0711-5)
- Raes, Godfried-Willem, "Kursus Akoestiek", Ghent University College
1982/2013, Internet: http://www.logosfoundation.org/kursus/4023.html
- Raes, Godfried-Willem, "Expression
control in musical automates", 1977/2015,
- Springer, George H., "Maintenance and repair of wind and percussion
instruments",ed.:Allyn and Bacon Inc., Boston, 1976. ISBN: 0-205-05012-3
- Smith, Bob H., "An Investigation of the Air Chamber of Horn Type Loudspeakers",
in: The Journal of the Acoustical Society of America 25, 305-312 (1953); https://doi.org/10.1121/1.1907038